Komplexe Zelluloseobjekte drucken

Diese Wabe aus dem neuartigen Zelluloseverbundmaterial ist filigran und zäh zugleich. ETH Zürich / Empa / Michael Hausmann
Bäume und andere Pflanzen machen es vor: Sie stellen Zellulose selbst her und bauen daraus komplexe Strukturen mit aussergewöhnlichen mechanischen Eigenschaften.
Zellulose ist deshalb für Materialwissenschaftler attraktiv, um nachhaltige Produkte mit speziellen Funktionen herzustellen.
Das Material zu komplexen Strukturen mit hohem Zelluloseanteil zu verarbeiten, fordert Materialwissenschaftler jedoch nach wie vor heraus.
Eine Gruppe von Forschenden der ETH Zürich und der Empa haben nun einen Weg gefunden, Zellulose mittels 3D-Drucker zu verarbeiten, um fast beliebig komplexe Gegenstände mit sehr hohem Zelluloseanteil zu schaffen.
Dazu kombinierten die Forschenden das Direct Ink Writing, eine 3D-Drucktechnik, mit einem nachfolgenden Verdichtungsprozess. Damit gelang es den Materialforschenden, den Zellulosegehalt in den gedruckten Objekten auf einen Volumenanteil von 27 Prozent zu heben, wie sie in der Fachzeitschrift «Advanced Functional Materials» berichteten.
Tinte aus Wasser und Nanozellulose
Die ETH- und Empa-Forschenden sind freilich nicht die ersten, die Zellulose mit dem 3D-Drucker verarbeiten. Mit bisherigen Ansätzen, bei denen ebenfalls zellulosehaltige Druckpaste verwendet wurden, gelang es allerdings nicht, feste Objekte mit einem derart hohen Zelluloseanteil und von solch hoher Komplexität anzufertigen.
Die Druckpaste, die Hausmann und seine Kollegen einsetzen, ist denkbar einfach zusammengesetzt. Sie ist eine Dispersion aus Wasser und wenigen hundert Nanometer grossen Zellulosepartikeln und -fasern. Der Zelluloseanteil liegt zwischen sechs und 14 Prozent des Tintenvolumens.
Lösungsmittelbad verdichtet Zellulose
Der Trick der ETH-Forschenden ist, den Gegenstand nach dem Drucken in ein Bad aus organischen Lösungsmitteln einzubringen. Weil Zellulose organische Lösungsmittel abweist, lagern sich die Zellulosepartikel dicht zusammen.
Dadurch schrumpft das Objekt, was zu einer starken Zunahme der relativen Menge von Zellulosepartikel im Material führt.
In einem weiteren Schritt tauchten die Wissenschaftler den Gegenstand in eine weitere Lösung, welche ein lichtempfindliches Kunststoffmonomer enthielt. Die Monomere füllten beim Verdunsten des Lösungsmittels die Lücken des Zellulosegerüsts.
Um die Monomere in festen Kunststoff zu verwandeln, setzten die Forschenden den Gegenstand UV-Licht aus. So entstand ein Verbundmaterial mit einem Zellulosegehalt von besagten 27 Volumenprozent.
«Der Verdichtungsprozess erlaubte es uns, mit einem sechs bis 14-prozentigen Wasser-Zellulose-Gemisch anzufangen und am Ende ein Verbundmaterialobjekt mit 27 Volumenprozent von Zellulose-Nanokristallen zu erhalten», sagt Hausmann.
Elastizität lässt sich einstellen
Je nach Art des eingesetzten Kunststoffmonomers können die Forschenden die mechanischen Eigenschaften wie Elastizität oder Stärke der Druckgegenstände einstellen. Dies erlaubt es ihnen je nach Bedarf harte oder weiche Teile zu erzeugen.
Mithilfe dieses Vorgehens konnten die Forschenden verschiedene, teils filigrane und trotzdem stabile Verbundmaterialobjekte herstellen, wie etwa eine Flammenskulptur, die nur ein Millimeter dick ist. Die Verdichtung von Gegenständen mit einer Wandstärke von mehr als fünf Millimetern führt allerdings zu Verzerrungen, da sich deren Oberflächen rascher zusammenziehen als deren Inneres.
Faserausrichtung wie bei Holz
Ihre Objekte untersuchten die Forschenden mittels Röntgenanalysen und mechanischen Tests. Dabei zeigte sich, dass sich die Zellulose-Nanokristalle ähnlich ausrichten wie Zellulosefasern in natürlichem Holzmaterialien.
