Zweigeteilte Getriebegehäuse mit Portal-Fräsmaschinen wirtschaftlich bearbeiten
Die hohen Anforderungen an Form- und Lageabweichungen für die funktionsfähige Komplettbaugruppe verlangen größte Sorgfalt bei der mechanischen Gehäusefertigung für Großgetriebe, bestehend aus Gehäuseteil und Deckel.
Achsflucht und Bohrungsqualität der Wellenlagerpaare beeinflussen Schwingungen und Verschleiß
Gefordert sind sehr hohe Koaxialität der Lagerbohrungen bei enger Bohrungstoleranz. Dabei haben die Güte von Koaxialität (Achsflucht) und Bohrungsqualität der drei Wellenlagerpaare entscheidenden Einfluss auf auftretende Schwingungen, Geräusche sowie Verschleiß der montierten Getriebe. Diese anspruchsvollen Funktionsvorgaben der Getriebe erfordern eigentlich die Fertigung im geschlossenen Verbund des Getriebegehäuses. Jedoch die Größe der jeweils zu fertigenden drei Lagerbohrungen in Deckel und Gehäuseteil sowie der Abstand zwischen diesen Teilen von etwa 1000 mm lassen eine derartige Bearbeitung nicht zu. Deshalb erfolgt die Fertigung des Großgetriebes auf einer Präzisions- Portalmaschine Mikromat 20 V.
Begonnen wird mit der Vorbearbeitung des Gehäuses von zwei Seiten mit 0,5 mm Aufmaß auf den genauigkeitsrelevanten Konturelementen, beispielsweise den Lagersitzen. Im Gehäuseteil werden Fräs- und Bohrbearbeitungen an der Bodenpartie durchgeführt. Nach Fertigstellung der ersten Seite des Getriebegehäuses erfolgt das Ermitteln der Lage der Formelemente durch Messtaster. Dies geschieht vor der Bearbeitung der zweiten Seite auf der Maschine und hat den weiteren Vorteil, dass das aufwändige Ausrichten des Bauteiles entfällt.
Messtaster ermittel die Lage des Gehäusedeckels
Analog vorgegangen wird bei der Vorbearbeitung des Deckels von zwei Seiten. Auch dort werden die Lagersitze mit 0,5 mm Aufmaß bearbeitet und vor der zweiten Seite erfolgt wiederum die Ermittlung der Lagen mittels Messtaster auf der Maschine. Eingespart werden die aufwändigen Ausrichtarbeiten durch Übernahme der Messdaten.
Flanschflächen werden feinstgefräst
Nach der thermisch bedingten zeitlichen Unterbrechung (zwischen Vor- und Fertigbearbeitung) sowie Lösung der Werkstückfixierung zur Realisierung höchster Genauigkeitsanforderungen erfolgt die Finishbearbeitung. Begonnen wird mit der Fertigbearbeitung der Gehäuseunterseite (Außenseite) mittels vertikaler Hauptspindel und durch den Einsatz des automatisch wechselbaren Winkelbohrkopfes für horizontal und schräg angeordnete Konturelemente wie Bohrungen, Gewinde und Flächen. Danach erfolgt das Spindeln der einzigen durchgehenden Lagersitzbohrung von außen.
Die Flanschflächen werden feinstgefräst und Dichtungsbohrungen mit Qualitätsanforderung H 6 erzeugt. In dieser Aufspannung werden ebenfalls außen liegende Durchgangsbohrungen durch Ausspindeln hergestellt. Diese fungieren als Ausrichtbohrungen für die Bearbeitung der zweiten Seite (Innenseite des Getriebegehäuses). Abschließend erfolgt die Kontrollmessung mit dem Messtaster. Danach wird das Werkstück gedreht und für die Bearbeitung der Innenseite (Oberseite des Gehäuses) vorbereitet.
Ausspindeln der drei Lagersitze mit einer Spindelverlängerung
Zunächst erfolgt die Nullpunktermittlung mittels Messtaster und Übertragung aus dem Durchgangslagersitz und Ausrichtbohrungen. Das in das Koordinatensystem des Gehäuses implantierte Maschinensystem bildet die Voraussetzung zur Fertigbearbeitung der Innenkontur. Mit der „Spindelverlängerung 600 mm“ erfolgt die Feinstbearbeitung durch Ausspindeln der drei Lagersitze in der Toleranz H 5.
