Produktion von RFID-Inlays: Der Prozess muss sitzen
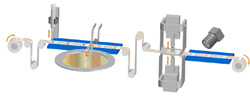
Exemplarische Darstellung eines typischen Fertigungsprozesses für RFID-Inlays: Im ersten Schritt erfolgt der Klebstoff-Auftrag, dann wird der Chip gesetzt. In der folgenden Thermodenstation wird die Kontaktierung sichergestellt.
RFID – das Schlagwort und die Hoffnung vieler Anwender, insbesondere im Supply Chain Management und in Logistikprozessen, hat sich in 2006 eine kleine Pause in seiner Entwicklung gegönnt. Die Gründe hierfür waren technologischer, aber auch systematischer Natur.
Im Wesentlichen wurden in 2006 technologische Herausforderungen (z.B. im Bereich UHF) geklärt und durch eine allgemeine und weltweite Ausweitung von RFID-Anwendungen konnte der Wertbeitrag, den RFID für Produktion, Logistik und Anti-Counterfeiting bedeutet, einem breiten Anwenderspektrum verdeutlicht werden. Durch das horizontale Ausweiten auf eine weitere Nutzerbasis und durch das erlangte Wissen zur Umsetzung von RFID sind die Vorzeichen für eine nachhaltige Entwicklung in 2007 gegeben.
DELO Industrie Klebstoffe trägt in der Wertschöpfungskette wesentlich dazu bei, den Anforderungen hinsichtlich Produktivität in der Fertigung von RFID-Inlays sowie der Produktqualität der Inlays in der Anwendung gerecht zu werden. Die von DELO erforschten und entwickelten Klebstoffe zur Kontaktierung des Chips auf dem Antennensubstrat spielen dabei eine Schlüsselrolle zur Funktionsfähigkeit von HF- oder UHF-Inlays.
Zur Verdeutlichung der Aufgabenstellung an den Klebstoff ist nachfolgend exemplarisch ein Reel-to-Reel-Fertigungsprozess von RFID-Inlays dargestellt.
Die in Vorprozessen produzierte Antenne wird von der Rolle dem Fertigungsautomaten zugeführt. Die Antennen werden zumeist aus PET-Basislaminaten mit entweder Kupfer- oder Aluminium-Metallisierung zur Verfügung gestellt. Weiterhin finden mit Silbertinten bedruckte Antennen ihren Einsatz. Substratvarianten bieten üblicherweise papier- oder polyimidbasierte Antennen.
Fertigung im Sekundentakt
Bei der Fertigung von Inlays wird in einem ersten Schritt der Klebstoff auf die Kontaktierungsfläche der Antenne, auf die der Chip später gesetzt werden soll, aufgetragen. Dies erfolgt entweder über Nadeldispensen oder über Siebdruckverfahren bei parallel auf dem Substrat angeordneten Antennen, also bei größeren Webbreiten. Danach wird der Chip im Flip-Chip- Verfahren vom Wafer in den Klebstoff auf der Antenne gesetzt. Flip-Chip deshalb, weil die aktive Seite des Chips mit den Bumps (Kontaktierungsstellen) aus der Chipfertigung offen nach oben liegts, in der Anwendung allerdings nur durch Zuwendung zur Antenne eine Funktionalität geschaffen wird, so dass der Chip gedreht werden muss.
Nach dem Platzieren des Chips folgt eine Pufferstation, um den Klebstoff anschließend in einer Thermodenstation auszuhärten. Dabei wird die Temperatur über jeweils einen oberen und unteren heißen Stempel (Thermode) in das System eingebracht. Die Thermoden übernehmen neben dem Wärmeeintrag die Funktion, den Chip mit einer definierten Kraft auf die Antenne zu pressen und die elektrische Kontaktierung sicherzustellen. Nachfolgend ist ein Inspektionsschritt (Funktionalitätsprüfung) angeschlossen, um mögliche Fehlteile zu detektieren und für Folgeprozesse (z. B. Konvertierung zu einem Etikett) erkennbar zu machen.
Der Klebstoff, entweder als nicht leitender Die-Attach-Klebstoff oder anisotrop leitend (in eine Raumrichtung leitend), übernimmt grundsätzlich die Aufgabe, den Mikrochip zuverlässig und an definierter Position auf der Antenne zu fixieren. Neben den rein mechanischen Aufgaben wird durch den Klebstoff zusätzlich die elektrische Kontaktierung gewährleistet.
