Servoantriebe verbessern Ausbringungsleistung und Präzision
Die Flexible-Servo-Drive-Technologie kombiniert einen Servoantrieb mit einem schaltbaren Getriebe und bietet damit sowohl mehr Klasse als auch Masse. Die Stanz- und Umformautomaten des Pforzheimer Pressenherstellers Haulick + Roos sind grundsätzlich für die Herstellung von Stanz- und Umformteilen mit höchster Präzision konzipiert. Mit dem neuen Servoantrieb lässt sich die Fertigungspräzision entweder mit einer deutlich höheren Ausbringung kombinieren oder bei gleicher Ausbringungsleistung verglichen mit einer konventionellen Exzenterpresse die Präzision der hergestellten Teile noch weiter steigern.
Definierte Geschwindigkeitsverläufe dank Servoantrieb schonen Maschine und Werkzeug
Reduktion der Stößelgeschwindigkeit – so lautet die Zauberformel, die in der Stanz- und Umformtechnik die Fachleute begeistert. Grund dafür sind die geringen Stößelgeschwindigkeiten und definierte Geschwindigkeitsverläufe beim Umformen, Tiefziehen, Biegen oder Prägen. Damit wird die Qualität der Produkte wesentlich verbessert, sowie Werkzeug und Maschine werden geschont.
Nur beeinträchtigen sie leider auch die Produktivität, denn eine langsam zu Werke gehende Maschine kann naturgemäß keine beeindruckenden Taktraten und damit keine hohe Ausbringung bieten. Die Verknüpfung von hoher Produktivität und hervorragender Qualität schien trotz vieler Anläufe nicht so recht gelingen zu wollen – bis die Ingenieure von Haulick + Roos einen Weg aus diesen Widersprüchen gefunden und die Flexible-Servo-Drive-Technologie (FSD) entwickelt und vor etwa zwei Jahren eingeführt haben. Diese innovative Antriebstechnologie für Stanz- und Umformautomaten verbindet auf ungeahnt flexible Weise, was zuvor getrennt war.
Sinusförmiger Stößelverlauf hat Nachteile
Beim herkömmlichen Antrieb führt der Stößel einer Exzenterpresse stets eine sinusförmige Bewegung aus, denn im oberen Totpunkt (OT) wie auch im unteren Totpunkt (UT) beträgt die Stößelgeschwindigkeit null, um bei 90 beziehungsweise 270° ihr Maximum zu erreichen und dann wieder auf null zu fallen.
Für viele Anwendungen wäre ein anderer, nicht sinusförmiger Geschwindigkeitsverlauf aber von Vorteil, zum Beispiel dann, wenn Umformvorgänge relativ langsam ablaufen sollen, um ein Reißen des Materials zu vermeiden, oder wenn zum Beispiel beim Prägen für einen bestimmten Zeitraum eine konstante, bewegungsfreie Kraft erforderlich ist, um dem Material die notwendige Zeit für Fließvorgänge zu lassen. Reduzierte Umformgeschwindigkeiten erhöhen zudem nicht nur die Genauigkeit der Bearbeitung, sondern verlängern auch die Werkzeugstandzeit und stellen damit eine prozessoptimierte Produktion sicher.
Herkömmliche Antriebe wurden durch Servomotoren ersetzt
Bei seiner FSD-Technologie hat das Pforzheimer Unternehmen den herkömmlichen elektromotorischen Antrieb seiner Stanz- und Umformautomaten durch einen Servomotor ersetzt, dessen Geschwindigkeit in weiten Grenzen eingestellt werden kann. Dieser Flexible Servo Drive (FSD) genannte Antrieb bietet nun die Möglichkeit, die Stößelgeschwindigkeit unabhängig von der jeweiligen Stößelposition einzustellen, indem die Drehzahl des Motors innerhalb von Sekundenbruchteilen angepasst wird.
