Digitale Nachrüstung für bestehende Maschinen und Anlagen
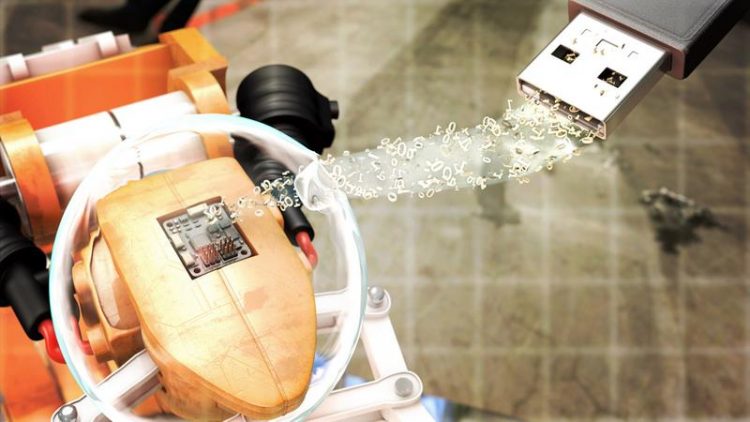
Der PLUGandWORK-Cube des Fraunhofer IOSB integriert existierende Maschinen in moderne Fertigungsanlagen. Damit schaffen auch mittelständische Unternehmen den Sprung ins Industrie-4.0-Zeitalter. Fraunhofer IOSB
Industrie 4.0 ist für Unternehmen zu einer Art Wettlauf um die Zukunft geworden. Die Vision ist bestechend. Alle Maschinen sind untereinander vernetzt und kommunizieren miteinander. Fertigungsstraßen konfigurieren sich selbst und reagieren intelligent auf Störungen oder Änderungswünsche. So haben die Mitarbeiter jederzeit den vollen Überblick über die Produktion und den Status der einzelnen Anlagen. Neue Maschinen werden nach dem Plug-and-Work-Prinzip integriert.
Heute scheitert die konsequente Umsetzung von Industrie 4.0 noch oftmals, weil auch ältere Geräte im Einsatz sind, die noch nicht über die nötigen Schnittstellen verfügen. Im schlimmsten Fall arbeiten die Maschinen dann in der Fertigungshalle isoliert vor sich hin.
Eine Lösung für dieses Problem hat das Fraunhofer-Institut für Optronik, Systemtechnik und Bildauswertung IOSB in Karlsruhe entwickelt. Der PLUGandWORKTM-Cube sorgt dafür, dass bestehende Maschinen und Anlagen in das Produktionssystem eingebunden werden können. In dem unscheinbaren Kästchen steckt ein Standard-Industrie-PC mit Windows als Betriebssystem.
Die Maschine liefert alle Informationen über sich selbst und ihre Fähigkeiten per Netzwerkkabel an den Würfel. Im ersten Schritt erstellt ein Mitarbeiter die Selbstbeschreibung der Maschine auf Basis des XML-Datenformats AutomationML (Automation Markup Language).
Ein Assistenz-Werkzeug erleichtert mit einer intuitiv bedienbaren, graphischen Bedienoberfläche den Aufbau der Selbstbeschreibung. Mit Hilfe dieses Modells generiert der Cube im zweiten Schritt automatisch den Kommunikations-Server zum Austausch von Informationen mit anderen Maschinen und der übergeordneten Fertigungssteuerung.
So wird die Maschine im Fertigungssystem integriert, sie kann mit anderen Anlagen kommunizieren und ist über das Netzwerk ansprechbar. »Im Prinzip ist das ganz ähnlich wie die Installation eines USB-Geräts, beispielsweise eines Druckers, am Büro-PC«, erklärt Projektleiter Dr. Olaf Sauer.
Die Tools registrieren aber auch Änderungen an der Maschine, beispielsweise bei einer aktualisierten Konfiguration. Ein Änderungsmanager nimmt die neue Konfiguration auf und leitet sie an den Kommunikations-Server weiter.
Mit dem Fraunhofer-Cube entfällt das umständliche Konfigurieren und Einrichten, wenn eine Anlage manuell in die Fertigung integriert wird. Dieser Prozess kann sich unter Umständen über mehrere Tage oder sogar Wochen hinziehen, der PLUGandWORKTM-Cube ist oft schon nach einigen Stunden fertig.
