Fertigung ohne Programmierkenntnisse mit Robotern automatisieren
Normalerweise programmieren oder teachen – ganz selbstverständlich – Programmierer oder Bediener den Roboter. Diese Prozesse sind meist aufwändig, vor allem zeitlich. So „lernt“ der Roboter Pfade, Bewegungen und auch Kräfte oder Grenzwerte. Nach erfolgreichem Abschluss kann er die erlernten Abläufe und Werte praktisch beliebig oft in hoher Genauigkeit wiederholen. Dies genügt vollkommen für statische Aufgaben. Andere Anforderungen in der Automatisierung stellen aber dynamische oder sich ändernde Randbedingungen und Abläufe.
Bei einfachen mechanischen spanenden Bearbeitungen können dies Maßabweichungen vom programmierten Pfad oder Hindernisse sein, bei Dauerprüfungen die sich verändernden Widerstände beziehungsweise Materialelastizitäten. Für solche Bedingungen hat ABB die Force-Control-Machining-Lösungen (FC) entwickelt. Sie basieren auf feinfühliger, in die Roboterhand integrierter Sensorik und spezifischer Software. Die Sensorik reagiert bereits auf Kraftänderungen von 10 N. Damit sind einige wichtige Funktionen und Anwendungen möglich.
Der Roboter programmiert sich selbst
Die Softwarefunktion „Lead Through Teaching – Automatic Path Learning“ unterstützt den Anwender beim einfachen Programmieren der Pfade. Im Gegensatz zum konventionellen, aufwändigen Programmierprozess erleichtern das Handbediengerät Flex-Pendant und die Software dem Bediener die Arbeit. Über die grafische Benutzeroberfläche kommt er mit wenigen Mausklicks zum Ziel. Dazu führt er den Roboter mit der Hand lediglich zu den ungefähren späteren Arbeitspositionen und gibt sie als Arbeitspunkte ein. Für diese relativ wenigen Eingaben sind bauteilabhängige Abweichungen von einigen Millimetern zulässig. Anschließend fährt der Roboter die Bauteilkontur ab und „lernt“ mit der Funktion Automatic Path Learning die tatsächlich benötigten Positionen.
In relativ kurzer Zeit sind so komplexe Pfade komplett erstellt. Zeit- und kostenintensives Programmieren entfällt – der Roboter erstellt selbst diffizilste Bearbeitungspfade. Leicht nachvollziehbar ist: Der Nutzen wird umso größer, je komplexer das Bauteil ist. So sind bis zu 90% Einsparungen der Programmierzeit möglich. Das erhöht die Effizienz der gesamten Anlage wesentlich und die Hersteller können deutlich schneller und flexibler auf Kundenwünsche reagieren.
FC Pressure sorgt beim Bearbeiten für eine konstante Anpresskraft (im rechten Winkel zum Pfad) und damit für einen konstanten Druck des Werkzeuges auf die Werkstückoberfläche. Die Vorgaben und Grenzwerte richten sich nach dem Arbeitsprozess und dem Werkstoff: automatisiertes Schleifen beziehungsweise Fräsen von Angüssen und Graten, Polieren der Oberfläche von Metallguss- oder Kunststoffteilen, Fräsen, Bohren und Schleifen von Holzwerkstücken, Verbundmaterialien aus Holz und Kunststoff oder anderen Werkstoffen.
In jeder Bearbeitungsphase erfasst die Software die Ist-Kräfte, gleicht sie mit der Soll-Vorgabe ab und adaptiert bei Bedarf die vorgegebenen Pfade. Dies stellt sicher, dass das Werkzeug immer an der Oberfläche des Werkstückes entlang fährt, das heißt, ohne unzulässig tief einzudringen – unabhängig von Konturunebenheiten und Fertigungstoleranzen. Weiter reduziert FC Pressure das Schadensrisiko für die Werkstückoberfläche und prognostiziert den Werkzeugverschleiß.
