Automatisierte Drehmaschine für Rundbarren aus Aluminium
Die Vorteile: Der Werkstückdurchlauf unterliegt keinen platzbedingten Restriktionen, weil im unteren Maschinenbereich viel Raum für die erforderlichen Manipulatoren zur Verfügung steht. Die Werkstückübergabe kann auf sehr kurzen Wegen und mit großer Sicherheit erfolgen.
Drehmaschine mit durchdachter Späneentsorgungseinrichtung
Die Späne fallen frei nach unten auf einen kontinuierlich arbeitenden Späneförderer. Durch dieses Konzept wird verhindert, dass sich Späne auf den Führungsbahnen oder an der Werkzeugaufnahme sammeln und zu Störungen im Betrieb führen, wird erläutert. Manuelle Reinigungsarbeiten werden auf ein Minimum reduziert.
Alle Prozesse wie das Werkstückhandling laufen automatisch ab, so dass ein mannloser Betrieb auch über einen längeren Zeitraum gewährleistet ist. Die ankommenden Rohbarren werden vereinzelt und auf einen Zuführrollengang übergeben. Vor dem Öffnen der Arbeitsraum-Schutztüren wird der Rohbarren außerhalb der Maschine automatisch ausgerichtet und zentriert.
Werkstückübergabe aus der Drehmaschine in einer Bewegung
Die Werkstückübergabe erfolgt in einer Bewegung. Dabei wird der fertig gedrehte Barren aus der Maschine auf den Abführrollengang an der Maschinenrückseite abgelegt und gleichzeitig der zentrierte Rohbarren durch die Maschinenvorderseite in den Arbeitsbereich gebracht und gespannt.
Die Spannung der Rundbarren erfolgt durch zwei Stirnmitnehmer, so kann die Mantelfläche komplett in einem Arbeitsgang gedreht werden. Die Bearbeitung erfolgt durch zwei hintereinander angeordnete und in der Höhe gestaffelte Werkzeuge, die auf einem gemeinsamen Vorschubschlitten montiert sind. Das vordere Werkzeug übernimmt die Schruppbearbeitung, während das hintere Werkzeug im selben Arbeitsgang schlichtet.
Drehmaschine bearbeitet Barren mit Durchmessern von 125 bis 710 mm
Der Arbeitsbereich dieser Maschine umfasst Barren mit einem Durchmesser von 125 bis 710 mm, wobei der tatsächliche Arbeitsbereich von den jeweils montierten Stirnmitnehmern festgelegt wird. Um den angegebenen Durchmesserbereich abzudecken, gibt es drei verschiedene Stirnmitnehmerpaare, die in kurzer Zeit getauscht werden können. Die standardmäßige Werkstücklänge liegt in einem Bereich von 600 bis 1700 mm.
Um die Taktzeiten auf ein Minimum zu reduzieren, hat der Hauptantrieb je nach Maschinengröße eine Antriebsleistung zwischen 130 und 220 kW. Diese hohe Leistung ist erforderlich, um den Beschleunigungs- und Bremsvorgang des Werkstückes zu minimieren, weil er ein Teil der Taktzeit ist.
Media Contact
Alle Nachrichten aus der Kategorie: Maschinenbau
Der Maschinenbau ist einer der führenden Industriezweige Deutschlands. Im Maschinenbau haben sich inzwischen eigenständige Studiengänge wie Produktion und Logistik, Verfahrenstechnik, Fahrzeugtechnik, Fertigungstechnik, Luft- und Raumfahrttechnik und andere etabliert.
Der innovations-report bietet Ihnen interessante Berichte und Artikel, unter anderem zu den Teilbereichen: Automatisierungstechnik, Bewegungstechnik, Antriebstechnik, Energietechnik, Fördertechnik, Kunststofftechnik, Leichtbau, Lagertechnik, Messtechnik, Werkzeugmaschinen, Regelungs- und Steuertechnik.
Neueste Beiträge
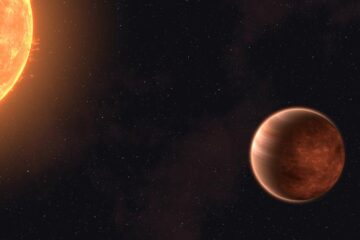
Wolken bedecken die Nachtseite des heißen Exoplaneten WASP-43b
Ein Forschungsteam, darunter Forschende des MPIA, hat mit Hilfe des Weltraumteleskops James Webb eine Temperaturkarte des heißen Gasriesen-Exoplaneten WASP-43b erstellt. Der nahe gelegene Mutterstern beleuchtet ständig eine Hälfte des Planeten…
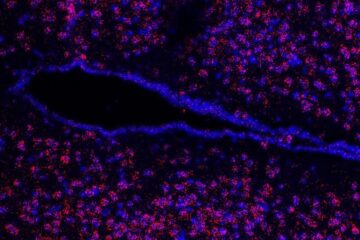
Neuer Regulator des Essverhaltens identifiziert
Möglicher Ansatz zur Behandlung von Übergewicht… Die rapide ansteigende Zahl von Personen mit Übergewicht oder Adipositas stellt weltweit ein gravierendes medizinisches Problem dar. Neben dem sich verändernden Lebensstil der Menschen…
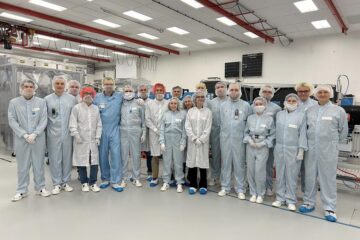
Maschinelles Lernen optimiert Experimente mit dem Hochleistungslaser
Ein Team von internationalen Wissenschaftlerinnen und Wissenschaftlern des Lawrence Livermore National Laboratory (LLNL), des Fraunhofer-Instituts für Lasertechnik ILT und der Extreme Light Infrastructure (ELI) hat gemeinsam ein Experiment zur Optimierung…