Größtmögliche Transparenz, Kompatibilität und Datensicherheit
Doch die Nachrüstbox erlöst nicht nur einzelne Maschinen aus ihrer Isolation. Sie bietet einen weiteren, entscheidenden Vorteil: »Auf dem PLUGandWORKTM-Cube können auch Daten der angeschlossenen Maschinen gespeichert werden«, erklärt Sauer. »Die Mitarbeiter in der Betriebsleitung sehen jederzeit, was an der Maschine gerade los ist und erkennen sofort, wenn Probleme auftauchen. So herrscht Transparenz beim Geschehen in der Fertigungshalle.«
Der Server im Cube arbeitet mit dem Kommunikationsprotokoll OPC UA (Open Platform Communications Unified Architecture) und nutzt damit einen international akzeptierten Standard, der bei der Maschine-zu-Maschine-Kommunikation die größtmögliche Kompatibilität gewährleistet. Auch an die Datensicherheit ist gedacht: Alle Daten werden verschlüsselt übertragen, und nur autorisierte Anlagen können sich in das System einklinken. Zur Sicherheitstechnik steuern dabei Industriepartner wie die Wibu Systems AG aus Karlsruhe ihre Expertise bei.
Je nach Komplexität der Maschinendaten und -parameter lassen sich bis zu 20 Maschinen an einen Cube anschließen. Die Nachrüsttechnik ist keineswegs nur für die großen Hersteller, etwa aus der Automobilbranche, konzipiert. »Auch mittelständische Unternehmen mit nur 20 Maschinen können diese in die Produktionssteuerung einbinden«, sagt Fraunhofer-Experte Sauer. Systemintegratoren, die bei ihren Kunden komplette Anlagen aufbauen und schlüsselfertig übergeben, profitieren ebenfalls vom Cube.
Schon seit Jahren arbeitet das IOSB an digitalen Technologien, die Unternehmen fit für Industrie 4.0 machen. Die Experten entwickeln die dafür nötigen standardisierten Schnittstellen, Softwaremodule und Datenübertragungsprotokolle. Außerdem beteiligen sich die Fraunhofer-Experten gemeinsam mit nationalen und internationalen Partnern aktiv an der Weiterentwicklung von AutomationML und engagieren sich in diversen Standardisierungsgremien.
Bis die Vision der Industrie 4.0 vollständig umgesetzt ist und die Hersteller ihren kompletten Maschinenpark auf den neuesten Stand gebracht haben, werden sicherlich noch einige Jahre vergehen. Bis dahin sorgt der PLUGandWORKTM-Cube dafür, dass auch ältere Maschinen fit für die digitale Ära sind.
https://www.fraunhofer.de/de/presse/presseinformationen/2017/maerz/digitale-nach…
Media Contact
Alle Nachrichten aus der Kategorie: HANNOVER MESSE
Neueste Beiträge
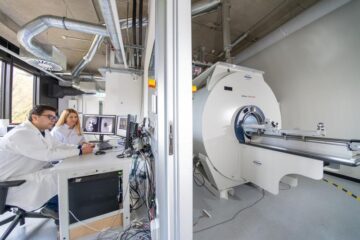
Diamantstaub leuchtet hell in Magnetresonanztomographie
Mögliche Alternative zum weit verbreiteten Kontrastmittel Gadolinium. Eine unerwartete Entdeckung machte eine Wissenschaftlerin des Max-Planck-Instituts für Intelligente Systeme in Stuttgart: Nanometerkleine Diamantpartikel, die eigentlich für einen ganz anderen Zweck bestimmt…
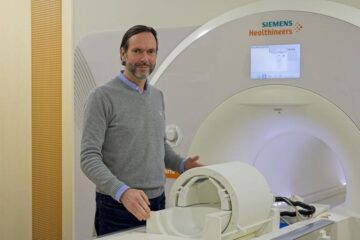
Neue Spule für 7-Tesla MRT | Kopf und Hals gleichzeitig darstellen
Die Magnetresonanztomographie (MRT) ermöglicht detaillierte Einblicke in den Körper. Vor allem die Ultrahochfeld-Bildgebung mit Magnetfeldstärken von 7 Tesla und höher macht feinste anatomische Strukturen und funktionelle Prozesse sichtbar. Doch alleine…
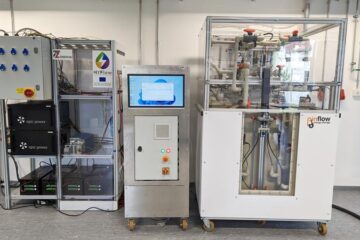
Hybrid-Energiespeichersystem für moderne Energienetze
Projekt HyFlow: Leistungsfähiges, nachhaltiges und kostengünstiges Hybrid-Energiespeichersystem für moderne Energienetze. In drei Jahren Forschungsarbeit hat das Konsortium des EU-Projekts HyFlow ein extrem leistungsfähiges, nachhaltiges und kostengünstiges Hybrid-Energiespeichersystem entwickelt, das einen…