Fraunhofer und DLR eröffnen Leichtbau-Forschungszentren in Augsburg
DLR und Fraunhofer feiern am 14. Mai mit Gästen aus Politik, Wirtschaft und Wissenschaft die Einweihung der gemeinsamen Forschungsplattform. An der Forschungsgruppe Funktionsintegrierter Leichtbau FIL des Fraunhofer-Instituts für Chemische Technologie ICT werden nun Arbeitsmöglichkeiten für etwa 55 Mitarbeiter und 25 wissenschaftliche Hilfskräfte/Studenten geschaffen. Der Bayerische Staatsminister für Wirtschaft, Infrastruktur, Verkehr und Technologie, Martin Zeil, ist Schirmherr der Veranstaltung und eröffnet die Feierlichkeiten.
»Wir verfügen über die modernsten Anlagen im Bereich der automatisierten Fertigung von kohlenstofffaserverstärkten Kunststoffen CFK. Mit unseren lokalen Partnern wie der Universität Augsburg, Premium Aerotec, Kuka, SGL, MT Aerospace, Eurocopter und vielen mehr sind wir eng vernetzt«, freut sich Prof. Dr. Klaus Drechsler, einer der beiden Leiter der Projektgruppe. Enge Verbindungen bestehen auch zum Lehrstuhl für Carbon Composites an der TU München und zum Institut für Flugzeugbau der Uni Stuttgart. Die Projektgruppe ist außerdem wichtiger Partner im Spitzencluster MAI Carbon mit Audi, BMW und vielen anderen. Derzeit kooperiert das FIL mit über 40 Firmen, darunter viele kleine Unternehmen.
Die Fraunhofer-Projektgruppe FIL wurde 2009 in Augsburg als Außenstelle des Fraunhofer ICT in Pfinztal bei Karlsruhe gegründet. Sie soll sich in den kommenden Jahren zu einem eigenständigen Institut entwickeln. Der Freistaat Bayern stellt für den Aufbau der Projektgruppe und den Neubau18 Mio Euro zur Verfügung. Die Stadt Augsburg beteiligt sich ebenfalls mit 3,5 Mio Euro, das BMBF mit 5,7 Mio Euro. Die Europäische Union unterstützt den FIL-Bau mit 3,9 Mio Euro. In dem sechsstöckigen Gebäude sind auf einer Fläche von etwa 1900 m² Büros und Laboratorien untergebracht sowie eine separate 1200 m² große Technikhalle für die Großanlagen. Ein zweiter Bauabschnitt ist bereits in der Vorplanung.
Know-how von DLR und Fraunhofer
Neue Produktionstechnologien sind erforderlich, um die Leichtbaumaterialien in großen Serien und kostengünstiger herstellen zu können. Die Teams der beiden Forschungseinrichtungen arbeiten an allen Produktionsschritten der Werkstoffe für den Leichtbau, denn die Nachfrage nach den kohlenstofffaserverstärkten Kunststoffen CFK für die Luft- und Raumfahrt sowie für die Automobil- und Maschinenbauindustrie steigt. Diese Materialien tragen erheblich dazu bei, Verbrauch und Emissionen von Flugzeugen, Kraftfahrzeugen und Maschinen zu reduzieren. CFK-Bauteile wiegen nur etwa halb so viel wie vergleichbare aus Stahl, sind aber genauso fest, crashsicher und rosten nicht. Die Fasern lassen sich je nach Anforderung in mehreren Lagen und verschiedenen Ausrichtungen übereinander legen. Bei Flugzeugen und Rennwagen der Formel 1 sind ein Großteil der Bauteile bereits aus CFK gefertigt. Bislang müssen solche Carbonkomponenten noch aufwändig von Hand gefertigt werden.
Forschungsbeispiele: Vollautomatische Fertigung
Für die Automobilindustrie haben die FIL-Forscher bereits ein neuartiges Herstellungsverfahren entwickelt. Dabei kombinieren sie eine üblicherweise im Textilbereich eingesetzte Flechtmaschine mit einer Pultrusionsanlage, die am Fraunhofer-Institut für Chemische Technologie ICT weiterentwickelt wurde. Die Flechtmaschine bringt die trockenen Carbonfasern in die richtige Form, die Pultrusionsmaschine ummantelt sie mit Harz. Das Besondere: Während bisher alles per Hand erledigt werden musste – die Fasern in das Werkzeug legen, ausrichten und Harz einspritzen – laufen nun alle Schritte vollautomatisch. Die Kombinationsanlage fertigt die Bauteile in einem kontinuierlichen Verfahren.
