Künstliches Kniegelenk: Kunststoff reibt Metall ab
Seine Ergebnisse tragen dazu bei, die Implantate weiter zu verbessern. Es gelangen zwar nur winzige Spuren des Metalls in den Körper, diese könnten aber bei Problemen mit der Prothese von Bedeutung sein.
Forschung zur Verbesserung künstlicher Kniegelenke, in denen Metall- und Kunststoffkomponenten aufeinander reiben, konzentrierte sich bisher hauptsächlich auf die Schwachstelle des Gelenks, den weicheren Kunststoff. Privatdozent Dr. Jan Philippe Kretzer, Biomechaniker der Orthopädischen Universitätsklinik Heidelberg, zeigte mit seinem Team erstmals, dass auch die metallische Gelenkfläche verschleißt: Rund 10 Prozent aller Partikel, die sich während mehrjähriger Belastung aus der Prothese lösen, sind metallisch. Soll zukünftig der Abrieb der Implantate weiter verringert werden, darf dieser Faktor nicht außer Acht gelassen werden. Insgesamt gelangen zwar nur geringste Mengen der Metall- und Kunststoffpartikel in den Körper, diese könnten aber langfristig Abbauprozesse der umgebenden Knochen und damit die Lockerung der Prothese fördern. Für seine Ergebnisse ist PD Dr. Kretzer mit dem Heinz-Mittelmeier-Forschungspreis der Deutschen Gesellschaft für Orthopädie und Orthopädische Chirurgie ausgezeichnet worden.
In Deutschland erhalten rund 160.000 Menschen pro Jahr einen Kniegelenksersatz. Dieser besteht aus zwei Metallkomponenten, die im Knochen verankert werden und die beschädigten Gelenkanteile in Oberschenkelknochen und Schienbein ersetzen. Zwischen diesen Metallkomponenten befindet sich eine Kunststoffeinlage, die verhindert, dass die Metalloberflächen direkt aufeinander reiben. Der im Vergleich zu Metall weicherer Kunststoff (Polyethylen) ist damit über die Jahre einer großen Belastung ausgesetzt, durch den Abrieb lösen sich kontinuierlich kleinste Partikel.
Abrieb könnte bei Problemen mit künstlichem Knie eine Rolle spielen
Die gelösten Kunststoffpartikel stehen in Verdacht, langfristig den Knochenabbau in unmittelbarer Umgebung des Implantats zu fördern. Es wird daher intensiv daran geforscht, den Verschleiß der Implantate zu verringern. „Dass sich auch aus der widerstandsfähigeren Metalloberfläche eine relevante Menge an Partikeln löst, haben wir nicht erwartet“, sagt Kretzer, Leiter des Labors für Biomechanik und Implantat-Forschung an der Orthopädischen Universitätsklinik. „Dieser Abrieb könnte bei Problemen mit künstlichen Kniegelenken ebenfalls eine Rolle spielen und sollte daher nicht vernachlässigt werden.“ So leiden einige Patienten nach der Implantation weiterhin unter Schmerzen am Knie, die – wie Erfahrungen mit künstlichen Hüftgelenken vermuten lassen – mit dem metallischen Abrieb zusammenhängen könnten.
Für die Studie ahmten die Heidelberger Biomechaniker die dreijährige Belastung eines gängigen Implantatsystems im Bewegungssimulator realitätsgetreu nach. Gelöste Partikel sammelten sich in der Flüssigkeit, die im Simulator das Gelenk umspült, und wurden mit Hilfe hochauflösender Massenspektrometrie (HR-ICP-MS) analysiert. Während der gesamten Belastung lösten sich 0,8 Milligramm, das ist weniger als ein Tausendstel Gramm, Metall, darunter Chrom und Titan, sowie rund 7 Milligramm Kunststoff. Der Anteil der Metallpartikel am gesamten Verschleiß betrug damit rund zwölf Prozent. Klinische Untersuchungen sollen nun zeigen, welche Mengen der Verschleißpartikel ins Blut von Patienten mit Knie-Prothesen gelangen und welche Auswirkungen sie haben. „Die Konzentrationen der Metallpartikel sind aber extrem gering und daher wahrscheinlich gesundheitlich unbedenklich“, sagt Kretzer.
