Cleanline – effiziente Reinigung im Fertigungstakt
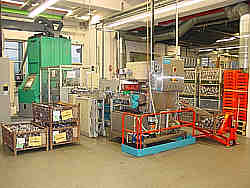
Die Reinigungsanlage Cleanline lässt sich einfach und effizient in den Fertigungsprozess integrieren.
Die Integration der Bauteilereinigung in den Fertigungsprozess kann in vielen Unternehmen einen entscheidenden Beitrag zur Reduzierung der Herstellkosten leisten. Doch die bisher am Markt erhältlichen Kleinreinigungsanlagen sind dazu meist nicht in der Lage. Die Fraunhofer-Technologie-Entwicklungsgruppe TEG in Stuttgart hat deshalb das neuartige, prozessintegrierte Reinigungssystem Cleanline entwickelt. Dieses bietet speziell bei der Fertigung in Linien oder Inseln eine lohnenswerte Alternative.
Die Reinigungsaufgaben bei der Bearbeitung von Serienteilen in der metallverarbeitenden Industrie sind äußerst vielfältig. Verschiedenste Verunreinigungen wie Emulsionen, Öle, Fette und Späne haften nach der Bearbeitung an den Oberflächen der Werkstücke und müssen entfernt werden. Die Höhe des Reinigungsgrades resultiert dabei stets aus den Anforderungen des nachfolgenden Bearbeitungsschritts. So genügt zur anschließenden sicheren Werkstückaufnahme beispielsweise die Entfernung störender Späne und Partikel. Bei der Vorbereitung von Klebeflächen ist dagegen eine gründliche Entfettung und Oberflächensäuberung notwendig. Die unterschiedlichen Reinigungsaufgaben werden dabei in der Regel in zentralen Anlagen durchgeführt. Allerdings gibt es hier einen entscheidenden Nachteil, denn die Werkstücke müssen zuvor meist von Hand in Körben chargiert und zur Anlage gebracht werden. „Dieser Vorgang ist mit einem hohen Personal- und Transportaufwand verbunden“, so Dipl.-Ing. Ulf Nägele, der für die Fraunhofer TEG das Cleanline-System mitentwickelt hat. Zudem sind Materialpuffer erforderlich, die wiederum zu höheren Durchlaufzeiten führen können.
Die Fraunhofer TEG in Stuttgart hat sich deshalb der Herausforderung gestellt, die Vielzahl der Anforderungen an Reinigungssysteme exakt zu analysieren. Zielvorgabe war, eine neuartige Lösung zu erarbeiten, die einem möglichst breiten Anwendungsgebiet Rechnung trägt. „Wir wollten eine Standardanlage konzipieren, die größtmögliche Flexibilität in Bezug auf Reinigungsverfahren und Bauteile bietet“, erklärt Dipl.-Ing. Nägele, „und die gleichzeitig Defizite bestehender Anlagen aufhebt, die nicht prozessorientiert arbeiten.“
Anforderungen an das neue System
Um die genauen Anforderungen an ein derartiges Reinigungssystem festzulegen, befragte das Fraunhofer TEG-Team zunächst 50 Unternehmen der metallverarbeitenden Industrie. Dabei wurden verschiedene Reinigungsaufgaben untersucht, bei denen eine Substitution zentraler Reinigungsanlagen durch herkömmliche Kleinreinigungsanlagen wie Durchlauf- oder Trommelanlagen aus unterschiedlichsten Gründen nicht möglich ist. Basierend auf diesen Daten legten die Stuttgarter Experten folgende Merkmale fest, welche die neue Lösung aufweisen sollte:
– Reinigung von Bauteilvarianten mit geringem Rüstaufwand
– Effiziente Reinigung und Trocknung in kurzem Fertigungstakt
– Flexibilität im Einsatz von unterschiedlichen wässrigen Reinigungsverfahren
– Sicherer Werkstücktransport ohne Beschädigung der Bauteiloberflächen
– Geringer Platzbedarf
„Hinzu kommt, dass insbesondere bei Werkstücken mit schöpfenden Geometrien, Hinterschneidungen und Sacklochbohrungen der Reinigungs- und Trocknungsgrad bestehender Anlagen häufig nicht ausreicht“, erklärt Dipl.-Ing. Pia Rimbrecht, Mitarbeiterin in der Gruppe mechanische Verfahrenstechnik bei der Fraunhofer TEG. Aus diesem Grund nahmen sich die TEG-Ingenieure kritische Werkstückgeometrien zum Maßstab für weiterreichende konzeptionelle Anstrengungen. Zunächst wurden Materialflusskonzepte entwickelt, die eine größtmögliche Flexibilität bezüglich Bauteilvarianten und der einzusetzenden wässrigen Reinigungsverfahren zulassen. „Den aussichtsreichsten Lösungsansatz haben wir schließlich gemeinsam mit der Firma Rotan GmbH in einen ersten Prototyp umgesetzt“, so Rimbrecht (Abb. 1).
