Zielvorgabe Optimierung
Die Herstellung von Extrusionswerkzeugen stellt an alle Betriebsbereiche höchste Anforderungen – vor allem dann, wenn kurzfristig testlaufbedingte Änderungen durchgeführt werden müssen. Durch ein ausgetüfteltes Automationskonzept erreichte die österreichische Gruber Extrusionstechnik eine beträchtliche Verkürzung der Durchlaufzeit.
Seit mehr als zehn Jahren liefert die Firma Gruber Extrusionstechnik aus Pettenbach, Österreich, Extrusionswerkzeuge in alle Welt. Wegen der vorwiegend kundenbezogenen Profilformen sind jährlich etwa 270 Extrusionswerkzeuge mit verschiedenen Geometrien herzustellen. Dabei stellen Genauigkeitsvorgaben und Lebensdauer höchste Anforderungen an die mechanische Bearbeitung der Düsen, Düsengehäuse, Trockenkalibriereinheiten, Vakuum-Wassertanks und Wasserbäder.
Die mechanische Bearbeitung und der Änderungsdienst für die Extrusionswerkzeuge bei Gruber waren nicht mehr auf dem neuesten technischen Stand, und auch die kontinuierlich gewachsene Abteilung stieß an ihre Kapazitätsgrenzen – eine wirtschaftliche Fertigungsplanung unter Berücksichtigung der Lieferzeiten und des weltweiten Preisdrucks war nicht mehr realisierbar. Die Firmenleitung suchte nach neuen Wegen, um eigene und von den Tochterfirmen gefertigte Extrusionswerkzeuge zu testen und gegebenenfalls schnell und wirtschaftlich der Schmelzviskosität und dem Fließverhalten der Kunststoffe noch besser anzupassen.
Täglich sind acht bis zehn getestete Extrusionswerkzeuge zu ändern. In dem dafür benötigten Zeitrahmen von etwa zwei Tagen pro Werkzeug kamen bislang konventionelle Maschinen zum Einsatz – speziell Fräsmaschinen. CNC-Maschinen arbeiten ausschließlich im Erodierbereich. Wegen der vielen manuellen Tätigkeiten war der Änderungsprozess stark von einzelnen Mitarbeitern abhängig – deren individuelle Arbeitsergebnisse erfordern einen hohen Aufwand für die Nacharbeit, beispielsweise durch Polieren. Durch die Zahl der Werkzeugteile und deren Lagerplätze entstanden organisatorische und logistische Probleme.
Verbesserungswürdig war auch die Beschreibung der Arbeitsfolgen im Änderungsprozess. Ein Extrusionstechniker erfasste sie, beschrieb sie in einer Änderungsmappe und gab sie an den Schichtführer weiter, der daraus Arbeitsanweisungen für die Fräs-, Erodier-, Polier- und Montageabteilung erstellte. Vorrangiges Ziel war die Umstellung von konventionellen auf CNC-Maschinen mit Robotisierung des Werkstück- und Werkzeugwechsels für einen 24-Stunden-Tag. Gleichzeitig sollte ein neues Anlagen- und Ablauf-Layout den Standort der zu bearbeitenden Werkzeuge und Bauteile jederzeit sichtbar machen. Dazu sollte ein Produktionsplanungs- und Steuerungssystem (PPS) den gesamten Fertigungsablauf vom Auftragseingang bis zur Endmontage steuern und überwachen.
Insgesamt waren die Durchlaufzeiten um rund 20 Prozent zu senken; neben monetären und zeitlichen Vorteilen waren die Mitarbeiter von fachfremden Aufgaben zu entlasten und ihre Motivation sollte sich verbessern.Für die Automation zeichneten sich zwei Lösungen ab: Die erste Variante umfasste eine rechteckig angelegte Anlage mit zwei CNC- Fräsmaschinen und drei Schneiderodiermaschinen, beschickt von einem mittig auf Schienen geführten Knickarmroboter. Für diese Variante sprachen die relativ einfache Anlagensteuerung und die Gesamtkosten.
Nachteilig war, dass bei einem Fehler die gesamte Anlage stillsteht. Weil auch der Werkstückwechsel zu lange dauern würde, wurde diese Variante nicht zuletzt wegen der beengten Fläche in der Fertigungshalle verworfen. Mehr Vorteile versprach unterdessen Variante zwei bei gleicher Maschinenzahl und einer manuellen Fräsabteilung zum Bearbeiten der Sonderteile. Die Fräszelle sollte aus zwei von einem Roboter beschickten HSC-Fräsmaschinen, der Erodierbereich aus drei roboterbeschickten Erodiermaschinen bestehen. Für diese Variante sprachen der geringere Platzbedarf, schnelle Wechselzeiten und die Mehrmaschinenbeschickung durch den Roboter sowie die nur sequenzielle Auswirkung von möglichen Störungen. Nachteilig allerdings: Der Änderungsprozess musste in getrennt installierte Fräs- und Erodierbereiche aufgeteilt werden.