Bei einem typischen Einsatz beginnt der Servomotor unmittelbar nach dem Umformvorgang, also etwa ab 180°, zu beschleunigen und erreicht bis etwa zum oberen Totpunkt Geschwindigkeiten, die meist ein Mehrfaches über der Hubzahl bei der Umformung liegen. Um den oberen Totpunkt herum beginnt die Abbremsphase, so dass der Stößel mit Beginn der Umformphase wieder mit einer langsameren Geschwindigkeit auf das Material auftrifft.
Ständiger Wechsel in der Motordrehzahl erhöht mittlere Hubzahl
Mit diesem ständigen Wechsel zwischen niedrigen und hohen Motordrehzahlen erreicht der Pressenhersteller unter dem Strich eine deutliche Steigerung der mittleren Hubzahl, ohne dass damit die Geschwindigkeit während der Umformphase erhöht würde.
Die FSD-Technik bietet aber zudem noch eine Besonderheit, die ihr einen entscheidenden Vorsprung vor vergleichbaren Servoantrieben verschafft. Bedingt durch die hohe Getriebe-übersetzung sind den servomotorisch angetriebenen Stanz- und Umformautomaten im Allgemeinen enge Grenzen bei der maximal möglichen Drehzahl und damit bei der maximalen Ausbringung gesetzt.
Um diese Grenze zu überwinden und ihre Automaten auch für solche Aufgaben einsetzen zu können, bei denen hohe Stückzahlen gefragt sind, haben die Pforzheimer seit 2007 als einziger Anbieter am Markt ihren Servoantrieb mit einem schaltbaren Getriebe kombiniert. Mit dieser Motor-Getriebe-Kombination kann nun entschieden werden, ob die Presse mit hohem Arbeitsvermögen laufen soll oder ob höchste Ausbringungen angestrebt werden – ein perfektes Beispiel für ein Höchstmaß an Flexibilität in der Produktion.
FSD sorgt für eine höhere Produktivität trotz unveränderter Geschwindigkeit
Wegen des frei einstellbaren Stößelgeschwindigkeitsverlaufs bietet die FSD-Technologie also eine höhere Produktivität bei unveränderter Geschwindigkeit im Umformbereich. Da der Verlauf der Stößelgeschwindigkeit während der Umformung genau an Material und Werkstück angepasst werden kann, lässt sich auch eine höhere Teilequalität erzielen – wobei durch die reduzierte Auftreffgeschwindigkeit auch noch die Geräuschemissionen sinken und die Werkzeugstandzeit erhöht werden können, was sich langfristig in den Wartungskosten für die Werkzeuge positiv niederschlägt.
Das FSD-System, das an allen Pressen von Haulick + Roos mit Planetengetriebe nachgerüstet werden kann, kommt ohne Schaltvorgänge im laufenden Betrieb aus, so dass weder Kupplungs- noch Bremsenverschleiß auftreten und die Wartungskosten für den Automaten ebenfalls gering bleiben. Dennoch bietet es durch die leichte Anpassung der maschinenseitigen Prozessparameter ein Höchstmaß an Flexibilität und eröffnet damit ganz neue Optimierungsmöglichkeiten für nahezu alle Arten von Umformprozessen.
Umform-Parameter lassen sich dank Servoantrieb schnell anpassen
Die schnelle Anpassung der verschiedenen Parameter wie UT- oder OT-Geschwindigkeit oder der Winkelbereiche zur Umformung gestalten die tägliche Nutzung eines Automaten mit Servoantrieb sehr einfach, was sich in den Rüstzeiten bemerkbar macht.
Da die volle Presskraft auch bei extrem niedrigen Geschwindigkeiten zur Verfügung steht, wird zudem auch das Testen und Einrichten von Werkzeugen vereinfacht – mit Vorteilen wie deutlich verkürzten Rüstzeiten und reduzierten Produktionsunterbrechungen. Insbesondere die Phase des Einrichtens ist für Unternehmen eine der teuersten Phasen, da zum einem der Stanzautomat nicht produzieren kann und zum anderen meistens auch hoch qualifizierte Fachkräfte diese Tätigkeit durchführen.
