Plasmagefäß für Wendelstein 7-X fertig gestellt

Teilstück der Plasmakammer von Wendelstein 7-X: Zwanzig dieser Elemente werden zu einem Ring zusammengefügt. In seiner Form schmiegt er sich den verwundenen Konturen des Plasmas an. Die Öffnungen im Gefäß machen das Plasma für Heizung und Messgeräte zugänglich. IPP, W. Filser
Der erste große Fertigungsauftrag für das Fusionsexperiment Wendelstein 7-X, die Herstellung der Plasmakammer, ist erfolgreich abgeschlossen: Die 20 Sektoren des bizarr geformten, 35 Tonnen schweren Gefäßes wurden aus mehreren hundert Einzelteilen zusammengefügt – ein handwerkliches Meisterstück. Die Montage der komplexen Gesamtanlage, die im Frühjahr 2005 im Teilinstitut Greifswald des Max-Planck-Instituts für Plasmaphysik (IPP) begonnen hat, wird rund sechs Jahre dauern.
Ziel der Fusionsforschung ist es, ähnlich wie die Sonne aus der Verschmelzung von Atomkernen Energie zu gewinnen. Um das Fusionsfeuer zu zünden, muss in einem späteren Kraftwerk der Brennstoff, ein Wasserstoffplasma, in Magnetfeldern eingeschlossen und auf Temperaturen über 100 Millionen Grad aufgeheizt werden. Wendelstein 7-X, die nach der Fertigstellung weltweit größte Fusionsanlage vom Typ Stellarator, hat die Aufgabe, die Kraftwerkseignung dieses Bautyps zu untersuchen.
Gefertigt wurde das Plasmagefäß von der MAN DWE GmbH in Deggendorf in 20 Teilstücken, von denen vier im IPP bereits für die Montage des Experiments genutzt werden. Zu einem annähernd ringförmigen Gefäß von rund zwölf Metern Durchmesser zusammengesetzt, wird die Plasmakammer später das bis zu 100 Millionen Grad heiße Plasma einschließen. In seiner Form ist das Gefäß dem verwundenen Plasmaschlauch angepasst. Diese eigenwillige Gestalt zusammen mit der verlangten hohen Maßhaltigkeit machte die Herstellung zu einer anspruchsvollen Aufgabe: Stellenweise sind die Toleranzen nicht größer als drei Millimeter.
Um die bizarre Form in Stahl nachzubilden, wurde das 35 Tonnen schwere Gefäß aus 200 einzelnen Ringen aufgebaut. Jeder Ring wiederum besteht aus mehreren fingerdicken und 18 Zentimeter breiten Stahlblechstreifen, die vielfach geknickt die geschwungenen Konturen nachformen. Mehr als 1600 Meter Schweißnaht fügen die über achthundert Einzelteile des Gefäßes vakuumdicht zusammen. Dazu wurden die zu verbindenden Bauteile in genau definierter Position in zwei Millimeter Abstand voneinander fixiert und der Spalt durch mehrere neben- und übereinander per Hand angeschweißte Lagen von Draht geschlossen – insgesamt wurden dabei einige Kilometer Schweißdraht verbraucht.
299 Öffnungen, durch die später das Plasma beobachtet und geheizt sowie wärmebelastete Wandpartien gekühlt werden sollen, wurden anschließend mit scharfem Wasserstrahl in die Gefäßteile geschnitten. Jeder der 20 Sektoren wurde auf der Innenseite mit Halterungen für die spätere Wandverkleidung versehen und außen mit Kühl- und Heizrohren. Es folgten Tests sämtlicher Gefäßsegmente und Rohre auf Ultrahochvakuumdichtigkeit. Dreidimensionale Vermessungen mit dem Lasertracker begleiteten die Fertigung von Anfang an und stellten sicher, dass die vorgegebene Form auch exakt erreicht worden war: „Die asymmetrische Gestalt gepaart mit der verlangten hohen Genauigkeit machte all dies“, so fasst der für das Plasmagefäß verantwortliche IPP-Ingenieur Bernd Hein zusammen, „zu einem Behälterbau am Rand des technisch Möglichen, der höchste Anforderungen an das handwerkliche Können der Beteiligten stellte“.
