Ein Licht geht auf

Funktionsdarstellung des Lichtleiters.
Bildquelle: Fraunhofer IPT
Leuchtpaneele aus Faserverbundkunststoff und gedruckter Elektronik sparen Energie und Ressourcen.
Alltagsgegenstände wie Leuchtmittel bieten ständig Potenzial zum Energiesparen. Nicht nur sie zu benutzen, verbraucht Energie, sondern auch sie herzustellen. Beides zu vereinen, darauf zielte das Projekt »KonFutius« unter Leitung des Fraunhofer-Instituts für Produktionstechnologie IPT in Aachen.
Die Projektpartner entwickelten einen neuen kontinuierlichen Herstellungsprozess für Leuchtpaneele, der bis zu 60 Prozent der Produktionskosten einsparen kann. Dafür kombinierten sie leichte Faserverbundkunststoffe (FVK), druckbare leitfähige Elektronikkomponenten und energiesparendes Leuchtendesign mit so genannter Edgelight-Technologie.
Im Projekt »KonFutius«, mit vollem Namen »Kontinuierliche Funktionalisierung von Leichtbaustrukturwerkstoffen im Rolle-zu-Rolle-Prozess durch Printed Electronics und Hybrid Integration«, automatisierten die Projektpartner einen kontinuierlichen Herstellungsprozess für Leuchtmittel weitgehend, der bisher manuell durchgeführt wurde.
Neuer Herstellungsprozess im Rolle-zu-Rolle-Verfahren
Im ersten Prozessschritt bedrucken die Projektpartner eine 300 mm breite Reflexionsfolie mit leitfähiger Tinte. Die Reflexionsfolienbahn bewegt sich nun kontinuierlich durch die Anlage. Direkt auf die Folie werden anschließend Elektronikkomponenten, wie LEDs und Widerstände, aufgebracht. Zum Befestigen der Elektronikkomponenten wird leitfähiger Klebstoff auf den Kontaktpunkten verwendet.
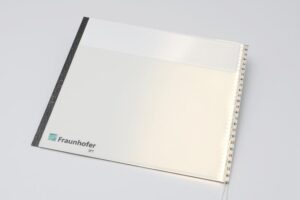
Bildquelle: Fraunhofer IPT
Im Anschluss wird die Reflexionsfolienbahn beim beteiligten Fraunhofer-Institut für Lasertechnik ILT in einem Laserschneidprozesses in einzelne Segmente zerteilt. Diese einzelnen Foliensegmente werden automatisiert in das Gehäuse aus FVK-Material montiert. Am Ende der Montagekette wird der Lichtleiter in das FVK-Gehäuse eingelegt und eine Diffusorplatte darauf angebracht. Durch die automatisierte Montage laufen alle Schritte in der Produktion parallel ab. Dies spart erheblichen Handling- und Ressourcenaufwand.
Ein weiterer Vorteil: Im Vergleich mit herkömmlichen Materialien weist die gesamte Leuchte, vor allem aufgrund des FVK-Gehäuses, ein geringeres Gewicht auf. Eingesetzt als Innenbeleuchtung in Fahrzeugen wie Autos, Bussen und Bahnen würden so weitere Ressourcen eingespart.
Standard-Leuchtpaneel zeigt Industriereife des Prozesses
Um zu demonstrieren, dass der neue Prozess tatsächlich im industriellen Einsatz Kosten und Ressourcen spart, wählten die Projektpartner einen Leuchtpaneel in der Größe 600 x 600 mm2 als Beispielbauteil. Üblicherweise werden solche Leuchtmittel als Standarddeckenbeleuchtung bei abgehängten Decken eingesetzt. Mit der Edgelight-Technologie können sie einen Design-Vorteil umsetzen: Der Lichtleiter verteilt das über die Kanten eingekoppelte Licht in der Fläche – dies reduziert wiederum den Energieaufwand. Die Paneele in einem kontinuierlichen Prozess herzustellen, spart allein 60 Prozent der üblichen Produktionskosten. Durch den Einsatz der neuen Technologie könne sich die deutsche Leuchtmittelindustrie einen Vorsprung auf dem Markt verschaffen, so das Fazit der Forschenden.
Laserschweißen statt Kleben
Statt das Gehäuse mit der Diffusorplatte wie üblich zu verkleben, verschweißen die Projektpartner beides mit dem Laser. Diese Prozessschritte finden bei dem beteiligten Fraunhofer-Institut für Lasertechnik ILT und der Firma Leister Technologies AG semi-kontinuierlich statt. In Parameterstudien eruierten die Projektpartner, welche Materialien sich mit dem Laser besonders gut verschweißen lassen.
Eine besondere Herausforderung im Montageprozess sind die geringen Toleranzen. Bisher war es nicht möglich, das Reflektormaterial so präzise zu falten, dass ein ausreichend geringer Abstand zwischen LEDs und Lichtleitern besteht. Den Projektpartnern gelang in der automatisierten Produktion auch dies.
