Leicht und sicher: Edelstahl-Hersteller zeigen Zukunft des Autos
Nichtrostender Edelstahl kann beim Einsatz im Automobilbau zu einer Ressourcen schonenden Gewichtsersparnis führen, ohne gängige Sicherheitsstandards zu beeinträchtigen. Leicht und sicher schließen sich nicht aus, nichtrostender Edelstahl kann damit Lösungen für die steigenden Umweltanforderungen bieten.
Zu diesem Ergebnis kommt das Projekt „Next Generation Vehicle“, ein Zusammenschluss führender Edelstahl-Hersteller und Autoproduzenten. Die internationale Forschungsgruppe stellte ihre Studie heute in Frankfurt/M. anlässlich der weltgrößten Automobilmesse IAA vor.
Ziel des Ende 2004 gestarteten Projektes war es, Potenziale von nichtrostendem Edelstahl als Material im Automobilbau aufzuzeigen. Im Rahmen der Untersuchung sind innovative Werkstoffe für neue Anwendungen im Automobilbau entwickelt und getestet worden – mit zukunftsweisenden Erkenntnissen. An dem Projekt nahmen die Autoproduzenten Audi, BMW, DaimlerChrysler, Fiat, General Motors/Saab und Ford/Volvo teil. Von Seiten der Edelstahl-Hersteller waren ThyssenKrupp Nirosta (Deutschland), Outokumpu (Finnland) und ArcelorMittal Stainless (Frankreich) beteiligt.
„Die Herausforderung für das Projekt bestand in dem Spagat zwischen Gewichtsreduzierung auf Grund steigender Umwelt-Anforderungen und steigender Sicherheitsbelange“, sagte Dr. Alfred Otto, Vorstand Vertrieb der ThyssenKrupp Nirosta. „Unsere Studien belegen, dass Edelstahl Lösungen für das Auto der Zukunft bietet. Wir liefern technologisch ausgereifte und innovative nichtrostende Stähle, die es schaffen, diesen hohen Anforderungen gerecht zu werden“, betonte Dr. Otto heute in Frankfurt. „Mit diesen auf ihre Bedürfnisse zugeschnittenen Werkstoffen können sich die Automobilhersteller dem wichtigen gesamtgesellschaftlichen Ziel des Klimaschutzes von der Produktseite her zunehmend annähern.“
Der Einsatz von nichtrostendem Edelstahl ist beim Fahrzeugbau gerade in crashbeanspruchten Strukturteilen denkbar und sinnvoll. Das ist das Ergebnis der Studie, die von Entwicklungs¬Ingenieuren und Anwendungstechnikern der beteiligten Unternehmen erarbeitet wurde.
Wesentliche Vorzüge der nichtrostenden Stähle – etwa Gewichtsersparnis und hohe Festigkeit – machen einen umfassenderen Einsatz dieser Werkstoffe bei einer Ressourcen schonenden Fertigung von Fahrzeugen zweckmäßig und sinnvoll.
Zielsetzung des „Next Generation Vehicle“- Projekts ist es, Verarbeitungsrichtlinien für nichtrostende Stähle als notwendige Voraussetzung für einen Edelstahleinsatz zu erstellen. Als Referenz dienten dazu B- Säulen, die in Crashtests erprobt wurden. Die Ergebnisse wurden in Zusammenarbeit mit führenden Unternehmen abgeglichen, die Simulationsprogramme für die Metallumformung und die Simulation des Crashverhaltens für Edelstahl anbieten.
Diese Firmen entwickelten im Rahmen des „Next Generation Vehicle“ Projekts ihre Programme weiter. Die Erkenntnisse aus dem „Next Generation Vehicle“-Projekt sind zu Design- und Verarbeitungs-Guidelines zusammengefasst worden. Mit den neuen künftig auch kommerziell erhältlichen Softwareprogrammen ist eine weitere Notwendigkeit für den breiteren Einsatz von nichtrostenden Stählen erfüllt. Den Autobauern eröffnen sich dadurch neue Möglichkeiten in der Fahrzeugentwicklung.
