Neue Formel und Mikrowellen beschleunigen Herstellung
Faserverbundmaterialien – vor allem auf Kohlenstoffbasis – sind aus der Industrie nicht mehr wegzudenken. Leichtbauteile werden vor allem in der Luftfahrtindustrie verwendet.
Aber auch in der Automobilindustrie und im Maschinenbau erlangen sie zur Steigerung der Energieeffizienz zunehmende Bedeutung. Doch nicht nur das geringe Gewicht machen diese Materialien so beliebt, sondern auch, dass sie nicht in allen Raumrichtungen die gleichen Eigenschaften haben müssen. Durch diese Anisotropie genannte Flexibilität können die Hersteller jede Struktur eines Bauteils individuell auf ihre Funktion hin abstimmen, denn die Faserrichtung gibt jeweils Stabilität und Elastizität vor.
Wenn Fasern etwa nur nebeneinander in einer Richtung liegen, versteift sich das Material in diese Richtung, wird aber in Richtungen senkrecht zu dieser biegsamer. Ist diese Elastizität nicht erwünscht, kann man durch verschiedene Gewebearten – wie bei Kleidungsstoff – Fasern einflechten, die das Bauteil auch in andere Richtungen stabilisieren. „Allerdings muss man die Eigenschaften für jedes Material und für jede Gewebestruktur neu messen, um sie anwenden zu können“, erklärt PD Dr. Jörg Bossert vom Lehrstuhl für Materialwissenschaft der Friedrich-Schiller-Universität Jena einen aufwendigen Teil der Herstellung.
Bossert arbeitet deshalb mit seinem Team und einigen Unternehmen im Verbundprojekt FiLiMa an einem Verfahren, durch das man in Zukunft solche Eigenschaften der Faserverbundstoffe besser berechnen kann. Auf der Fachmesse „Composites Europe 2012“ vom 9. bis 11. Oktober in Düsseldorf stellt er sein Projekt vor. „Wir benutzen zur Bestimmung der Kennwerte für unsere Simulation ein optisches Verfahren“, erläutert der Jenaer Materialwissenschaftler.
„Dabei tragen wir auf die Prüfkörper ein Punktemuster auf, das sich verändert, sobald man auf das Material eine Kraft ausübt.“ Die Verformungen werden also optisch erfasst und mit Kameras aufgezeichnet. Je nach Gewebeart und Material ergeben sich eine Reihe unterschiedlicher Werkstoffkenndaten, mit deren Hilfe die Wissenschaftler die Formeln für bestehende Berechnungsmethoden weiterentwickeln wollen.
So können z. B. Maschinenteile durch den gezielten Einsatz von Faserverbünden viel schneller und präziser bewegt werden. „Die Erkenntnisse über minimale Verformungen des Materials sind etwa bei der Produktion von Maschinen wichtig, die sich während ihres Wirkungsprozesses bewegen“, sagt Bossert. „Wenn diese schnell auf einem Luftlager bewegt werden, dann dürfen sich minimal nebeneinanderliegende Bauteile nicht verformen, da sie sich sonst berühren und damit die gesamte Einheit beschädigen.“
Weiterhin entwickeln die Jenaer Materialwissenschaftler ihre Methode weiter, Mikrowellenstrahlung bei der Herstellung von Bauteilen aus Faserverbundmaterialien einzusetzen. Während dieser Verfahrensweise werden die Fasern in einem formgebenden Werkzeug fixiert, in das flüssiges Harz injiziert wird. Die Vernetzung des Harzes zu einem Duromer, auch Aushärten genannt, erfolgt dann mit Hilfe von Mikrowellen. „Sie beschleunigen den Prozess der Aushärtung erheblich“, sagt Bossert. „Denn nur das in eine Form gegebene Material wird erhitzt, nicht die Form selbst. Energetisch ist das ein großer Vorteil“. Die reine Bestrahlungsdauer beträgt etwa zehn Minuten. Einschließlich Abkühlungszeit dauert der Vorgang weniger als eine Stunde. Andere Herstellungsprozesse brauchen mehrere Stunden. Inzwischen schaffen es die Experten von der Universität Jena auch, mit dieser Methode dreidimensionale Bauteile herzustellen.
Die Messe nutzen die Wissenschaftler bewusst, um ihre Methode mit Wissenschaftlern und Anwendern zu diskutieren und Kooperationspartner für weitere Anwendungen zu gewinnen. „Außerdem wollen wir auch diese Gelegenheit nutzen, um für den Studiengang Werkstoffwissenschaft an der Uni Jena zu werben“, sagt Bossert.
Die Universität Jena präsentiert sich auf der „Composites Europe 2012“ gemeinsam mit anderen mitteldeutschen Universitäten und Forschungseinrichtungen am Stand „Forschung für die Zukunft“ (G07) in Halle 8.
Kontakt:
PD Dr. Jörg Bossert
Institut für Materialwissenschaft und Werkstofftechnologie der Universität Jena
Löbdergraben 32, 07743 Jena
Tel.: 03641 / 947733
E-Mail: joerg.bossert[at]uni-jena.de
Media Contact
Weitere Informationen:
http://www.uni-jena.de/Alle Nachrichten aus der Kategorie: Messenachrichten
Neueste Beiträge
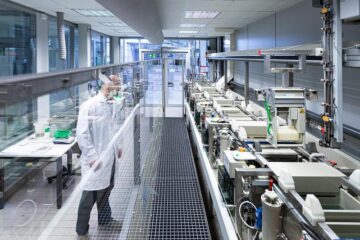
Wie die Galvanotechnik durch Digitalisierung effizient wird
SurfaceTechnology GERMANY… Digitalisierung und Hartverchromung aus Chrom(III)-Elektrolyten: Das sind die beiden großen Themen, mit denen sich Forscherinnen und Forscher von der Abteilung Galvanotechnik am Fraunhofer IPA derzeit beschäftigen. Ihre Erkenntnisse…
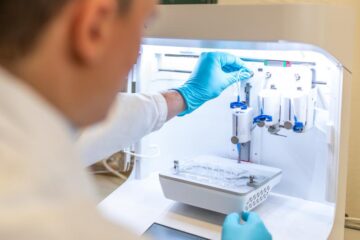
Ersatz für Tierversuche – jetzt ganz ohne Tierleid
Erstes Gewebe-Modell der Leber völlig ohne Materialien tierischer Herkunft hergestellt. Wissenschaftler*innen der TU Berlin haben mit Hilfe von 3D-Biodruck erstmals ein Modell der Leber aus menschlichen Zellen hergestellt, ohne dabei…
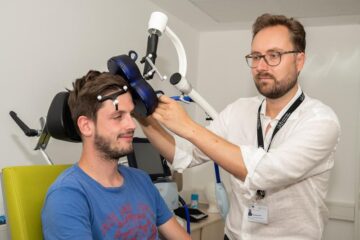
Neue Wege zur mentalen Gesundheit
Magnetspule am Kopf sorgt für antidepressive Effekte… In der Klinik und Poliklinik für Psychiatrie und Psychotherapie am Universitätsklinikum Bonn (UKB) wird derzeit eine Studie zur Erforschung der antidepressiven Wirkung einer…