Einschubwagen verhindert Stangendreher beim Schäldrehen
Schäldrehmaschinen werden vorwiegend in der Massenfertigung zur wirtschaftlichen Herstellung von Blankstahl hoher Qualität und zum Grobschälen dickwandiger Rohre sowie von gewalztem oder gegossenem Rundstahl eingesetzt. Das Schäldrehen ist ein vom Drehen abgeleitetes Fertigungsverfahren. Es handelt sich um die kinematische Umkehrung des Längs-Runddrehens mit großem Vorschub unter Verwendung eines umlaufenden Werkzeuges, durch das das Material konzentrisch hindurchgeschoben oder -gezogen wird.
Die Umsatzverteilung der letzten Jahre bei der Schumag AG hat gezeigt, dass es einen deutlichen Trend hin zur Schältechnologie gab, der erwartungsgemäß auch zukünftig anhalten wird. Grund dafür sind die deutlich gestiegenen Anforderungen an hochqualitatives und insbesondere oberflächenfehlerfreies Rundmaterial mit engen Toleranzen.
Einsatz unter anderem für Bauteile für die Energietechnik
Besonders der weltweite Boom in der Energietechnik sorgt verstärkt für Nachfrage nach Schäldrehmaschinen. Die Herstellung von Getriebewellen, Turbinenläufern, Bohrstangen und Flanschen für Rohrverbindungen sind einige typische Anwendungsfälle für das Schäldrehverfahren. Die jüngere Entwicklung innerhalb des Schälens macht ferner deutlich, dass der Markt für Blankstahl mit großen Abmessungen einen Umbruch erlebt. Wurden früher äußerst selten geschälte Stangen mit Durchmessern größer 200 mm gefordert, so ist heute dieser Bedarf an Stangenmaterial sprunghaft angestiegen.
Eine neue Maschinengeneration, die auf diese Veränderung reagiert und das Schälen geschmiedeter Stangen mit Durchmessern bis 500 mm ermöglicht, ist die PMH-Baureihe. Dieses Maschinenkonzept berücksichtigt nicht nur die technischen Anforderungen dieser Sonderanwendungen, sondern trägt auch den Forderungen nach Betriebskostenreduzierung und Flexibilität Rechnung.
Das Groß-Schälen innerhalb der Blankstahlfertigung ist eine große Herausforderung. Eine erste Anforderung besteht darin, dass in diesem Bereich häufig zerspanungstechnisch schwierige Werkstoffe wie rostfreie Stähle und auch Nickelbasislegierungen verarbeitet werden. Die Maschinen der PMH-Baureihe verfügen dazu über weitaus höhere Leistungsreserven als Vorgängermaschinen.
Des Weiteren ist das Vormaterial bei großen Stangendurchmessern in der Regel geschmiedet. Dieses Herstellungsverfahren führt jedoch dazu, dass das Vormaterial häufig krummer und unrunder ist, als man es grundsätzlich bei gewalztem Material kennt.
Nach wie vor werden geschmiedete Stangen oberhalb eines Durchmessers von 250 mm auf Drehbänken zu Blankstahl verarbeitet. Dieses Vorgehen ist in zweierlei Hinsicht ineffizient. Zum einen benötigt das Drehen eine bis zu zehnfach höhere Bearbeitungszeit. Zum anderen sind beim Drehen deutlich höhere Spanabnahmen erforderlich, um eine fehlerfreie Oberfläche zu garantieren. Dies ist darin begründet, dass die Drehbearbeitung nicht der Krümmung des Rohmaterials folgen kann, sondern zwangsläufig immer ein gerades, zylindrisches Bauteil erzeugt. Bei bisherigen Schälmaschinenkonzepten ist dies ebenso der Fall, weil herkömmliche Schälmaschinen mit starren Führungssystemen am Ein- und Auslauf arbeiten.
Bei der Schälmaschine der PMH-Baureihe verhält es sich anders: Je nach Anforderung kann diese nicht nur nach dem herkömmlichen Prinzip mit starren Führungen arbeiten, sondern die PMH kann sich bei Bedarf der Krümmung der Stange anpassen und somit eine minimale Spanabnahme realisieren.
Einschubwagen macht angepasste Führung möglich
Das Arbeitsprinzip der Führungssysteme am Ein- und Auslauf ist das folgende: Zunächst klemmt der Einschubwagen den Stab mittig und transportiert ihn zur Schäldrehmaschine. Die angetriebenen Rollen des Einlaufrollgangs sowie die im Wagenbett integrierten, ebenfalls angetriebenen Stützrollen unterstützen einen gleichmäßigen Transport des Stabes. Anschließend führt der Einschubwagen den Stabanfang in die geöffnete Einlaufführung ein. Der Einschubwagen fährt zurück in Richtung Stabende/Einlaufrollgang und spannt den Stab in einem Abstand von mindestens 3 m zur Einlaufführung. Das Spannen erfolgt hierbei außermittig.
Die Spannbacken des Einschubwagens fahren zunächst weggesteuert (drucklos) auf Kontakt zur Stange. Danach wird der Klemmdruck beidseitig gleichmäßig angehoben und an beiden Klemmzylindern konstant gehalten. Danach schiebt der Einschubwagen den Stab weiter durch die Maschine. Der Schälvorgang beginnt. Während des Schälens wird die Mitte des Prozesses von der Einlaufführung vorgegeben. Eventuelle Ungeradheiten des Stabes gleicht der Einschubwagen aus, weil die Klemmzylinder als Paket horizontal schwimmend gelagert sind.