Nach der Festlegung für diese Lösungsvariante entschied sich Gruber für die Vorschläge von System 3R Schweiz zur Automation der Zellen. Das Konzept des Automationsspezialisten aus dem Kanton St. Gallen nur die Planvorstellungen und überzeugte durch weitere Vorteile, etwa gleichzeitiges Beschicken von zwei oder mehr Maschinen, den Magazinkapazitäten und der breiten Erfahrung einschließlich Peripherie mit Messmaschine, Software und Manipulator. Der für die Einzel- und Serienfertigung einsetzbare Roboter Workpartner sollte die HSC-Fräszelle automatisieren.
Bei einer Aufstellfläche von 1.895 Millimeter mal 1.835 Millimeter enthält sein Magazin sechs bis acht, bei kleineren Werkstücken auch bis zu zehn Regalebenen für Werkstücke und Werkzeuge. Die Magazinkapazität beträgt beim Fräsen und Erodieren maximal 80 Kilogramm pro Position oder 400 Kilogramm pro Regalebene. Als Spannsysteme werden die Palettensysteme GPS 240 von System 3R eingesetzt, von denen maximal fünf Paletten pro Ebene gelagert werden können. In der neuen Organisationsform beschreibt die Leitung Werkzeugbau den Arbeitsablauf – beispielsweise für einen Werkzeugtest – im PPS-System.
Die Teile durchlaufen die manuelle Fräsbearbeitung oder die Abteilung Automation, werden danach wieder zusammengeführt, in die Polier- oder Montageabteilung weitergeleitet und schließlich zum Testlauf bereitgestellt. Die neue Abteilung Automation umfasst jetzt zwei Röders-HSC-Maschinen, beschickt von einem Roboter Workpartner. Ein solcher Roboter soll in der Erodierzelle drei Schneiderodiermaschinen verschiedener Fabrikate beschicken. Dieses Automationskonzept wird dank des in der ersten Ausbaustufe erreichten Auslastungsgrades durch das palettierte Fräsen vorerst noch nicht umgesetzt.
Mit den neuen Abläufen und der Automation der Fräs- und Erodiermaschinen verkürzten sich die Durchlaufzeiten um etwa siebeneinhalb Stunden. Als Soll wurden 20 Prozent angestrebt – erreicht werden derzeit 34 Prozent. Diese Einsparung spiegelt sich in einer Mehrkapazität von 96 Werkzeugen pro Jahr oder in eingesparten Änderungskosten von durchschnittlich 72 Euro pro Werkzeug wider. Die Investitionen werden mittelfristig durch deutlich niedrigere Selbstkosten amortisiert. Von der Automation profitiert in besonderem Maße der Fräsbereich; dort konnten die Spindelstunden erhöht werden.
Media Contact
Weitere Informationen:
http://www.handling.de/xist4c/web/Zielvorgabe-Optimierung_id_882__dId_464050_.htmAlle Nachrichten aus der Kategorie: Maschinenbau
Der Maschinenbau ist einer der führenden Industriezweige Deutschlands. Im Maschinenbau haben sich inzwischen eigenständige Studiengänge wie Produktion und Logistik, Verfahrenstechnik, Fahrzeugtechnik, Fertigungstechnik, Luft- und Raumfahrttechnik und andere etabliert.
Der innovations-report bietet Ihnen interessante Berichte und Artikel, unter anderem zu den Teilbereichen: Automatisierungstechnik, Bewegungstechnik, Antriebstechnik, Energietechnik, Fördertechnik, Kunststofftechnik, Leichtbau, Lagertechnik, Messtechnik, Werkzeugmaschinen, Regelungs- und Steuertechnik.
Neueste Beiträge
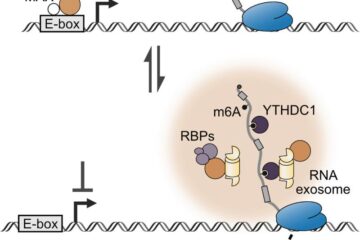
Forschende enthüllen neue Funktion von Onkoproteinen
Forschende der Uni Würzburg haben herausgefunden: Das Onkoprotein MYCN lässt Krebszellen nicht nur stärker wachsen, sondern macht sie auch resistenter gegen Medikamente. Für die Entwicklung neuer Therapien ist das ein…

Mit Kleinsatelliten den Asteroiden Apophis erforschen
In fünf Jahren fliegt ein größerer Asteroid sehr nah an der Erde vorbei – eine einmalige Chance, ihn zu erforschen. An der Uni Würzburg werden Konzepte für eine nationale Kleinsatellitenmission…
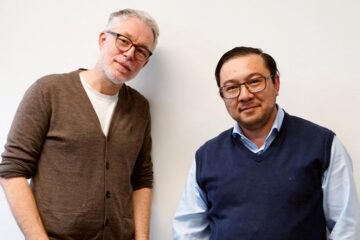
Zellskelett-Gene regulieren Vernetzung im Säugerhirn
Marburger Forschungsteam beleuchtet, wie Nervenzellen Netzwerke bilden. Ein Molekülpaar zu trennen, hat Auswirkungen auf das Networking im Hirn: So lässt sich zusammenfassen, was eine Marburger Forschungsgruppe jetzt über die Vernetzung…