Funktion des Systems Cleanline
Der Cleanline-Prototyp wurde von den Stuttgarter Experten als kombinierte Spritz-Tauchreinigungsanlage konzipiert und durch ein Trocknungsmodul ergänzt. Um den Platzbedarf der neuen Anlage zu reduzieren, erfolgt der Materialtransport der Werkstücke innerhalb des Reinigungs- und Trocknungsmoduls vertikal durch Räder. An diesen sind die Werkstückaufnahmen befestigt, die an die jeweilige Werkstückgeometrie angepasst werden können und zur Vermeidung von Spritzschatten möglichst offen gestaltet sind. Die Dimensionierung der Werkstückaufnahmen ist so geregelt, dass alle Bauteilvarianten Platz finden (Abb. 2). „Durch die Drehbewegung des Rades ergaben sich zudem weitere wichtige Faktoren“, erklärt die TEG-Ingenieurin. Denn zum einen liegen die Bauteile während des Vorgangs an unterschiedlichen Flächen der Behausung an, so dass alle Seiten optimal gereinigt und getrocknet werden. Zum anderen ist gewährleistet, dass schöpfende Geometrien durch die Drehbewegung entleert werden. Dadurch wird die Verschleppung von Reinigungsmedien in die nachfolgenden Stufen deutlich reduziert und der Reinigungs- und Trocknungsprozess unterstützt.
„Durch die vertikale Förderung innerhalb der Module konnten wir auch eine Kombination von Spritz- und Tauchreinigung auf engstem Raum kombinieren“, fährt Nägele fort. Dieser Verfahrensablauf ist vor allem für Werkstücke mit komplexer Geometrie vorteilhaft. Zudem ermöglicht die Tauchreinigung eine Anwendung weiterer Verfahrensalternativen wie Ultraschall oder Injektionsfluten zur Unterstützung des Reinigungsprozesses. „Diese Verfahren können durch eine einfache Modifikation des Reinigungsmoduls integriert werden, ohne dass eine Anpassung des Grundaufbaus der Anlage erforderlich ist“, erklärt der Ingenieur. Darüber hinaus gestattet der modulare Aufbau eine Hintereinanderschaltung mehrerer Reinigungseinheiten und damit optional eine mehrstufige Reinigung ohne nennenswerten konstruktiven Änderungsaufwand.
Die Ein- und Ausgabeschnittstellen der Anlage wurden außerdem so gewählt, dass ein möglichst großer Freiheitsgrad bei der An- und Einbindung in bestehende oder geplante Fertigungseinrichtungen besteht (Abb. 3). Die Werkstücke können beispielsweise über ein Förderband oder eine Hebeeinrichtung vereinzelt an der Ein- bzw. Ausgabeposition bereitgestellt werden. Zur Steuerung des Beladevorgangs wird durch die Reinigungsanlage ein Ausgangssignal zur Beladebereitschaft und ein Eingangssignal zur Beladefreigabe gegeben. Der weitere Transport der Werkstücke sowie die Übergabe vom Reinigungs- in das Trocknungsmodul erfolgt durch eine horizontal verlaufende Schiebereinrichtung. Dabei werden lediglich die Werkstücke in das folgende Modul befördert, während die Werkstückaufnahmen im Modul verbleiben. Auf diese Weise kann die Verschleppung von Reinigungsmedien weiter reduziert und die Trocknung unterstützt werden. Die Schieber sind als massive Blöcke ausgeführt, welche die einzelnen Bearbeitungsräume voneinander trennen.
Überzeugende Resultate in der Praxis
Dieses neuartige Reinigungskonzept überzeugte auch die verantwortlichen Leiter der Rotorenfertigung der ebm-Werke in Mulfingen. Das Unternehmen stellt innovative und leistungsstarke Außenläufermotoren sowie Ventilatoren her. Die Reinigung der Rotoren erfolgt dabei zwischen der spanenden Bearbeitung und dem Tamponbedrucken. Und gerade bei der spanabhebenden Bearbeitung stellt die Oberflächenreinheit der Bauteile einen entscheidenden Faktor dar, um den Fertigungsprozess stabil und sicher zu gestalten und damit eine konstante Qualität der Produkte zu gewährleisten. Das Unternehmen beschloss deshalb, das neuartige Reinigungssystem Cleanline in den Fertigungsprozess zu integrieren. Die Anlagenparameter wurden hierfür gemeinsam von den Entwicklern der Fraunhofer TEG, dem Anlagenhersteller Rotan GmbH und natürlich von der Firma ebm erarbeitet. Durch die enge Abstimmung in der Planungs- und Umsetzungsphase konnte der Reinigungsprozess schließlich durchgängig optimiert werden.
