Schneidstoffe und Beschichtungen für schwerzerspanbare Werkstoffe
Es ist noch nicht lange her, da bezeichnete man Werkstoffe wie Titan, Superlegierungen und rostfreie Stähle als exotische Werkstoffe. Sie kamen nur wenig vor, waren extrem teuer und die Bearbeitung stellte manchen Produzenten vor fast unlösbare Herausforderungen. Inzwischen ist von der Zerspanung von Hightech Alloys, den exotischen Werkstoffen der nächsten Generation, die Rede. Es geht um neue Legierungsansätze bei Guss, Titan, Superlegierungen und Refraktärmetallen.
Energiespartrend führt zum verstärktem Einsatz von Hochleistungsmaterialien
Diese Werkstoffe sind nach wie vor sehr teuer, werden aber heutzutage immer mehr eingesetzt und gewinnen durch ihre Eigenschaften rasant an Bedeutung. Der Energiehunger der Welt verlangt Werkstoffe, die die extreme Leistungssteigerung energieerzeugender Anlagen mit sehr hohem Wirkungsgrad unterstützen. Die Entwicklung der Leistungsfähigkeit im Kraftwerkbau, in der Wehrtechnik, in der Luft- und Raumfahrt oder der Medizintechnik ist direkt von der Entwicklung dieser Werkstoffe abhängig. Aber auch der Trend, schlichtweg Energie zu sparen, führt zum vermehrten Einsatz von Hochleistungsmaterialien.
Exotische Werkstoffe wie Titan sind in der Bearbeitung um etwa den Faktor zehn schwieriger klassifiziert als klassische Stähle. Einer der Hauptgründe liegt in der sehr schlechten Wärmeleitfähigkeit. So wird bei der Bearbeitung von Titan nur etwa ein Viertel der entstehenden Wärme durch die Späne abgeführt, der Rest führt direkt zur Erwärmung des Werkzeugs.
Beim Zerspanen exotischer Werkstoffen sind Trägerwerkzeuge mit Innenkühlung die erste Wahl
Um bei diesen Anforderungen zu bestehen, braucht man ein hochwarmfestes Hartmetallsubstrat und eine effiziente Kühlung während der Bearbeitung. Das bedeutet den Einsatz von Kühlmittel in großen Mengen, am besten mit hohem Druck durch die Spindel direkt an die Schneidkanten des Werkzeugs, was auch den Späneabtransport begünstigt. Deshalb sind für das Zerspanen von exotischen Werkstoffen Trägerwerkzeuge mit Innenkühlung erste Wahl.
Eine weitere Konsequenz der schlechten Wärmeleitfähigkeit, beispielsweise von Ti-tanlegierungen, sind die hohen Temperaturen in den Werkzeugen, die unter anderem zu chemischen Reaktionen an der Oberfläche der Werkzeugschneide führen. Die von Ceratizit entwickelte Hyper-Coat-Beschichtung wirkt dort als effizienter Schutz.
Bei massiver Kaltumformung neigt Titan zu starker Verfestigung, wobei die Zugfestigkeit sich verdreifacht und die Bruchdehnung sich um bis zu 90% verringert. Diese Verfestigungsneigung setzt dem Zerspanungsprozess einen signifikanten Widerstand entgegen, der die Schneidkanten leicht zum Ausbrechen bringt oder im Schneidstoff Zerrüttungserscheinungen hervorruft.
Titan atmet nach dem Schnittprozess auf
Eine Reduktion der Schnittkräfte durch möglichst positive und scharfe Schneiden bringt nur bis zu einem gewissen Punkt Abhilfe, weil die Schneiden, wenn die Ausgestaltung zu positiv ist, zu empfindlich werden. Die hohe Elastizität des Werkstoffs begründet eine Relaxation des Materials, die direkt nach dem Schnittprozess zu einem „Aufatmen“ des Titans führt, was besondere Anforderungen an die geometrische Freistellung der Schneidkante stellt.
Durch die extremen Eigenschaften von exotischen Werkstoffen ist meist nur eine langsame Bearbeitung, also mit niedrigen bis moderaten Schnittparametern, möglich. Die Bearbeitung ist somit sehr zeitaufwändig. Ein weiteres Merkmal ist die hohe Prozesssicherheit, die gewährleistet sein muss, denn Ausschussteile sind absolutes Tabu. Erstens handelt es sich vor allem in der Luftfahrtindustrie nicht selten um sehr große Werkstücke, deren Bearbeitung mehrere Tage in Anspruch nehmen kann, und zweitens entstehen sehr hohe Kosten, wenn große Werkstücke aus dem teuren Material nicht mehr verwendbar sind.
Bearbeitungsgeschwindigkeit bei Titan verdoppelt
Durch die lange Erfahrung auf dem Gebiet der Werkstoffwissenschaften, die sehr guten Kontakte in der Industrie, den Fokus auf schwer zu zerspanende Werkstoffe und das Know-how der Entwicklung und Anwendungstechnik hat Ceratizit sich als Spezialist für die Bearbeitung anspruchsvoller Werkstoffe etabliert. Durch Lösungen des Hartmetallexperten ist es zum Beispiel bei der Herstellung von Turbinenschaufeln aus Titan möglich, die Bearbeitungsgeschwindigkeit sogar zu verdoppeln.
Bei der Zrinski Tehnologija in Kroatien konnte man bei der Bearbeitung eines Titan-Werkstückes (3.7164, Durchmesser 21 mm, Länge 165 mm) mit einer Ceratizit-Lösung 130 Teile pro Schneidkante bearbeiten. Das sind mehr als doppelt so viele wie beim Konkurrenzprodukt, und das bei einer höheren Drehzahl der Spindel von 1400 statt 1000 min—1.
