Serienteile aus Metallpulver
Aktuelle Ergebnisse stellen die Experten auf dem International Laser Technology Congress AKL’10 vom 05. bis zum 07. Mai 2010 in Aachen vor. Das ILT feiert in diesem Jahr sein 25-jähriges Bestehen.
An Triebwerksbauteile werden höchste Anforderungen gestellt: Sie müssen sich in einer einzigen Sekunde mehr als 1 000 Mal drehen, Temperaturen von bis zu 2 000 Grad und extremen Drücken standhalten. Zudem sollen sie möglichst leicht sein und dennoch höchsten Sicherheitsstandards genügen. Die Entwicklung und Wartung der Triebwerke ist für die Ingenieure daher eine große Herausforderung.
Forscher des Fraunhofer-Institut für Lasertechnik ILT in Aachen setzen auf das selektive Laserschmelzen (Selective Laser Melting) SLM. Bei diesem Verfahren wird das Werkstück auf einer Bauplattform schichtweise aus einem pulverförmigen Werkstoff aufgebaut. Das Ganze funktioniert im Grunde wie ein Drucker, aber in drei Dimensionen. Gemäß den computergenerierten Konstruktionsdaten des geplanten Werkstücks wird das Metallpulver an den vorgegebenen Stellen aufgetragen und anschließend sofort mit einem starken Laserstrahl zum Schmelzen gebracht. Es verbindet sich dadurch fest mit dem bereits fertigen Teil des Objekts – Materialprüfungen haben erbracht, dass derartig erzeugte Komponenten eine mindestens ebenso hohe Güte aufweisen wie konventionell hergestellte.
Das SLM hat großes Potenzial: „Mit diesem Verfahren gelingt es nicht nur, beschädigte Triebwerksteile perfekt zu reparieren, sondern auch komplette Komponenten zu fertigen, die man mit konventionellen Methoden wie Fräsen oder Gießen prinzipiell nicht herstellen kann,“ sagt Dr. Konrad Wissenbach vom ILT. „Damit werden auch Geometrien und Designs möglich, von denen man bisher nicht zu träumen wagte.“ Die Zahlen sprechen für sich: Die Durchlaufzeiten für die Instandsetzung lassen sich mit diesem und weiteren lasergestützten generativen Verfahren um 40 Prozent und mehr reduzieren. Bis zu 50 Prozent des notwendigen Materials und mindestens 40 Prozent der Reparaturkosten können zukünftig eingespart werden. Wissenbach ist Koordinator des 6,5 Millionen Euro schweren EU-Projekts FANTASIA – die Abkürzung für „Flexible and near-net-shaped generative manufacturing chains and repair techniques for complex shaped aero engine parts“. Das Projekt läuft Ende Mai 2010 aus. Die erzielten Ergebnisse stellen ILT-Forscher auf dem 8. International Laser Technology Congress AKL’10 vom 05. bis zum 07. Mai 2010 in Aachen der Fachwelt vor.
Noch ist das SLM-Verfahren nicht für jeden Turbinenwerkstoff geeignet. ?Wir haben mit Inconel 718, einer Nickelbasis-Superlegierung, und Titanlegierungen schon sehr gute Ergebnisse erzielt“, sagt Wissenbach, „bei anderen rissempfindlichen Werkstoffen sind wir noch nicht ganz so weit.“ Hier erproben die ILT-Forscher noch Möglichkeiten, wie man eventuell entstandene Risse nachträglich durch Schmelzen oder Pressen wieder verschließen kann. Besser wäre es natürlich, die Bildung von Rissen ganz zu vermeiden. Deshalb experimentieren die Ingenieure mit unterschiedlichen Parametern: Sie variieren die Laserleistung, die Strahlgeometrie, die Aufbaustrategie. Oder sie erproben, wie sich eine Vorwärmung der Bauplattform auf die Qualität des Produkts auswirkt.