Das beteiligte Aachener Zentrum für integrativen Leichtbau AZL testete darüber hinaus, ob sich die Gehäuse im Nachhinein verformen lassen. So ist es möglich, statt 2D- auch 3D-Oberflächen zu beleuchten. Dabei konnten die zusammengebauten, verschweißten Paneele tatsächlich in die passende Form gebracht werden.
Zukünftige Einsatzgebiete des Prozesses erweitern und nachhaltige Materialien nutzen
Die Projektpartner planen, den entwickelten kontinuierlichen Rolle-zu-Rolle-Prozess auch an weitere Anwendungsfelder anzupassen. Denkbar sind zum Beispiel Sensorikbauteile in der Automobilindustrie, wie die funktionsintegrierte Elektronik in Armaturen. Welche nachhaltigen Materialien künftig die verwendeten FVK ablösen oder ergänzen können, wollen die Forschenden ebenfalls analysieren.
Zum Projekt »KonFutius«
Das Projekt »KonFutius« wurde durch Mittel des Europäischen Fonds für regionale Entwicklung (EFRE) Produktion.NRW gefördert (Förderkennzeichen: EFRE-0801653). Es lief vom 1.7.2019 bis 30.6.2022.
Beteiligte Forschungseinrichtungen und Industriepartner
– Fraunhofer-Institut für Produktionstechnologie IPT, Aachen (Projektkoordination)
– Aachener Zentrum für integrativen Leichtbau (AZL) der RWTH Aachen
– Fraunhofer-Institut für Lasertechnik ILT, Aachen
– Leister Technologies Deutschland GmbH, Wuppertal
– Polyscale GmbH & Co. KG, Aachen
Wissenschaftliche Ansprechpartner:
Sebastian Dormann M.Sc.
Fraunhofer-Institut für Produktionstechnologie IPT
Steinbachstraße 17
52074 Aachen
Telefon +49 241 8904-248
sebastian.dormann@ipt.fraunhofer.de
www.ipt.fraunhofer.de
Weitere Informationen:
https://www.ipt.fraunhofer.de/de/presse/Pressemitteilungen/neue-leuchtpaneele-au…
Media Contact
Alle Nachrichten aus der Kategorie: Architektur Bauwesen
Die zukunftsorientierte Gestaltung unseres Wohn- und Lebensraumes erhält eine immer größer werdende Bedeutung. Die weltweite Forschung in den Bereichen Architektur und Bauingenieurwesen leistet hierzu einen wichtigen Beitrag.
Der innovations-report bietet Ihnen hierzu interessante Berichte und Artikel, unter anderem zu den Teilbereichen: Nachhaltiges Bauen, innovative Baumaterialien, Bautenschutz, Geotechnik, Gebäudetechnik, Städtebau, Denkmalschutz, Bausoftware und Künstliche Intelligenz im Bauwesen.
Neueste Beiträge
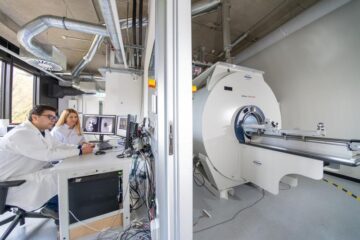
Diamantstaub leuchtet hell in Magnetresonanztomographie
Mögliche Alternative zum weit verbreiteten Kontrastmittel Gadolinium. Eine unerwartete Entdeckung machte eine Wissenschaftlerin des Max-Planck-Instituts für Intelligente Systeme in Stuttgart: Nanometerkleine Diamantpartikel, die eigentlich für einen ganz anderen Zweck bestimmt…
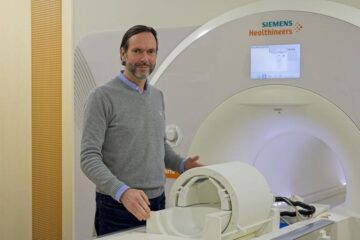
Neue Spule für 7-Tesla MRT | Kopf und Hals gleichzeitig darstellen
Die Magnetresonanztomographie (MRT) ermöglicht detaillierte Einblicke in den Körper. Vor allem die Ultrahochfeld-Bildgebung mit Magnetfeldstärken von 7 Tesla und höher macht feinste anatomische Strukturen und funktionelle Prozesse sichtbar. Doch alleine…
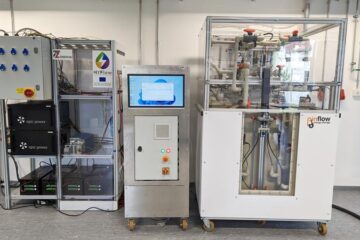
Hybrid-Energiespeichersystem für moderne Energienetze
Projekt HyFlow: Leistungsfähiges, nachhaltiges und kostengünstiges Hybrid-Energiespeichersystem für moderne Energienetze. In drei Jahren Forschungsarbeit hat das Konsortium des EU-Projekts HyFlow ein extrem leistungsfähiges, nachhaltiges und kostengünstiges Hybrid-Energiespeichersystem entwickelt, das einen…