Roboter passt die Geschwindigkeit an
FC Speed-Change sorgt mit dem Ändern der Roboterbahngeschwindigkeit für konstanten Materialabtrag während des Prozesses. Denn treten zu hohe Bearbeitungswiderstände auf, reduziert die Software automatisch die Vorschubgeschwindigkeit des Roboterarms und hält so die Bearbeitungskräfte konstant. Weiter verhindert der Roboter auf diese Weise Schäden am Werkstück oder Werkzeug, die durch zu hohe mechanische und thermische Beanspruchungen entstehen könnten. Sowohl die optimale Roboterarbeitsgeschwindigkeit als auch die reduzierten Schadensrisiken beziehungsweise die erhöhte Prozesssicherheit steigern die Produktivität und Wirtschaftlichkeit des kompletten Bearbeitungsprozesses.
Aufbauend auf der ABB-Technik entwickelte ACTS, ein Tochterunternehmen der Magna International, ein vollkommen neues Prüfsystem für Autositze. Das Prüfobjekt Sitz verändert sich während des Einsitz-Tests durch die Belastung: Die Spannkraft und die Elastizität der Polsterung lassen nach. Ein konventionell ausgestatteter Roboter arbeitet an dieser Stelle iterativ; das heißt, er fährt die vorgegebene Bewegungsbahn ab und misst die erzielte Kraft. Nach jedem Zyklus gleicht er dann das Ist-Ergebnis mit dem Sollwert ab und korrigiert die Bahn für den nächsten Zyklus. So dauert es einige Zyklen, bis er den Sollwert wieder erreicht.
Anders bei Frits (Force-controlled robotic intelligent test system). Der Roboter bewegt den Belastungs-Dummy kraftgeregelt, sodass dieser immer direkt mit dem Sollwert belastet. Im Dauertest simuliert er deshalb sehr genau, realitätsnah und vor allem reproduzierbar das wiederholte Ein- und Aussteigen eines Menschen. Auf diese Weise ermittelt er das Ermüdungs- und Verschleißverhalten unter realistischen Bedingungen.
Die Messwerte der Materialermüdung oder des Materialversagens lassen sich auch als Kraft-Weg-Diagramme ausgeben. Daraus kann der Prüfer zuverlässige Rückschlüsse auf den Sitzkomfort und dessen Veränderung ziehen. Die Prüfer profitieren auch bei neuen Tests oder geänderten Vorgaben von den kurzen Programmierprozessen dank Automatic Path Learning. Die Anwendungsvielfalt des neuen Prüfsystems ist nahezu unbegrenzt. Zum Beispiel stellt die kraftgeregelte Dauerlaufprüfung von Fahrzeugkomponenten in Einbaulage (zum Beispiel Sitze, Türen und Klappen, Lenkräder und so weiter) nur eine Möglichkeit unter vielen dar.
Ein anderer Aspekt ist das Messen der Betätigungskräfte von Verstell-, Öffnungs- und Schließeinrichtungen (zum Beispiel Türgriff, Gangschaltung, Lenkrad). Was für den Fahrzeugbereich gilt, lässt sich auch auf Anwendungen in der Luftfahrt, im Schiffbau oder im allgemeinen Maschinenbau bis hin zum Prüfen der beweglichen Teile von Elektrogeräten übertragen. Dabei unterstützt das Prüfsystem Anwender mit dem direkten Protokollieren und Dokumentieren der Testreihen. Andererseits lassen sich einmal programmierte Prüfabläufe und deren Prüfungskoordinaten speichern und so die Rüst- und Programmieraufwände für Folgeversuche minimieren.
In Zukunft noch einfacher mit „gehorchender Maschine“
Im Rahmen einer europäischen Forschungsinitiative löst ABB eine Aufgabe, die der alten Vision von „aufs Wort gehorchenden Maschinen“ näher kommt: Lead Through Programming heißt diese Entwicklung. Die Forscher wollen mit ihr auch unerfahrenen Benutzern das Programmieren ermöglichen. Das innovative Konzept geht von Befehlen aus, die der Benutzer mit Hilfe von Schlüsselwörtern abruft. Er fordert den Roboter zum Beispiel auf: „Bewege dich hierher – schalte das Werkzeug ein – warte fünf Sekunden!“ Zum Programmerstellen führt der Anwender den Roboter dabei schrittweise durch den Bearbeitungsprozess.