Auch die Produktivität des Verfahrens muss noch weiter gesteigert werden, denn bei einer Schichtdicke von 30 bis 100 Mikrometern dauert die Fertigung größerer Teile noch recht lange. „Hier können wir einen größeren Strahldurchmesser für die großen Flächen mit einem kleinen Strahl für die Konturen kombinieren“, sagt Wissenbach. „Wir wollen damit eine Verbesserung um den Faktor Zehn in der Schnelligkeit erreichen.“
Auf dem 8. International Laser Technology Congress AKL’10 feiert das Fraunhofer-Institut für Lasertechnik ILT auch sein 25-jähriges Jubiläum. 1985 gründete Prof. Gerd Herziger am Technologiestandort Aachen das Institut mit fünf Mitarbeitern. Dies löste einen Innovationsschub in der gesamten deutschen Laserforschung aus. Innerhalb kürzester Zeit avancierte das ILT zum größten Laserzentrum in Europa und beschäftigt mittlerweile über 300 Mitarbeiter. Sie entwickeln Verfahren, Systeme und Strahlquellen zum Einsatz in der Laserfertigungs- und Lasermesstechnik für Industriekunden aus den unterschiedlichsten Branchen: von der Medizintechnik über die Automobil- bis hin zur Luftfahrtindustrie.
Media Contact
Weitere Informationen:
http://www.fraunhofer.deAlle Nachrichten aus der Kategorie: Verfahrenstechnologie
Dieses Fachgebiet umfasst wissenschaftliche Verfahren zur Änderung von Stoffeigenschaften (Zerkleinern, Kühlen, etc.), Stoffzusammensetzungen (Filtration, Destillation, etc.) und Stoffarten (Oxidation, Hydrierung, etc.).
Unter anderem finden Sie Wissenswertes aus den Teilbereichen: Trenntechnologie, Lasertechnologie, Messtechnik, Robotertechnik, Prüftechnik, Beschichtungsverfahren und Analyseverfahren.
Neueste Beiträge
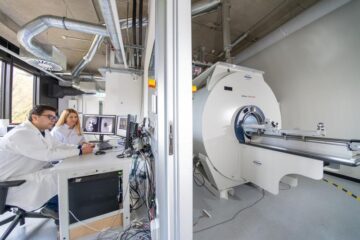
Diamantstaub leuchtet hell in Magnetresonanztomographie
Mögliche Alternative zum weit verbreiteten Kontrastmittel Gadolinium. Eine unerwartete Entdeckung machte eine Wissenschaftlerin des Max-Planck-Instituts für Intelligente Systeme in Stuttgart: Nanometerkleine Diamantpartikel, die eigentlich für einen ganz anderen Zweck bestimmt…
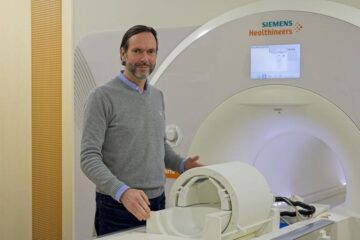
Neue Spule für 7-Tesla MRT | Kopf und Hals gleichzeitig darstellen
Die Magnetresonanztomographie (MRT) ermöglicht detaillierte Einblicke in den Körper. Vor allem die Ultrahochfeld-Bildgebung mit Magnetfeldstärken von 7 Tesla und höher macht feinste anatomische Strukturen und funktionelle Prozesse sichtbar. Doch alleine…
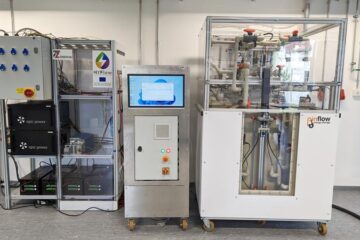
Hybrid-Energiespeichersystem für moderne Energienetze
Projekt HyFlow: Leistungsfähiges, nachhaltiges und kostengünstiges Hybrid-Energiespeichersystem für moderne Energienetze. In drei Jahren Forschungsarbeit hat das Konsortium des EU-Projekts HyFlow ein extrem leistungsfähiges, nachhaltiges und kostengünstiges Hybrid-Energiespeichersystem entwickelt, das einen…