In diesem Punkt stellt das sogenannte Try-Out-Wheel mit seinen Funktionen eine klare Verbesserung gegenüber der Vergangenheit dar. Mit diesem Handrad können alle elementaren Achsen (Vorschub, Stößelfeinverstellung und Stößelhub) hochgenau verfahren und eingestellt werden, eine Rückwärtsbewegung durch den UT ist ebenso möglich wie die Einzelstanzung mit voller Presskraft.
Ein Vergleich zu herkömmlichen Antrieben zeigt die Vorteile des Servoantriebs
Wie deutlich die Vorteile der FSD-Technologie sind, zeigt am besten der direkte Vergleich zwischen herkömmlichen Antrieben und der neuen FSD-Technologie. Betrachtet sei beispielsweise die Produktion eines Stanzteiles auf einer konventionellen Exzenterpresse, bei der die Hubzahl produktionsbedingt auf 60 Hübe pro min begrenzt ist, da die maximal mögliche Umformgeschwindigkeit im unteren Totpunkt keine höhere Hubzahl zulässt.
Beim Einsatz der FSD-Technologie bleibt die Umformgeschwindigkeit im Bereich von 150 bis 180° mit 60 Hübe pro min unverändert, während sie in der Beschleunigungsphase nach dem UT beispielsweise auf 120 Hübe pro min ansteigt, um in der Abbremsphase nach dem OT wieder auf den Wert von 60 Hübe pro min zu sinken. Daraus ergibt sich eine mittlere Hubzahl von 95 Hübe pro min und damit eine Produktionssteigerung dank FSD-Technologie von etwa 42%.
Servoantrieb erhöht Produktivität von Stanzautomaten um 185%
Noch deutlicher fällt der Produktivitätsgewinn bei einem Stanzautomaten aus, der materialbedingt mit nur 20 Hüben pro min arbeitet. Durch die Beschleunigungsphase nach dem UT und die Abbremsphase nach dem OT lässt sich eine mittlere Hubzahl von 57 Hübe pro min und eine Produktivitätssteigerung von rund 185% erreichen – sofern der Vorschub diese Steigerung der Taktraten zulässt.
Bei typischen Tiefzieh-Anwendungen kann ab einem vorgegebenen Winkel eine konstante Stößelgeschwindigkeit eingehalten werden – ein Geschwindigkeitsverlauf, wie er beim Umformen bisher nur mit hydraulischen Pressen erreicht werden konnte. Und selbst extrem langsame Umformgeschwindigkeiten, wie sie bei manchen Präge- oder Biegeprozessen erforderlich sind, können mit der FSD-Technologie erreicht werden.
Servoantrieb mit besonderen Vorteilen beim Prägen und Biegen
Einen zusätzlichen Vorteil bietet die Servotechnologie gerade beim Prägen und Biegen. Die Lösung von Haulick + Roos ermöglicht eine frei einstellbare Verharrungszeit (Wartezeit) des Stößels im unteren Totpunkt. Hierdurch bietet sich dem Nutzer die Möglichkeit, für anspruchsvolle Formteile ein Fließen des Materials zu ermöglichen. Damit werden die Teilequalität und die wirtschaftliche Nutzung des Automaten auf lange Sicht deutlich gesteigert.
Auch bei der Betrachtung des Energieverbrauchs schneidet die FSD-Technologie hervorragend ab, denn zum einen weisen Servomotoren einen höheren Wirkungsgrad als Gleich- oder Drehstromantriebe auf, zum anderen steht dem zusätzlichen Stromverbrauch durch die Drehzahlerhöhung eine Energierückgewinnung beim Bremsen gegenüber.
Die hohen kurzzeitigen Stromaufnahmen während der Beschleunigungsphasen, die in schwach ausgelegten Stromnetzen zu Spannungsschwankungen führen können, lassen sich durch spezielle Kondensator-Module, die Stromspitzen beim Beschleunigen oder Bremsen ausgleichen, kompensieren. Die erforderliche Anzahl dieser Module kann durch den Anbieter individuell, basierend auf Kundenangaben, berechnet werden.