Konkret heißt dies, dass die erforderlichen Reinigungs- und Trocknungsanforderungen jetzt mit deutlich reduziertem chemischen und energetischen Aufwand erfüllt werden. So konnte die Reinigerkonzentration von drei auf 1,5 Prozent reduziert und die Reinigungstemperatur von 60°C auf 45°C abgesenkt werden. Durch die definierte Ausrichtung der Teile in den Werkstückaufnahmen und eine gezielte Ausbildung des Flüssigkeitsstrahls der Reinigungsdüsen werden dabei auch die vor allem an der Innenseite der Rotoren stark anhaftenden Feinstpartikel prozesssicher entfernt (Abb. 4). Zusätzlich ermöglicht die Reduzierung von Temperatur und Reinigungsmedium in Kombination mit speziellen Einbauten im Vorlagetank eine Separation demulgierender Öle an der Oberfläche. Partikuläre Verunreinigungen werden dabei durch eine Feinfiltereinrichtung entfernt und Verdunstungen automatisch durch eine Dosiereinheit ausgeglichen. Da die Anlage im dreischichtigen Betrieb eingesetzt wird, erfolgt der Wechsel des Reinigungsmediums während der Stillstandszeiten am Wochenende durch externes Service-Personal. Das Medium wird anschließend einer zentralen Aufbereitung zugeführt. Beim Einsatz mehrerer dezentraler Anlagen ist auch die Versorgung mit Reinigungsmedien aus einer zentralen Versorgungs- und Aufbereitungsstation denkbar, die nicht auf der Fertigungsfläche installiert sein muss.
Kritische Stellen gemeistert
Auch bei der Trocknung konnte eine Absenkung der erforderlichen Temperatur bei einer fertigungsbedingten Taktzeit von fünf Sekunden pro Rotor erreicht werden. Allerdings erwiesen sich hier die Wuchtbohrungen an der Oberseite der glockenförmigen Rotorgebilde als kritisch. Denn die kurzen Taktzeiten sowie die Absenkung der Reinigungstemperatur und die damit verbundene geringere Wärmeaufnahme der Bauteile erschweren eine vollständige Trocknung. Die Entleerung der schöpfenden Geometrien durch die materialflussbedingte Drehbewegung der Teile reicht ebenfalls nicht aus. „Wir haben deshalb spezielle Ringdüsen entwickelt, die mit pulsierender Druckluft arbeiten“, erklärt Ulf Nägele. Damit kann nach Eintritt der Rotoren in die Trocknungskammer der größte Teil der Reinigungsflüssigkeit aus den Wuchtbohrungen entfernt werden. Gleichzeitig kommt ein Heißluftgebläse mit Gegenstromprinzip zum Einsatz, das die Rotoren über Schlitzdüsen an der jeweiligen Taktposition trocknet und die Konvektion über der gesamten Bauteiloberfläche erhöht. „Um die Heizenergie zu reduzieren, wird die Trocknungsluft bei dieser Anlage im Kreislauf gefahren“, fährt Nägele fort. Jedoch werden, um eine Sättigung zu vermeiden, etwa fünf Prozent der Trocknungsluft dem Kreislauf entnommen und über einen Schwadenkondensator abgeführt. Diese Maßnahmen ermöglichten eine Absenkung der erforderlichen Temperatur von 90°C auf 45°C. Zudem ist durch die Reduzierung keine weitere aktive Kühlung der Rotoren außerhalb der Reinigungsanlage vor dem Tamponbedrucken notwendig.
Erschließung weiterer Anwendungsgebiete
Die Integration der von der Fraunhofer TEG entwickelten Reinigungstechnik in den Fertigungsprozess ermöglicht in vielen Anwendungen eine Reduzierung der Fertigungskosten. Durch die Entfernung störender Kontaminationen bereits am Ort der Entstehung kann darüber hinaus die Reinigungsaufgabe auf das Notwendige begrenzt und dadurch die Effizienz des Reinigungsprozesses erhöht werden. „Eine weitere Umsetzung dieses neuartigen Konzepts erfolgt derzeit für Ventilblöcke“, berichtet Dipl.-Ing. Ulf Nägele. Auch hier sind die bereits genannten Kennzeichen der Werkstücke in Bezug auf die kritischen Reinigungsgeometrien, die kurzen Taktzeiten und den Variantenmix ausschlaggebend für die Überzeugungskraft des kompakten Reinigungskonzepts von Cleanline. „Zukünftig sollen aber noch weitere Anwendungsgebiete erschlossen werden“, meint Nägele abschließend. Aufgrund der bisherigen Entwicklungen sehen die Fraunhofer TEG-Experten beispielsweise Möglichkeiten bei der Integration verschiedener Reinigungsverfahren in das materialflusstechnische Konzept oder auch in der modularen Erweiterung bei der Umsetzung eines mehrstufigen Reinigungsprozesses.