Sobald der Stabanfang die Schälmaschine verlässt, setzt sich der Auszugwagen in Bewegung. Seine Geschwindigkeit wird mit der des Einschubwagens synchronisiert, bevor der Auszugwagen ebenfalls außermittig spannt. Für einen kurzen Moment wird der Stab sowohl im Einschubwagen als auch im Auszugwagen geklemmt, bevor der Stab vollständig an den Auszugwagen übergeben wird. Je nach Stangenlänge wird die Übergabe zwischen Einschub- und Auszugwagen mehrfach wiederholt. Nach dem Ausziehen wird der Stab von den im Wagenbett integrierten Stützrollen und den Rollen des Auslaufrollgangs abtransportiert und auf den Ablagerost abgeworfen.
Vorteile gegenüber herkömmlichem Einschubapparat
Das Arbeitsprinzip mit einem Einschubwagen hat außer der Möglichkeit, den Schäldrehprozess der Krümmung des Materials anzupassen, noch weitere Vorteile gegenüber dem Einsatz eines Einschubapparates mit Rollen. Dadurch, dass die Stange im Einschubwagen an einer festen Position geklemmt wird, kann wirksam verhindert werden, dass sie sich während des Schälprozesses dreht. Diese sogenannten Stangendreher traten bei herkömmlichen Maschinen in Kombination mit geschmiedetem, relativ ungenauem Material immer wieder auf und konnten zum Teil erhebliche Maschinenschäden verursachen.
Ein Entwicklungsziel bei der PMH-Schäldrehmaschine war es, im Verbund mit der beschriebenen schältechnischen Innovation ein über die Lebensdauer der Maschine optimiertes Betriebskostenkonzept zu realisieren. Daher ist der Aufwand für Wartung und Werkzeugwechsel bei der PMH gegenüber den Groß-Schälmachinen der Vorgängergeneration deutlich reduziert worden. So entfällt beispielsweise durch die Verwendung von verschleißfreien Spannbacken in den Spannwagen das regelmäßige Wechseln von Einschubrollen.
Ein solcher Wechsel verschlissener Rollen eines Einschubapparates verschlingt nicht nur mehrere tausend Euro Materialkosten, sondern benötigt bis zu einer halben Schicht Arbeitszeit, in der die Maschine nicht produzieren kann.
Die Schäldrehmaschine hat bereits erste Abnehmer: Ein bedeutender europäischer Stahlveredler hat sich für das neue Konzept entschieden, weitere Auftragsverhandlungen stehen vor dem Abschluss.
Dipl.-Ing. Thomas Koch ist Leiter Konstruktion bei der Schumag AG in 52076 Aachen; Dr.-Ing. Thomas Maßmann ist im selben Unternehmen Mitarbeiter in der Abteilung Projektierung Schälen, Richten, Schleifen.
Media Contact
Alle Nachrichten aus der Kategorie: Maschinenbau
Der Maschinenbau ist einer der führenden Industriezweige Deutschlands. Im Maschinenbau haben sich inzwischen eigenständige Studiengänge wie Produktion und Logistik, Verfahrenstechnik, Fahrzeugtechnik, Fertigungstechnik, Luft- und Raumfahrttechnik und andere etabliert.
Der innovations-report bietet Ihnen interessante Berichte und Artikel, unter anderem zu den Teilbereichen: Automatisierungstechnik, Bewegungstechnik, Antriebstechnik, Energietechnik, Fördertechnik, Kunststofftechnik, Leichtbau, Lagertechnik, Messtechnik, Werkzeugmaschinen, Regelungs- und Steuertechnik.
Neueste Beiträge
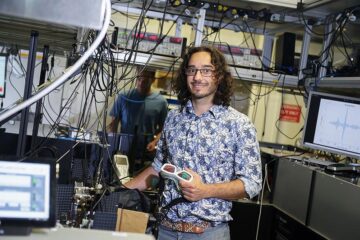
Neue universelle lichtbasierte Technik zur Kontrolle der Talpolarisation
Ein internationales Forscherteam berichtet in Nature über eine neue Methode, mit der zum ersten Mal die Talpolarisation in zentrosymmetrischen Bulk-Materialien auf eine nicht materialspezifische Weise erreicht wird. Diese „universelle Technik“…

Tumorzellen hebeln das Immunsystem früh aus
Neu entdeckter Mechanismus könnte Krebs-Immuntherapien deutlich verbessern. Tumore verhindern aktiv, dass sich Immunantworten durch sogenannte zytotoxische T-Zellen bilden, die den Krebs bekämpfen könnten. Wie das genau geschieht, beschreiben jetzt erstmals…

Immunzellen in den Startlöchern: „Allzeit bereit“ ist harte Arbeit
Wenn Krankheitserreger in den Körper eindringen, muss das Immunsystem sofort reagieren und eine Infektion verhindern oder eindämmen. Doch wie halten sich unsere Abwehrzellen bereit, wenn kein Angreifer in Sicht ist?…