Keramikschrauben – korrosions- und hitzebeständig

Eine neu designte keramische Dehnverschraubung mit 4 mm Schraubendurchmesser wird auf ihre Belastbarkeit geprüft: links real und rechts virtuell in einer Computersimulation (inverse Modellierung). © Fraunhofer IWM
Kurz nicht aufgepasst – und prompt ist man über die Bürgersteigkante gestolpert. Diagnose: Komplizierter Beinbruch.
Damit der Knochen wieder richtig zusammenwächst, verbinden Ärzte die Knochenfragmente mit Schienen. Verwenden sie dabei Metallschrauben, kann es jedoch zu Unverträglichkeiten kommen. Viele Mediziner würden daher keramische Schrauben bevorzugen.
Ebenso bei langfristigen Implantaten: Enthalten diese metallische und damit magnetisierbare Stoffe – und sei es nur eine winzige Schraube – so macht das eine Diagnostik wie Computer- und Magnetresonanz-tomografie unmöglich. Auch außerhalb von Krankenhäusern wären Keramikschrauben eine gute Alternative – etwa für chemische, elektrische und thermische Anwendungen: Sie wirken elektrisch isolierend und vertragen den Einsatz in Säuren und Laugen.
Darüber hinaus trotzen sie Temperaturen von über tausend Grad Celsius, während ihre metallischen Gegenstücke bei etwa 500 Grad Celsius erweichen. In Öfen beispielsweise, wo hohe Temperaturen herrschen, bestehen meist schon alle Teile aus Keramik – außer den Schrauben.
»Das schwächste Material begrenzt jedoch die Anwendung. Das heißt: Die Temperatur darf nur so hoch sein, wie die Schrauben sie aushalten«, sagt Christof Koplin, Wissenschaftler am Fraunhofer-Institut für Werkstoffmechanik IWM. »Mit Keramikschrauben könnte man den Techniksprung hin zur Keramik endlich vollständig vollziehen.«
Bisher stehen die Hersteller dem Werkstoff jedoch noch skeptisch gegenüber. Der Grund ist offensichtlich: Keramik ist spröde. Zwar gibt es durchaus Keramiken, die ähnlich viel aushalten wie Stahl. Verarbeitet man diese allerdings zu einer Schraube, bleiben schätzungsweise nur rund 10 bis 20 Prozent der ursprünglichen Tragkraft übrig. Wieviel Last sie tatsächlich tragen können, wussten die Schraubenhersteller bislang nicht.
Forscher am IWM in Freiburg widmen sich mit einem Schraubenprüfstand und Simulationen dieser Frage – gemeinsam mit ihren Kollegen des Fraunhofer-Instituts für Keramische Technologien und Systeme IKTS in Dresden und dem Institut für Werkzeugmaschinen und Fabrikbetrieb IWF der TU Berlin. »Wir testen verschiedene Keramikschrauben und überprüfen, wie viel sie wirklich aushalten«, erläutert Koplin. Gefördert wird das Projekt vom Bundesministerium für Wirtschaft und Energie BMWi und der Arbeitsgemeinschaft industrieller Forschung AiF.
Zudem optimieren die Wissenschaftler das Schraubendesign. So liegt eine der Herausforderungen darin, dass die Belastbarkeit bei gleich gebauten Keramikschrauben stark variiert: Während die eine viel aushält, bricht die andere bereits deutlich früher. Die Schrauben dürfen daher nur so weit belastet werden, dass auch die Schwächsten unter ihnen durchhalten. Der Grund für diese Unterschiede liegt im Aufbau der Keramik: Der Werkstoff besteht aus vielen kleinen Körnern. Verbinden sich diese bei der Herstellung nicht richtig miteinander, entsteht ein kleiner Riss, der schließlich zum Bruch führen kann.
Die Forscher haben den gesamten Herstellungsprozess nun so optimiert, dass in keinem der zahlreichen Bearbeitungsschritte solche Risse entstehen. »Wir konnten die Streuung deutlich reduzieren und damit die Belastungsgrenze der Schrauben erhöhen«, sagt Koplin. Besonders viel Potenzial für Verbesserungen sieht Koplin im letzten Arbeitsschritt, der dem Schraubengewinde eine Form verleiht – sei es über das Spritzgießen oder das Schleifen. Inzwischen können sich Schraubenhersteller an das IWM wenden und sich vom Projektteam beraten lassen, welches Design für die angestrebte Schraubenbelastung gut ist und wie der ideale Herstellungsprozess aussehen sollte.
In ihrem Prüfstand haben die Forscher auch selbst hergestellte Keramikschrauben getestet. Das Besondere an diesen Lösungen: Sie haben etwa 30 bis 35 Prozent der Tragkraft von gleich gestalteten Pendants aus Stahl. »Das ist ein großer Sprung nach vorne«, sagt Koplin. »Für viele Anwendungen würde diese Tragkraft bereits ausreichen, wenn man die Schraube etwas größer auslegt.«
Media Contact
Alle Nachrichten aus der Kategorie: Materialwissenschaften
Die Materialwissenschaft bezeichnet eine Wissenschaft, die sich mit der Erforschung – d. h. der Entwicklung, der Herstellung und Verarbeitung – von Materialien und Werkstoffen beschäftigt. Biologische oder medizinische Facetten gewinnen in der modernen Ausrichtung zunehmend an Gewicht.
Der innovations report bietet Ihnen hierzu interessante Artikel über die Materialentwicklung und deren Anwendungen, sowie über die Struktur und Eigenschaften neuer Werkstoffe.
Neueste Beiträge
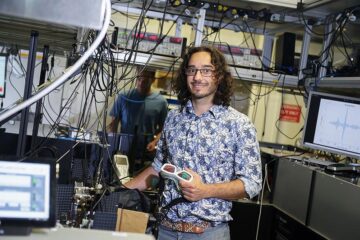
Neue universelle lichtbasierte Technik zur Kontrolle der Talpolarisation
Ein internationales Forscherteam berichtet in Nature über eine neue Methode, mit der zum ersten Mal die Talpolarisation in zentrosymmetrischen Bulk-Materialien auf eine nicht materialspezifische Weise erreicht wird. Diese „universelle Technik“…

Tumorzellen hebeln das Immunsystem früh aus
Neu entdeckter Mechanismus könnte Krebs-Immuntherapien deutlich verbessern. Tumore verhindern aktiv, dass sich Immunantworten durch sogenannte zytotoxische T-Zellen bilden, die den Krebs bekämpfen könnten. Wie das genau geschieht, beschreiben jetzt erstmals…

Immunzellen in den Startlöchern: „Allzeit bereit“ ist harte Arbeit
Wenn Krankheitserreger in den Körper eindringen, muss das Immunsystem sofort reagieren und eine Infektion verhindern oder eindämmen. Doch wie halten sich unsere Abwehrzellen bereit, wenn kein Angreifer in Sicht ist?…