Bei Chips mit Stud- oder Pd-Bumps erfolgt die elektrische Kontaktierung nur indirekt durch den Klebstoff. Diese Bumpvarianten zeichnen sich durch eine sehr scharfkantige Geometrie und inhomogene Oberflächen aus, sodass beim Setzen des Chips auf dem Antennensubstrat die Bumps direkt in die Metallisierungsschicht eindringen und der elektrische Kontakt geschlossen ist. Der Klebstoff, in Form des nicht leitenden Produkts (NCP = Non Conductive Paste), sichert in diesem Fall ausschließlich die Positionsgenauigkeit des Chips in alle drei Raumrichtungen. Bereits ein minimales Abheben des Chips vom Substrat öffnet den Kontakt und würde zu einem Funktionsausfall des Inlays führen.
Die zweite Variante Klebstoff, so genannter ACP (Anistropic Conductive Paste), stellt neben der mechanischen Fixierung und Positionierung die elektrische Kontaktierung unmittelbar sicher. Dies erfolgt durch eine mit speziellen Partikeln gefüllte polymere Harzmatrix. Anwendung finden ACP zumeist bei geometrisch sehr homogenen und flach aufgebauten Au- oder NiAu-Bumps am Chip, die nicht in die Metallisierungsschicht der Antenne penetrieren können. Natürlich müssen diese Klebstoffe hinsichtlich ihrer Performance dieselben Anforderungen erfüllen wie die NCP und dürfen eine Relativbewegung des Chips zur Antenne in keine Raumrichtung zulassen.
Kostenoptimierung durch neue Klebstoffe
Mittlerweile stehen bei der Firma DELO drei Generationen an Klebstoffen zur Verfügung, die einerseits höchsten Zuverlässigkeitsansprüchen gerecht werden und gleichzeitig schnellste Aushärtegeschwindigkeit bei geringen Temperaturen erreichen. So können die Klebstoffe auf gängigen Fertigungsanlagen bei 140 °C Thermodentemperatur in 5 s ausgehärtet werden. Gängige Temperaturbereiche gingen bislang bis 210 °C, Zykluszeiten im Bereich 10 s waren die Regel. Durch die stark beschleunigten Klebstoffsysteme von DELO könnten einerseits die Produktivität gängiger Anlagen auf ca. 25.000 Teile pro Stunde gesteigert werden, andererseits können durch die geringeren Aushärtetemperaturen kostengünstigere, da weniger hitzestabilisierte Substrate eingesetzt werden.
Beides spart Kosten im Herstellungsprozess des Inlays, wodurch DELO einen aktiven Beitrag zur Kostenoptimierung in dieser preissensitiven Branche leistet. Natürlich werden die Klebstoffklassen durch unterschiedlichste Varianten an Partikeln und Partikelabmischungen ergänzt, sodass für annähernd jede Kombination aus Antenne, Chip, Prozessanforderungen und Zuverlässigkeitsanforderung ein optimales Paket geschnürt werden kann.
Media Contact
Weitere Informationen:
http://www.delo.deAlle Nachrichten aus der Kategorie: Materialwissenschaften
Die Materialwissenschaft bezeichnet eine Wissenschaft, die sich mit der Erforschung – d. h. der Entwicklung, der Herstellung und Verarbeitung – von Materialien und Werkstoffen beschäftigt. Biologische oder medizinische Facetten gewinnen in der modernen Ausrichtung zunehmend an Gewicht.
Der innovations report bietet Ihnen hierzu interessante Artikel über die Materialentwicklung und deren Anwendungen, sowie über die Struktur und Eigenschaften neuer Werkstoffe.
Neueste Beiträge

Neues Wirkprinzip gegen Tuberkulose
Gemeinsam ist es Forschenden der Heinrich-Heine-Universität Düsseldorf (HHU) und der Universität Duisburg-Essen (UDE) gelungen, eine Gruppe von Molekülen zu identifizieren und zu synthetisieren, die auf neue Art und Weise gegen…

Gefahr durch Weltraumschrott
Neue Ausgabe von „Physikkonkret“ beleuchtet Herausforderungen und Lösungen für eine nachhaltige Nutzung des Weltraums. Die Deutsche Physikalische Gesellschaft (DPG) veröffentlicht eine neue Ausgabe ihrer Publikationsreihe „Physikkonkret“ mit dem Titel „Weltraumschrott:…

Wasserstoff: Versuchsanlage macht Elektrolyseur und Wärmepumpe gemeinsam effizient
Die nachhaltige Energiewirtschaft wartet auf den grünen Wasserstoff. Neben Importen braucht es auch effiziente, also kostengünstige heimische Elektrolyseure, die aus grünem Strom Wasserstoff erzeugen und die Nebenprodukte Sauerstoff und Wärme…