Doch warum wird die Metalloberfläche des künstlichen Kniegelenks überhaupt von der weicheren Kunststoffkomponente abgerieben? Erst wenn die Wissenschaftler diese Frage geklärt haben, können sie den Metallabrieb bei zukünftigen Implantaten verringern.
Ansprechpartner:
Privatdozent Dr. sc. hum. Dipl.-Ing. Jan Philippe Kretzer
Labor für Biomechanik und Implantat-Forschung
Orthopädische Universitätsklinik Heidelberg
Tel.: 06221 / 562 92 09
E-Mail: Philippe.Kretzer@med.uni-heidelberg.de
Universitätsklinikum und Medizinische Fakultät Heidelberg
Krankenversorgung, Forschung und Lehre von internationalem Rang
Das Universitätsklinikum Heidelberg ist eines der bedeutendsten medizinischen Zentren in Deutschland; die Medizinische Fakultät der Universität Heidelberg zählt zu den international renommierten biomedizinischen Forschungseinrichtungen in Europa. Gemeinsames Ziel ist die Entwicklung innovativer Diagnostik und Therapien sowie ihre rasche Umsetzung für den Patienten. Klinikum und Fakultät beschäftigen rund 11.000 Mitarbeiterinnen und Mitarbeiter und engagieren sich in Ausbildung und Qualifizierung. In mehr als 50 klinischen Fachabteilungen mit ca. 2.200 Betten werden jährlich rund 118.000 Patienten voll- bzw. teilstationär und rund 1.000.000 mal Patienten ambulant behandelt. Das Heidelberger Curriculum Medicinale (HeiCuMed) steht an der Spitze der medizinischen Ausbildungsgänge in Deutschland. Derzeit studieren ca. 3.500 angehende Ärztinnen und Ärzte in Heidelberg.
Bei Rückfragen von Journalisten:
Dr. Annette Tuffs
Leiterin Unternehmenskommunikation / Pressestelle
des Universitätsklinikums Heidelberg und der
Medizinischen Fakultät der Universität Heidelberg
Im Neuenheimer Feld 672
69120 Heidelberg
Tel.: 06221 56-4536
Fax: 06221 56-4544
E-Mail: annette.tuffs@med.uni-heidelberg.de
Media Contact
Alle Nachrichten aus der Kategorie: Materialwissenschaften
Die Materialwissenschaft bezeichnet eine Wissenschaft, die sich mit der Erforschung – d. h. der Entwicklung, der Herstellung und Verarbeitung – von Materialien und Werkstoffen beschäftigt. Biologische oder medizinische Facetten gewinnen in der modernen Ausrichtung zunehmend an Gewicht.
Der innovations report bietet Ihnen hierzu interessante Artikel über die Materialentwicklung und deren Anwendungen, sowie über die Struktur und Eigenschaften neuer Werkstoffe.
Neueste Beiträge
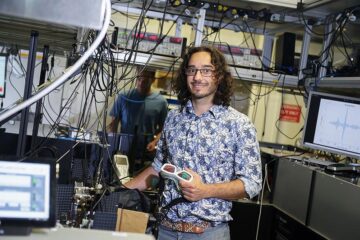
Neue universelle lichtbasierte Technik zur Kontrolle der Talpolarisation
Ein internationales Forscherteam berichtet in Nature über eine neue Methode, mit der zum ersten Mal die Talpolarisation in zentrosymmetrischen Bulk-Materialien auf eine nicht materialspezifische Weise erreicht wird. Diese „universelle Technik“…

Tumorzellen hebeln das Immunsystem früh aus
Neu entdeckter Mechanismus könnte Krebs-Immuntherapien deutlich verbessern. Tumore verhindern aktiv, dass sich Immunantworten durch sogenannte zytotoxische T-Zellen bilden, die den Krebs bekämpfen könnten. Wie das genau geschieht, beschreiben jetzt erstmals…

Immunzellen in den Startlöchern: „Allzeit bereit“ ist harte Arbeit
Wenn Krankheitserreger in den Körper eindringen, muss das Immunsystem sofort reagieren und eine Infektion verhindern oder eindämmen. Doch wie halten sich unsere Abwehrzellen bereit, wenn kein Angreifer in Sicht ist?…