Zur Person:
Dipl.-Ing. Ulf Nägele studierte Maschinenbau mit Schwerpunkt mechanische Verfahrenstechnik an der Universität in Stuttgart. Bis Mitte des Jahres 2001 war er wissenschaftlicher Mitarbeiter bei der Fraunhofer-Technologie-Entwicklungsgruppe als Leiter der Gruppe mechanische Verfahrenstechnik. Inzwischen ist er für den Vertrieb von Cleanline im Auftrag der Firma Rotan GmbH in Dannstadt verantwortlich.
Tel. 07144/898095 2
Fax 07144/898095 7
E-Mail: ulf.naegele@t-online.de
Zur Person:
Dipl.-Ing. (FH) Pia Rimbrecht studierte Verfahrens- und Umwelttechnik an der Fachhochschule in Offenburg. Seit März 2001 ist sie als wissenschaftliche Mitarbeiterin bei der Fraunhofer TEG in Stuttgart speziell im Bereich der industriellen
Teilereinigung tätig.
Tel. 0711/970-3539
Fax 0711/970-3998
E-Mail: pia.rimbrecht@teg.fraunhofer.de
Media Contact
Weitere Informationen:
http://www.teg.fraunhofer.de/Alle Nachrichten aus der Kategorie: Verfahrenstechnologie
Dieses Fachgebiet umfasst wissenschaftliche Verfahren zur Änderung von Stoffeigenschaften (Zerkleinern, Kühlen, etc.), Stoffzusammensetzungen (Filtration, Destillation, etc.) und Stoffarten (Oxidation, Hydrierung, etc.).
Unter anderem finden Sie Wissenswertes aus den Teilbereichen: Trenntechnologie, Lasertechnologie, Messtechnik, Robotertechnik, Prüftechnik, Beschichtungsverfahren und Analyseverfahren.
Neueste Beiträge
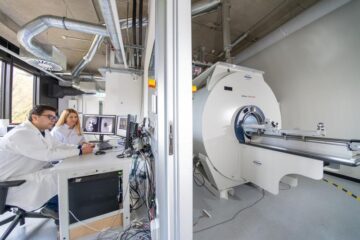
Diamantstaub leuchtet hell in Magnetresonanztomographie
Mögliche Alternative zum weit verbreiteten Kontrastmittel Gadolinium. Eine unerwartete Entdeckung machte eine Wissenschaftlerin des Max-Planck-Instituts für Intelligente Systeme in Stuttgart: Nanometerkleine Diamantpartikel, die eigentlich für einen ganz anderen Zweck bestimmt…
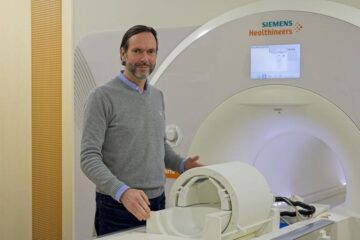
Neue Spule für 7-Tesla MRT | Kopf und Hals gleichzeitig darstellen
Die Magnetresonanztomographie (MRT) ermöglicht detaillierte Einblicke in den Körper. Vor allem die Ultrahochfeld-Bildgebung mit Magnetfeldstärken von 7 Tesla und höher macht feinste anatomische Strukturen und funktionelle Prozesse sichtbar. Doch alleine…
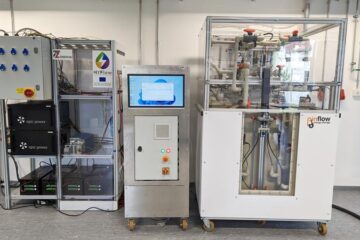
Hybrid-Energiespeichersystem für moderne Energienetze
Projekt HyFlow: Leistungsfähiges, nachhaltiges und kostengünstiges Hybrid-Energiespeichersystem für moderne Energienetze. In drei Jahren Forschungsarbeit hat das Konsortium des EU-Projekts HyFlow ein extrem leistungsfähiges, nachhaltiges und kostengünstiges Hybrid-Energiespeichersystem entwickelt, das einen…