Der Anwender hat die Auswahl zwischen den Antriebsgrößen
Seit der Markteinführung hat sich die Servotechnologie von Haulik + Roos als führend etabliert. Um diese Position zu halten und den Vorsprung noch auszubauen, wird der Pforzheimer Hersteller von Präzisions-Stanz- und -Umformautomaten auf der diesjährigen Blechexpo in Stuttgart die nächste Generation der Servoantriebe für die Umformbranche vorstellen.
Eine gut abgestimmte Auswahl an Antriebsgrößen in der Kombination mit dem schon bewährten zweistufigen Getriebe bietet den Abnehmern des Pforzheimer Unternehmens die Möglichkeit, schon in der Projektierungsphase einen optimalen Produktionsprozess sicherzustellen. Je nach Anforderung können Motoren für eine deutliche Produktionssteigerung (Power Version – mit hoher Motorleistung) oder aber mit geringeren Anschaffungskosten (Economy Version – mit hoher Energieeffizienz) eingesetzt werden.
Dr. Ullrich Speer ist Leiter Vertrieb & Marketing bei der Haulick + Roos GmbH in Pforzheim, Horst Stegmüller ist freier Journalist.
Media Contact
Weitere Informationen:
http://www.maschinenmarkt.vogel.de/themenkanaele/produktion/umformtechnik/articles/236739/Alle Nachrichten aus der Kategorie: Maschinenbau
Der Maschinenbau ist einer der führenden Industriezweige Deutschlands. Im Maschinenbau haben sich inzwischen eigenständige Studiengänge wie Produktion und Logistik, Verfahrenstechnik, Fahrzeugtechnik, Fertigungstechnik, Luft- und Raumfahrttechnik und andere etabliert.
Der innovations-report bietet Ihnen interessante Berichte und Artikel, unter anderem zu den Teilbereichen: Automatisierungstechnik, Bewegungstechnik, Antriebstechnik, Energietechnik, Fördertechnik, Kunststofftechnik, Leichtbau, Lagertechnik, Messtechnik, Werkzeugmaschinen, Regelungs- und Steuertechnik.
Neueste Beiträge
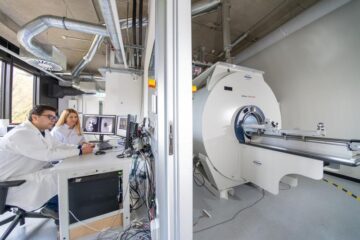
Diamantstaub leuchtet hell in Magnetresonanztomographie
Mögliche Alternative zum weit verbreiteten Kontrastmittel Gadolinium. Eine unerwartete Entdeckung machte eine Wissenschaftlerin des Max-Planck-Instituts für Intelligente Systeme in Stuttgart: Nanometerkleine Diamantpartikel, die eigentlich für einen ganz anderen Zweck bestimmt…
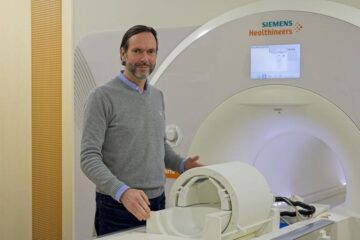
Neue Spule für 7-Tesla MRT | Kopf und Hals gleichzeitig darstellen
Die Magnetresonanztomographie (MRT) ermöglicht detaillierte Einblicke in den Körper. Vor allem die Ultrahochfeld-Bildgebung mit Magnetfeldstärken von 7 Tesla und höher macht feinste anatomische Strukturen und funktionelle Prozesse sichtbar. Doch alleine…
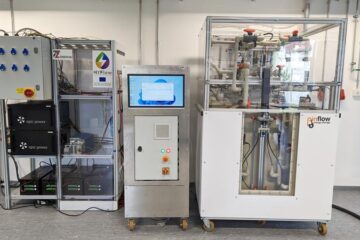
Hybrid-Energiespeichersystem für moderne Energienetze
Projekt HyFlow: Leistungsfähiges, nachhaltiges und kostengünstiges Hybrid-Energiespeichersystem für moderne Energienetze. In drei Jahren Forschungsarbeit hat das Konsortium des EU-Projekts HyFlow ein extrem leistungsfähiges, nachhaltiges und kostengünstiges Hybrid-Energiespeichersystem entwickelt, das einen…