Innerhalb des „Next Generation Vehicle“ Projekts ist auch ein Kostenmodell in Zusammenarbeit mit dem Bostoner MIT (Massachusetts Institute of Technology) erstellt worden, mit dem der Einsatz unterschiedlicher Fertigungsverfahren und Werkstoffe direkt miteinander verglichen und somit die optimale Edelstahllösung ermittelt werden kann. „Next Generation Vehicle“ wird seine Arbeit in den nächsten Monaten fortsetzen.
Nichtrostender Edelstahl bietet für Entwicklungsingenieure der Autokonzerne schon jetzt interessante Möglichkeiten. Beispielsweise haben eigens entwickelte Werkstoffe der ThyssenKrupp Nirosta bereits Eingang in den Automobilbau gefunden. Aus ihnen werden Crash-Komponenten für den Porsche Carrera GT, Überrollbügel beim Porsche Boxster, Bauteile im Audi A 6 und Rahmenkonstruktionen für den Audi A 8 gefertigt. Dadurch werden in einigen Bereichen bereits heute die Anzahl der Bauteile vermindert und Kosten eingespart.
Weitere Informationen sind im Internet unter www.ngvproject.org zu finden.
Die ThyssenKrupp Nirosta GmbH (Krefeld), ein Unternehmen der ThyssenKrupp Stainless AG, ist einer der weltweit führenden Hersteller von rostfreien Flacherzeugnissen mit einem breit gefächerten Programm von Güten, Abmessungen und Oberflächen.
ThyssenKrupp Stainless ist die Führungsgesellschaft des ThyssenKrupp Konzerns für alle Aktivitäten im Bereich nichtrostender Edelstahl-Flachprodukte sowie Nickellegierungen und Titan und beschäftigt in ihren sieben Tochtergesellschaften mit Werken in Deutschland, Italien, Mexiko, China und den USA insgesamt 12.200 Mitarbeiter.
Media Contact
Weitere Informationen:
http://www.thyssenkrupp.comAlle Nachrichten aus der Kategorie: Automotive
Die wissenschaftliche Automobilforschung untersucht Bereiche des Automobilbaues inklusive Kfz-Teile und -Zubehör als auch die Umweltrelevanz und Sicherheit der Produkte und Produktionsanlagen sowie Produktionsprozesse.
Der innovations-report bietet Ihnen hierzu interessante Berichte und Artikel, unter anderem zu den Teilbereichen: Automobil-Brennstoffzellen, Hybridtechnik, energiesparende Automobile, Russpartikelfilter, Motortechnik, Bremstechnik, Fahrsicherheit und Assistenzsysteme.
Neueste Beiträge
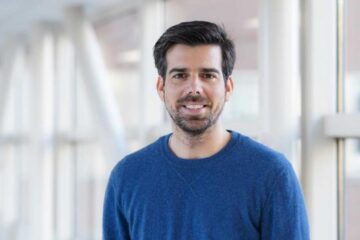
Biomarker für Therapie-Erfolg bei Tumorerkrankung im Knochenmark identifiziert
Hochrangige klinische Studie zu CAR-T-Zelltherapie beim Multiplen Myelom. Die CAR-T-Zelltherapie hat sich als wirkungsvolle Behandlung verschiedener hämatologischer Krebserkrankungen etabliert. Doch nicht bei allen Erkrankten schlägt die Therapie gleich gut an….
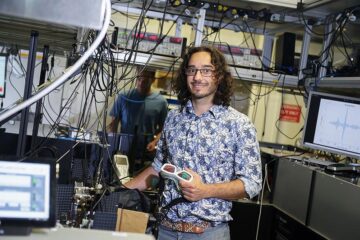
Neue universelle lichtbasierte Technik zur Kontrolle der Talpolarisation
Ein internationales Forscherteam berichtet in Nature über eine neue Methode, mit der zum ersten Mal die Talpolarisation in zentrosymmetrischen Bulk-Materialien auf eine nicht materialspezifische Weise erreicht wird. Diese „universelle Technik“…

Tumorzellen hebeln das Immunsystem früh aus
Neu entdeckter Mechanismus könnte Krebs-Immuntherapien deutlich verbessern. Tumore verhindern aktiv, dass sich Immunantworten durch sogenannte zytotoxische T-Zellen bilden, die den Krebs bekämpfen könnten. Wie das genau geschieht, beschreiben jetzt erstmals…