Mit einem Winkelbohr- und -fräskopf geschieht die Herstellung der horizontal und schrägliegenden Konturelemente wie Flächen, Bohrungen und Gewinde. In gleicher Zuordnung findet das Ausspindeln der Stiftlochbohrungen zur späteren Genaufixierung des Deckels statt. Abschließend erfolgt die obligatorische Kontrollmessung mit dem Messtaster.
Auf der Anschraubfläche wird der vorgefertigte Deckel über die Stiftlöcher per Messtaster justiert, danach fixiert und verschraubt. Mit der Hauptspindel erfolgt vorgabegerecht die Finishbearbeitung der drei Lagersitze durch Ausspindeln in der Qualität H 6. Die Kontrollmessung mit Messtaster bildet den Abschluss der Operation. Ein Komplettvermessen und Dokumentieren der Daten des Getriebegehäuses schließt die Fertigung und Zertifizierung ab.
Aufgrund der volumetrischen Genauigkeit, also der hochpräzisen Ausführung der Geometrie der Mikromat-Portalfräsmaschinen, und des Einsatzes von Zusatzkomponenten wie Winkelbohr- und -fräskopf sowie Spindelverlängerung werden Koaxialitäten der Lagerbohrungen über einen Lagerabstand von etwa 1000 mm mit einer Genauigkeit von
Trotz nicht realisierbarer Komplettbearbeitung von Gehäuse und Deckel und ohne zusätzliche, kostenintensive Aufnahmevorrichtungen ermöglichen die Portalfräsmaschinen in Verbindung mit einem Messtaster die qualitätsgerechte Fertigung.
Dipl.-Ing. Thomas Warnatsch ist geschäftsführender Gesellschafter der Mikromat GmbH in 01239 Dresden.
Media Contact
Alle Nachrichten aus der Kategorie: Maschinenbau
Der Maschinenbau ist einer der führenden Industriezweige Deutschlands. Im Maschinenbau haben sich inzwischen eigenständige Studiengänge wie Produktion und Logistik, Verfahrenstechnik, Fahrzeugtechnik, Fertigungstechnik, Luft- und Raumfahrttechnik und andere etabliert.
Der innovations-report bietet Ihnen interessante Berichte und Artikel, unter anderem zu den Teilbereichen: Automatisierungstechnik, Bewegungstechnik, Antriebstechnik, Energietechnik, Fördertechnik, Kunststofftechnik, Leichtbau, Lagertechnik, Messtechnik, Werkzeugmaschinen, Regelungs- und Steuertechnik.
Neueste Beiträge
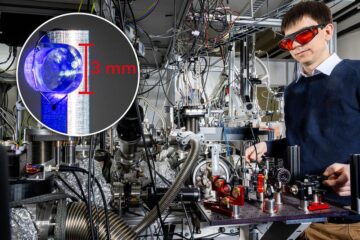
Atomkern mit Laserlicht angeregt
Dieser lange erhoffte Durchbruch ermöglicht neuartige Atomuhren und öffnet die Tür zur Beantwortung fundamentaler Fragen der Physik. Forschenden ist ein herausragender Quantensprung gelungen – sprichwörtlich und ganz real: Nach jahrzehntelanger…
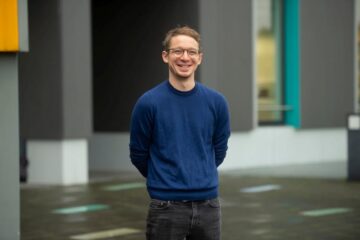
Wie das Immunsystem von harmlosen Partikeln lernt
Unsere Lunge ist täglich den unterschiedlichsten Partikeln ausgesetzt – ungefährlichen genauso wie krankmachenden. Mit jedem Erreger passt das Immunsystem seine Antwort an. Selbst harmlose Partikel tragen dazu bei, die Immunantwort…
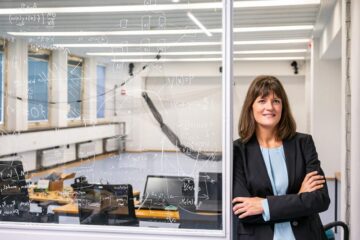
Forschende nutzen ChatGPT für Choreographien mit Flugrobotern
Robotik und ChatGPT miteinander verbinden… Prof. Angela Schoellig von der Technischen Universität München (TUM) hat gezeigt, dass Large Language Models in der Robotik sicher eingesetzt werden können. ChatGPT entwickelt Choreographien…