«Das bedeutet, dass wir die Mikrostruktur unserer Druckgegenstände so steuern können, sodass Materialien entstehen, deren Mikrostruktur derjenigen der biologischen Vorbildern wie Holz ähneln», betont Rafael Libanori, Oberassistent in der Gruppe von ETH-Professor André Studart.
Noch sind die gedruckten Stücke klein – Labormassstab eben. Doch mögliche Anwendungen gibt es viele, angefangen bei massgeschneiderten Verpackungen bis hin zu Knorpelersatz-Implantaten für Ohren.
Die Forscher haben denn auch ein Ohr nach menschlichem Vorbild angefertigt. Bis ein solches jedoch in der Klinik eingesetzt werden könnte, braucht es mehr Forschung und klinische Versuche.
An der Drucktechnik könnte auch die Autoindustrie interessiert sein. Japanische Autobauer haben bereits einen Prototyp eines Sportwagens gebaut, dessen Karosserie fast vollständig mit Zellulosebasierten Materialien gefertigt wurde.
Rafael Libanori, Complex Materials, ETH Zürich, +41 44 633 29 32, rafael.libanori@mat.ethz.ch
Hausmann MK, Siqueira G, Libanori R, Kokkinis D, Neels A, Zimmermann T, Studart AR: Complex‐Shaped Cellulose Composites Made by Wet Densification of 3D Printed Scaffolds. Advanced Functional Materials, 9. Dezember 2019. doi: 10.1002/adfm.201904127
Media Contact
Weitere Informationen:
http://www.ethz.chAlle Nachrichten aus der Kategorie: Materialwissenschaften
Die Materialwissenschaft bezeichnet eine Wissenschaft, die sich mit der Erforschung – d. h. der Entwicklung, der Herstellung und Verarbeitung – von Materialien und Werkstoffen beschäftigt. Biologische oder medizinische Facetten gewinnen in der modernen Ausrichtung zunehmend an Gewicht.
Der innovations report bietet Ihnen hierzu interessante Artikel über die Materialentwicklung und deren Anwendungen, sowie über die Struktur und Eigenschaften neuer Werkstoffe.
Neueste Beiträge
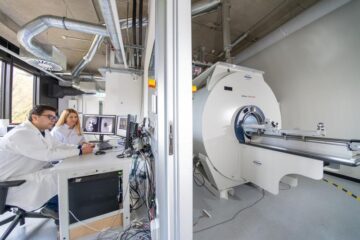
Diamantstaub leuchtet hell in Magnetresonanztomographie
Mögliche Alternative zum weit verbreiteten Kontrastmittel Gadolinium. Eine unerwartete Entdeckung machte eine Wissenschaftlerin des Max-Planck-Instituts für Intelligente Systeme in Stuttgart: Nanometerkleine Diamantpartikel, die eigentlich für einen ganz anderen Zweck bestimmt…
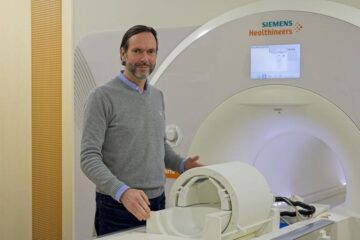
Neue Spule für 7-Tesla MRT | Kopf und Hals gleichzeitig darstellen
Die Magnetresonanztomographie (MRT) ermöglicht detaillierte Einblicke in den Körper. Vor allem die Ultrahochfeld-Bildgebung mit Magnetfeldstärken von 7 Tesla und höher macht feinste anatomische Strukturen und funktionelle Prozesse sichtbar. Doch alleine…
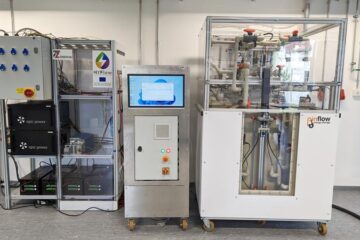
Hybrid-Energiespeichersystem für moderne Energienetze
Projekt HyFlow: Leistungsfähiges, nachhaltiges und kostengünstiges Hybrid-Energiespeichersystem für moderne Energienetze. In drei Jahren Forschungsarbeit hat das Konsortium des EU-Projekts HyFlow ein extrem leistungsfähiges, nachhaltiges und kostengünstiges Hybrid-Energiespeichersystem entwickelt, das einen…