Lebenszyklusakte für mehr Produktivität in der Industrie 4.0: Jeder Bohrer zählt
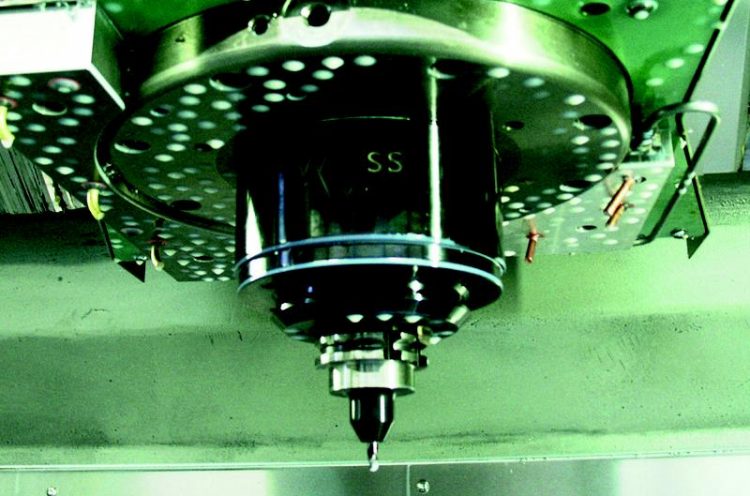
Bohrspindel im industriellen Fertigungsprozess: Mithilfe „intelligenter“ Werkzeuge für „Industrie 4.0“ lassen sich Prozesse autonom optimieren. © Fraunhofer IMS
Zahlreiche Arbeitsschritte in herstellenden Betrieben beinhalten spanabhebende Tätigkeiten: Sei es beim Bohren, Fräsen, Drehen oder Hobeln. Dabei wird jedoch nicht nur am Werkstück Material entfernt, auch das Werkzeug verschleißt nach und nach. Wann der Zeitpunkt für den Austausch oder das Nachschleifen gekommen ist, wird durch die Standzeit festgelegt.
Diese ist aufgrund der unterschiedlichen Einflüsse, denen ein Werkzeug bei seiner Arbeit ausgesetzt ist, allerdings nur schwer exakt zu bestimmen. Zwar lassen sich Werkzeugcharakteristika berechnen, die Maschineneinstellung nimmt jedoch meist ein Mitarbeiter vor und verursacht damit eine bisher nicht zurück verfolgbare Beeinflussung.
Hinsichtlich der Standzeit hat das eine Schwankungsbreite von ca. 25 Prozent zur Folge. Um Stillstände und Werkstückschäden zu vermeiden, werden Werkzeuge daher häufig zu früh gewechselt. Dies kann sich in Mehrkosten von bis zu 50 Prozent niederschlagen.
RFID-Tag ermöglicht unterbrechungsfreien Betrieb
Der Schlüssel zum Erfolg – und mehr Produktivität bei der Nutzung von Werkzeugen – ist die Bestimmung der maximal möglichen Standzeit jedes einzelnen Werkzeugs. Hierfür müssen jedoch zahlreiche individuelle Faktoren berücksichtigt werden, wie zum Beispiel die jeweilige Schneidtätigkeit, Einstellungen durch Mitarbeiter oder das Material der Werkstücke.
Die Lösung: Eine individuelle Lebenszyklusakte, in der jedes Ereignis im Leben eines Werkzeugs festgehalten wird. Basierend auf diesen Daten entsteht dann in einem speziellen Management-Tool ein digitaler Werkzeugzwilling, über den präzise ermittelt werden kann, wann ein Werkzeug ausgetauscht oder erneuert werden muss.
Wie aber kommen die Daten vom Werkzeug in das Management-Tool? Manuelles Auslesen scheidet aus. Nicht nur, weil hierfür der Betrieb unterbrochen werden muss, sondern auch, weil sich die Werkzeuge oft an unzugänglichen Orten befinden und herkömmliche Übertragungsmethoden durch das meist metallische Umfeld gestört werden.
Forscher vom Fraunhofer IMS haben diese Herausforderung mit einer neu entwickelten RFID-Technologie gelöst. Die neuen Transponder arbeiten auf einem Frequenzbereich von 5,8 GHz und können auch in der schwierigen metallischen Umgebung von Produktionsstätten aus bis zu einem Meter Entfernung ausgelesen werden. Erst dadurch wird eine effektive Kommunikation zwischen Werkzeug und Datenbank möglich. Da der RFID-Transponder eine Fläche von weniger als 5 mm2 einnimmt, kann er leicht in die Oberfläche von Werkzeugen eingebaut werden.