Das System bietet ihm jeweils lediglich die Schlüsselworte oder die zu codierenden Befehle an, die in der spezifischen Situation relevant sind. Es empfängt die Befehle als gesprochenes Wort und generiert daraus das Steuerprogramm. Der Anwender schreibt weder eine Programmzeile, noch benötigt er Programmierkenntnisse. Der aufs Wort hörende Roboter bietet zukünftig auch völlig neuen, programmier- und informationstechnisch unerfahrenen Mitarbeitern die Vorzüge der automatisierten robotergestützten Produktion. An Stelle von Programmierkenntnissen zählen seine Erfahrung und sein Anwender-Know-how. Damit erhalten Betriebe und Unternehmen, die bisher roboterfern waren, neue Chancen im globalen Wettbewerb.
Franz Diedrich ist Account Manager bei der ABB Automation GmbH, Unternehmensbereich Robotics.
Media Contact
Weitere Informationen:
http://www.maschinenmarkt.vogel.de/index.cfm?pid=1568&pk=147934Alle Nachrichten aus der Kategorie: Maschinenbau
Der Maschinenbau ist einer der führenden Industriezweige Deutschlands. Im Maschinenbau haben sich inzwischen eigenständige Studiengänge wie Produktion und Logistik, Verfahrenstechnik, Fahrzeugtechnik, Fertigungstechnik, Luft- und Raumfahrttechnik und andere etabliert.
Der innovations-report bietet Ihnen interessante Berichte und Artikel, unter anderem zu den Teilbereichen: Automatisierungstechnik, Bewegungstechnik, Antriebstechnik, Energietechnik, Fördertechnik, Kunststofftechnik, Leichtbau, Lagertechnik, Messtechnik, Werkzeugmaschinen, Regelungs- und Steuertechnik.
Neueste Beiträge
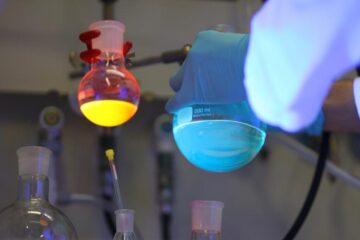
Chemischer Seiltrick auf molekularer Ebene
Mechanismusforschung hilft, wenn „Trial & Error“ versagt. In den meisten industriellen chemischen Reaktionen verbinden sich Katalysatoren mit den Ausgangsstoffen und begleiten sie über Zwischenstufen zum Produkt. Dieser Weg wird in…
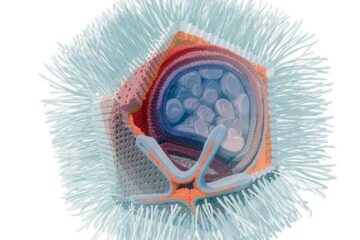
Riesenviren infizieren tödlichen Parasiten
Neues ungewöhnliches Riesenvirus in Kläranlage Klosterneuburg entdeckt. Der Einzeller Naegleria fowleri gehört zu den tödlichsten Parasiten für den Menschen. Forscher*innen des Zentrums für Mikrobiologie und Umweltsystemwissenschaft der Universität Wien um…
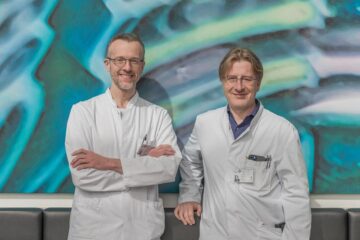
Studie belegt Vorteile von Midazolam nach Herzstillstand
Wenn nach einem Herzstillstand die Wiederbelebung erfolgreich war und der Kreislauf wieder einsetzt, ist die Patientin oder der Patient noch nicht über den Berg. In der anschließenden Phase können verschiedene…