Im fertigen Experiment wird das Plasmagefäß im Inneren eines Kranzes aus 70 supraleitenden Magnetspulen liegen. Sie erzeugen den magnetischen Käfig, der das Plasma vor den Innenwänden des Plasmagefäßes in Schwebe hält. Der Spulenkranz wiederum ist umgeben von einer wärmeisolierenden Außenhülle. Eine Superisolation umschließt den luftleeren Raum zwischen Plasma- und Außengefäß und trennt die mit flüssigem Helium auf Supraleitungstemperatur abgekühlten Magnetspulen von ihrer warmen Umgebung. Die gesamte Anlage ist aus fünf nahezu baugleichen Modulen aufgebaut, die vormontiert und dann in der Experimentierhalle kreisförmig zusammengesetzt werden. Die Montage von Wendelstein 7-X (siehe IPP-Presseinformation 5/05), die bereits im Frühjahr 2005 begonnen hat, wird rund sechs Jahre dauern.
Media Contact
Weitere Informationen:
http://www.ipp.mpg.deAlle Nachrichten aus der Kategorie: Energie und Elektrotechnik
Dieser Fachbereich umfasst die Erzeugung, Übertragung und Umformung von Energie, die Effizienz von Energieerzeugung, Energieumwandlung, Energietransport und letztlich die Energienutzung.
Der innovations-report bietet Ihnen hierzu interessante Berichte und Artikel, unter anderem zu den Teilbereichen: Windenergie, Brennstoffzellen, Sonnenenergie, Erdwärme, Erdöl, Gas, Atomtechnik, Alternative Energie, Energieeinsparung, Fusionstechnologie, Wasserstofftechnik und Supraleittechnik.
Neueste Beiträge
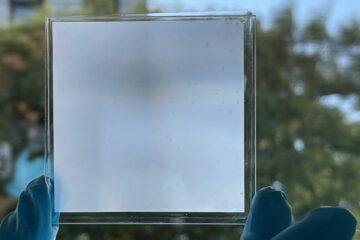
Neuartiges Material für nachhaltiges Bauen
Innovativer Werkstoff für eine energieeffiziente Architektur: Forschende des Karlsruher Instituts für Technologie (KIT) stellen in der aktuellen Ausgabe der Fachzeitschrift Nature Communications ein polymerbasiertes Material mit besonderen Eigenschaften vor. Das…
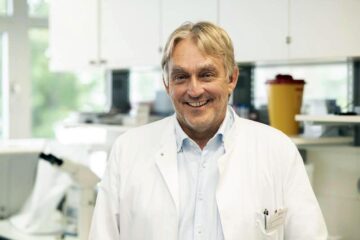
Neues Antibiotikum gegen Erreger der Flussblindheit und Lymphatischen Filariose
Prof. Achim Hoerauf, Direktor des Instituts für Medizinische Mikrobiologie, Immunologie und Parasitologie des Universitätsklinikums Bonn (UKB), und seinem Team ist es in Kollaboration mit der Abteilung Pharmazeutische Technologie und Biopharmazie…
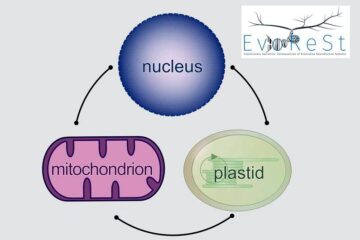
Evolutionäre Genomik: Folgen biodiverser Fortpflanzungssysteme
Die Deutsche Forschungsgemeinschaft (DFG) fördert die Einrichtung eines neuen Graduiertenkollegs (GRK) in der Biologie an der Universität Göttingen. Das GRK mit dem Titel „Evolutionary Genomics: Consequences of Biodiverse Reproductive Systems…