Schwer zerspanbare Werkstoffe wie Nickel-Basis-Legierungen gewinnen ebenfalls immer mehr an Bedeutung. Abgesehen von Anwendungen in der Luft- und Raumfahrt sowie der Automobilindustrie steigt der Bedarf an solchen Werkstoffen, insbesondere für Großbauteile in der Energieversorgung, beispielsweise Hoch- und Mitteldruckturbinen oder Hochdruckverdichter.
Hyper-Coat-Beschichtungen brachten den Durchbruch
Ceratizit trägt dieser Entwicklung Rechnung, indem neuartige Schneidstoffsorten mit speziellen Geometrien für die Schwerzerspanung von Hochleistungswerkstoffen gepaart wurden. Dabei brachten die Produkte mit Hyper-Coat-Beschichtungen den Durchbruch. Entwickelt wurden zwei Sorten, die diesen besonderen Anwendungsbereich großflächig abdecken. Bei der ersten Sorte, CTP5620, handelt sich um eine Feinkornsorte mit hoher Abrasionsbeständigkeit, sowohl in der Schicht als auch im Substrat. Die zweite Sorte, CTP5630, ist eine hochwarmfeste, zähe Variante, die insbesondere im instabilen Zerspanungsumfeld eine hohe Zuverlässigkeit bietet.
Neben Schneidstoff und Beschichtung spielt die richtige Schneidengeometrie eine mindestens ebenso bedeutende Rolle. So werden bei dieser Bearbeitung sehr gute Oberflächen und optimale Spanbildungen durch die spezielle Spanleitstufe beziehungsweise Schneidkante erzielt. Die für das Schäldrehen obligatorischen Stützfasen wurden für diese Anwendung angepasst, so dass ein vibrationsfreies und prozesssicheres Zerspanen gewährleistet ist.
Stangen mit Durchmessern größer als 200 mm prozesssicher bearbeiten
Die Entwicklungen wurden auf dem weltweit sehr gängigen Plattentyp YNUF 201220 angebracht. Dieser findet sowohl als Singleplatte bei kleineren Durchmessern als auch als Schlichtplatte im Tandemsystem bei großen Stangendurchmessern Anwendung. Die Bearbeitung von Nickel- und Nickel-Basis-Legierungen verlangt sehr niedrige Schnittgeschwindigkeiten von 15 bis 50 m/min bei Vorschüben von etwa 4 bis 14 mm pro Umdrehung. Höhere Schnittgeschwindigkeiten würden die Vibrationsneigung unterstützen und gegebenenfalls zu Plattenbruch oder zu Beschädigungen des Werkstücks führen.
Mit der neuen Werkzeuglösung können außer den kleineren Durchmessern von 20 bis 60 mm nun auch Stangen mit Durchmessern größer als 200 mm prozesssicher bearbeitet werden. Der charakteristische Leistungsvorteil des Schäldrehens im Vergleich zur klassischen Drehbearbeitung steht damit auch den Herstellern von großen Stangen dieser Werkstoffklasse zur Verfügung.
Dr. Uwe Schleinkofer ist Leiter Entwicklung Zerspanung bei der Ceratizit Austria GmbH, in A-6600 Reutte.
Media Contact
Weitere Informationen:
http://www.maschinenmarkt.vogel.de/themenkanaele/produktion/umformtechnik/articles/235304/Alle Nachrichten aus der Kategorie: Maschinenbau
Der Maschinenbau ist einer der führenden Industriezweige Deutschlands. Im Maschinenbau haben sich inzwischen eigenständige Studiengänge wie Produktion und Logistik, Verfahrenstechnik, Fahrzeugtechnik, Fertigungstechnik, Luft- und Raumfahrttechnik und andere etabliert.
Der innovations-report bietet Ihnen interessante Berichte und Artikel, unter anderem zu den Teilbereichen: Automatisierungstechnik, Bewegungstechnik, Antriebstechnik, Energietechnik, Fördertechnik, Kunststofftechnik, Leichtbau, Lagertechnik, Messtechnik, Werkzeugmaschinen, Regelungs- und Steuertechnik.
Neueste Beiträge
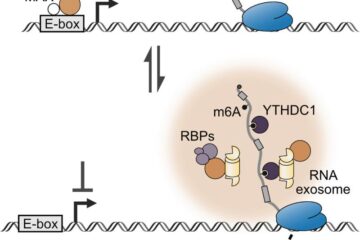
Forschende enthüllen neue Funktion von Onkoproteinen
Forschende der Uni Würzburg haben herausgefunden: Das Onkoprotein MYCN lässt Krebszellen nicht nur stärker wachsen, sondern macht sie auch resistenter gegen Medikamente. Für die Entwicklung neuer Therapien ist das ein…

Mit Kleinsatelliten den Asteroiden Apophis erforschen
In fünf Jahren fliegt ein größerer Asteroid sehr nah an der Erde vorbei – eine einmalige Chance, ihn zu erforschen. An der Uni Würzburg werden Konzepte für eine nationale Kleinsatellitenmission…
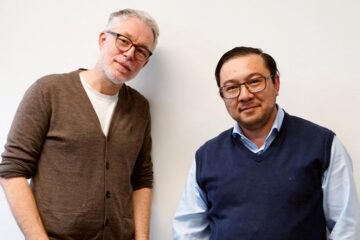
Zellskelett-Gene regulieren Vernetzung im Säugerhirn
Marburger Forschungsteam beleuchtet, wie Nervenzellen Netzwerke bilden. Ein Molekülpaar zu trennen, hat Auswirkungen auf das Networking im Hirn: So lässt sich zusammenfassen, was eine Marburger Forschungsgruppe jetzt über die Vernetzung…