Track & Trace Fingerprint: Bauteil-Rückverfolgung per »Fingerabdruck«

Das Fraunhofer IPM hat mit »Track & Trace Fingerprint« ein markerfreies System zur Rückverfolgung von Massenbauteilen entwickelt. © Fraunhofer IPM
In Zeiten hoch vernetzter Produktionsabläufe und globaler Zulieferketten ist es für die Industrie eine Herausforderung, einzelne Komponenten komplexer Produkte im Nachhinein zurückzuverfolgen. Bei hochpreisigen Komponenten werden RFID-Etiketten, DataMatrix-Codes oder auch chemische Marker zur Identifizierung eingesetzt. Eine lückenlose Rückverfolgbarkeit von Bauteilen und Produktionshistorien ist jedoch auch in der Massenproduktion sinnvoll, denn einmal verbaut können auch die kleinsten und auf den ersten Blick unscheinbarsten Teile die Qualität eines komplexen und teuren Endprodukts beeinträchtigen.
»Insbesondere für kleine, preissensitive Elemente wie beispielsweise elektrische Steckverbinder oder Zündkerzen sind daher praktikable und zugleich kostengünstige ›Track & Trace‹-Lösungen gefragt. Etiketten oder spezielle Markierungen erweisen sich hierbei jedoch oftmals als zu teuer oder technisch nicht realisierbar«, erklärt Dr. Alexander Förste, Projektleiter »Track & Trace Fingerprint« am Fraunhofer IPM. »Um dieser Problematik zu begegnen, haben wir mit ›Track & Trace Fingerprint‹ ein effizientes System zur Rückverfolgung von Massenbauteilen entwickelt, das die individuelle Wiedererkennung und Authentifizierung einzelner Komponenten ermöglicht.«
Auch Massenbauteile sind Unikate
Die neue Fraunhofer-Technologie nutzt die individuell ausgeprägte Mikrostruktur der Oberflächen von Bauteilen und Halbzeugen. Zunächst wird ein ausgewählter Bereich des Bauteils mit all seinen spezifischen Strukturen und deren Position mit einer Industrie-Kamera hochaufgelöst aufgenommen. Aus dem Bild wird eine charakteristische Bitfolge – der »Fingerprint« – errechnet und einer individuellen ID zugeordnet. Diese Paarung wird in einer Datenbank hinterlegt.
Die ID kann dann mit weiteren Informationen wie Mess- oder Herstellungsdaten verknüpft werden. Für eine spätere Identifizierung des Bauteils wird der Vorgang einfach wiederholt – ein Datenabgleich nach der Bildaufnahme liefert zuverlässig und fehlerfrei den entsprechenden Fingerprint-Code und somit weitere individuelle Merkmale des Bauteils.
»Das Eingravieren einer Seriennummer oder das Aufbringen eines Barcodes verbietet sich auf einer Dicht- wie auch auf einer dekorativen Oberfläche. Unser neuer Ansatz dagegen ist auch im Hinblick auf Massenbauteile effizient, praxistauglich und kostensparend: Eine große Bandbreite an Materialien eignet sich für diese Art der markierungsfreien Rückverfolgung – von glatten Kunststoffen über Aluminium und Eisenguss bis hin zu lackierten Oberflächen«, erläutert Förste.
»Der stochastische ›Fingerabdruck‹ eines Bauteils lässt sich auch bei Losgrößen von mehreren 100.000 Stück im Sekundentakt eindeutig identifizieren – dies ermöglicht eine Zuordnung von bauteilbezogenen Daten im Produktionstakt. Da keine zusätzlichen Marker oder IDs am Produkt angebracht werden, ist dieses System nicht nur fälschungssicher, sondern auch sehr ökonomisch realisierbar – es fallen schließlich keine stückzahlabhängigen Kosten an.« Die robuste Objekterkennung funktioniert durch die große Zahl möglicher Messpunkte zuverlässig auch bei Störeinflüssen wie Verunreinigungen oder Kratzern.
Ohne Rückverfolgbarkeit keine Prozessoptimierung
Eine vollständige und markierungsfreie Rückverfolgbarkeit über den gesamten Herstellungsprozess schafft einen spürbaren Mehrwert, gerade in Branchen mit hohen Qualitätsstandards wie etwa der Automobilindustrie oder der Medizintechnik. Einen ersten Prototyp des neuen Verfahrens hat das Fraunhofer IPM im Rahmen des Projekts »Track4Quality« bereits im Einsatz. Zudem wird in der zweiten Jahreshälfte 2017 bei einem Partner aus der Automobilzulieferindustrie eine Pilotinstallation in Betrieb genommen. »Unsere Technologie zeigt anschaulich, wie die Vernetzung von Digitalisierungslösungen und herkömmlichen Fertigungsprozessen im Rahmen der Industrie 4.0 in der Praxis funktioniert«, so Förste.
»Die Qualität komplexer Industrieprodukte kann von der Beschaffenheit jedes einzelnen Bauteils abhängen. Wenn ein einziger, nur wenige Cent teurer fehlerhafter Stecker die Funktionsfähigkeit und Langlebigkeit einer komplexen Elektronik-Steuerbox zum Beispiel im Automobil gefährdet, werden oft sämtliche verbaute Stecker in ›Sippenhaft‹ genommen. Unser Verfahren verhindert solch aufwendige und kostenintensive Großeingriffe in die Produktions- und Wertschöpfungskette.« Wenn produzierende Unternehmen auch kleinste Schlüsselkomponenten in der Massenproduktion rasch und zweifelsfrei zurückverfolgen können, trägt dies zur Optimierung ihrer Prozesse bei – beispielsweise bei der Verbesserung von Produktions- und Montageabläufen, bei eventuell notwendigen Rückrufaktionen oder beim Recycling.
https://www.fraunhofer.de/de/presse/presseinformationen/2017/juni/bauteil-rueckv…
Media Contact
Alle Nachrichten aus der Kategorie: Informationstechnologie
Neuerungen und Entwicklungen auf den Gebieten der Informations- und Datenverarbeitung sowie der dafür benötigten Hardware finden Sie hier zusammengefasst.
Unter anderem erhalten Sie Informationen aus den Teilbereichen: IT-Dienstleistungen, IT-Architektur, IT-Management und Telekommunikation.
Neueste Beiträge
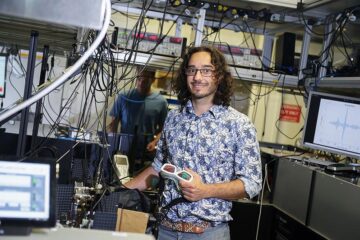
Neue universelle lichtbasierte Technik zur Kontrolle der Talpolarisation
Ein internationales Forscherteam berichtet in Nature über eine neue Methode, mit der zum ersten Mal die Talpolarisation in zentrosymmetrischen Bulk-Materialien auf eine nicht materialspezifische Weise erreicht wird. Diese „universelle Technik“…

Tumorzellen hebeln das Immunsystem früh aus
Neu entdeckter Mechanismus könnte Krebs-Immuntherapien deutlich verbessern. Tumore verhindern aktiv, dass sich Immunantworten durch sogenannte zytotoxische T-Zellen bilden, die den Krebs bekämpfen könnten. Wie das genau geschieht, beschreiben jetzt erstmals…

Immunzellen in den Startlöchern: „Allzeit bereit“ ist harte Arbeit
Wenn Krankheitserreger in den Körper eindringen, muss das Immunsystem sofort reagieren und eine Infektion verhindern oder eindämmen. Doch wie halten sich unsere Abwehrzellen bereit, wenn kein Angreifer in Sicht ist?…