Auch für die Luftfahrtindustrie hat die Fraunhofer Projektgruppe einiges zu bieten: So entwickeln die Forscher in einem vom BMWi geförderten Vorhaben unter anderem ein vollautomatisches Fertigungsverfahren für komplexe CFK-Bauteile, gemeinsam mit ihren Kollegen von Premium Aerotec und Coriolis Composites GmbH.
Kern der Technologie ist ein Roboter mit Legekopf: Er greift die mit Harz ummantelten Carbonfasern und legt sie auf dem Werkzeug ab. In einem Folgeprozessschritt werden die Fasern ausgehärtet. Das automatisierte Verfahren eignet sich für Großserien und liefert gleichbleibend hohe Qualität. Zudem entsteht kein Verschnitt und die Fasern können belastungsgerecht abgelegt werden. »Unser Ziel ist es, die Herstellungskosten von CFK-Bauteilen um 90 Prozent zu reduzieren und das Leichtbaupotenzial größtmöglich auszuschöpfen. Das wollen wir vor allem über neue Produktionsverfahren erreichen, die sich auch für Großserien eignen,« sagt Drechsler.
Media Contact
Alle Nachrichten aus der Kategorie: Materialwissenschaften
Die Materialwissenschaft bezeichnet eine Wissenschaft, die sich mit der Erforschung – d. h. der Entwicklung, der Herstellung und Verarbeitung – von Materialien und Werkstoffen beschäftigt. Biologische oder medizinische Facetten gewinnen in der modernen Ausrichtung zunehmend an Gewicht.
Der innovations report bietet Ihnen hierzu interessante Artikel über die Materialentwicklung und deren Anwendungen, sowie über die Struktur und Eigenschaften neuer Werkstoffe.
Neueste Beiträge
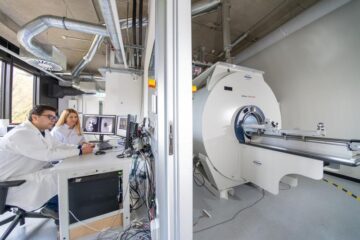
Diamantstaub leuchtet hell in Magnetresonanztomographie
Mögliche Alternative zum weit verbreiteten Kontrastmittel Gadolinium. Eine unerwartete Entdeckung machte eine Wissenschaftlerin des Max-Planck-Instituts für Intelligente Systeme in Stuttgart: Nanometerkleine Diamantpartikel, die eigentlich für einen ganz anderen Zweck bestimmt…
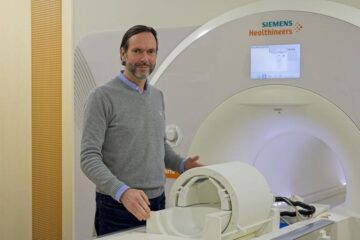
Neue Spule für 7-Tesla MRT | Kopf und Hals gleichzeitig darstellen
Die Magnetresonanztomographie (MRT) ermöglicht detaillierte Einblicke in den Körper. Vor allem die Ultrahochfeld-Bildgebung mit Magnetfeldstärken von 7 Tesla und höher macht feinste anatomische Strukturen und funktionelle Prozesse sichtbar. Doch alleine…
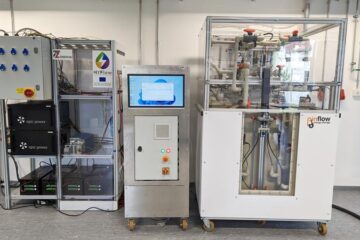
Hybrid-Energiespeichersystem für moderne Energienetze
Projekt HyFlow: Leistungsfähiges, nachhaltiges und kostengünstiges Hybrid-Energiespeichersystem für moderne Energienetze. In drei Jahren Forschungsarbeit hat das Konsortium des EU-Projekts HyFlow ein extrem leistungsfähiges, nachhaltiges und kostengünstiges Hybrid-Energiespeichersystem entwickelt, das einen…