Neue Anwendungen für die Industrie 4.0
Herstellende Unternehmen auf dem Weg zur Industrie 4.0 profitieren von der Technik nicht nur, weil ihre Werkzeuge optimal ausgelastet werden. »Ein großer Aspekt der Industrie 4.0 ist das Erfassen von Daten, um einen möglichst transparenten Produktionsprozess zu erreichen. Die neue Lösung weist genau in diese Richtung«, weiß Dr. Gerd vom Bögel, Leiter des Geschäftsfelds »Wireless & Transponder Systems« beim Fraunhofer IMS.
»Zwar geht es im ersten Schritt um die Identifikation des Werkzeugs, im weiteren Projektverlauf könnten die Sensoren aber auch dazu dienen, nicht nur werkzeugbezogene Daten zu liefern, sondern auch Informationen über die Umgebung des Werkzeugs zu erfassen. Dadurch wird es möglich, den Prozess in Echtzeit zu überwachen, ihn transparenter zu gestalten und weiter zu optimieren.«
Aber auch in anderen Bereichen der Industrie 4.0 ist der Einsatz dieser Technologie denkbar. So könnten beispielsweise alle »Assets« der untersten physikalischen Ebene wie Werkzeuge, Werkstücke, Maschinen oder Fahrzeuge mit den RFID-Tags ausgestattet werden, um eine noch breitere Informationsbasis zu schaffen. Diese kann dann dazu genutzt werden, weitere Optimierungspotentiale zu identifizieren.
Das Projektkonsortium setzt sich neben dem Fraunhofer IMS aus den Technologieunternehmen CIMSOURCE GmbH und PROMETEC Gesellschaft für Produktions- Mess- und Automatisierungstechnik mbH, der ID4US GmbH, dem Heinz Nixdorf Institut der Universität Paderborn sowie dem Anwendungspartner Sandvik Coromant Deutschland zusammen. »Cute Machining« wird im Rahmen des Programms »EFRE-NRW« durch die Landesregierung NRW und die EU gefördert.
https://www.fraunhofer.de/de/presse/presseinformationen/2017/juni/jeder-bohrer-z…
Media Contact
Alle Nachrichten aus der Kategorie: Informationstechnologie
Neuerungen und Entwicklungen auf den Gebieten der Informations- und Datenverarbeitung sowie der dafür benötigten Hardware finden Sie hier zusammengefasst.
Unter anderem erhalten Sie Informationen aus den Teilbereichen: IT-Dienstleistungen, IT-Architektur, IT-Management und Telekommunikation.
Neueste Beiträge
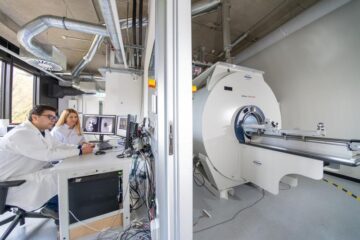
Diamantstaub leuchtet hell in Magnetresonanztomographie
Mögliche Alternative zum weit verbreiteten Kontrastmittel Gadolinium. Eine unerwartete Entdeckung machte eine Wissenschaftlerin des Max-Planck-Instituts für Intelligente Systeme in Stuttgart: Nanometerkleine Diamantpartikel, die eigentlich für einen ganz anderen Zweck bestimmt…
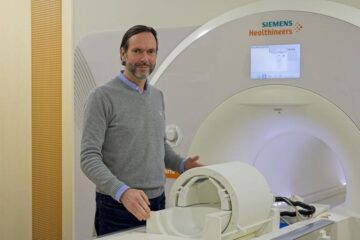
Neue Spule für 7-Tesla MRT | Kopf und Hals gleichzeitig darstellen
Die Magnetresonanztomographie (MRT) ermöglicht detaillierte Einblicke in den Körper. Vor allem die Ultrahochfeld-Bildgebung mit Magnetfeldstärken von 7 Tesla und höher macht feinste anatomische Strukturen und funktionelle Prozesse sichtbar. Doch alleine…
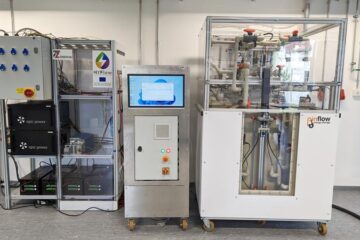
Hybrid-Energiespeichersystem für moderne Energienetze
Projekt HyFlow: Leistungsfähiges, nachhaltiges und kostengünstiges Hybrid-Energiespeichersystem für moderne Energienetze. In drei Jahren Forschungsarbeit hat das Konsortium des EU-Projekts HyFlow ein extrem leistungsfähiges, nachhaltiges und kostengünstiges Hybrid-Energiespeichersystem entwickelt, das einen…