Greifermodule für ölfreie Tiefziehprozesse im Automobilbau
Im Presswerk von Kia Motors in Teplicka arbeiten zwei servomotorisch angetriebene Kompakt-Saugerpressen des Typs „Rotem CTS4-5400“ aus Korea. Der Leiter des Presswerks, Se Jong Lee, gewährt einen Einblick in die vollautomatische Arbeitsweise: Stapler führen palettierte Platinenstapel an beiden Seiten der Entstapelanlage zu.Diese Entstapelanlagen kommen aus dem gleichen Hause wie die Kompakt-Saugerpressen.
Beginnend mit der automatischen Abstapelung folgt ein vierstufiger, durchgängig automatisierter Stanz- und Umformprozess bis zur automatisierten Entnahme der Fertigteile sowie der automatisierten Ablage in Spezialpaletten. Die befüllten Spezialpaletten entnimmt wiederum ein Stapler aus der Anlage.
Die Pressen bieten Tischgrößen, die es erlauben, Platinen mit einer Länge von maximal 3260 mm und einer Breite von 1630 mm zu bearbeiten. Das heißt, die Pressen sind in der Lage, komplette Seitenteile und Dächer tief zu ziehen, umzuformen und zu stanzen.
Kleinere Teile, wie Türen, werden paarweise in einem Werkzeugsatz produziert. Der gesamte automatisierte Stanz- und Umformprozess für die kleineren Teile ist so optimiert, dass mit 15 Hüben pro Minute gefahren wird. Die Pressen bei Großteilen erlauben 14 Hübe pro Minute.
Der Stanz- und Tiefziehprozess beginnt mit der automatisierten Zuführung der zu bearbeitenden Platinen. Jede der beiden Saugerpressen ist so ausgelegt, dass im Fall der Zwillingsfertigung von Teilen in einem Werkzeug die beiden Werkstücke synchron zugeführt werden. Beim Entstapeln sorgen Spreizmagnete für die zuverlässige Aufnahme von jeweils nur einer Platine.
Saugertransferbalken übernehmen das Handling der Platinen
Die Platinen durchlaufen dann zunächst eine Richtmaschine und werden danach von einem Saugertransferbalken aufgenommen und in die erste Umformstufe zum Tiefziehen eingelegt. Das komplette Handling der Werkstücke durch die vier Stufen der mechanisch arbeitenden Saugerpresse übernehmen bauartgleiche Saugerbalken, die von Transfergeräten der Güdel Group AG im Schweizer Langenthal bewegt werden.
Zum vierstufigen Umformprozess gehört eine Zwischenablage nach dem Tiefziehen in der ersten Stufe. Diese Ablagestation ermöglicht es, im Bedarfsfall das tiefgezogene Werkstück vor der weiteren Bearbeitung zu wenden.
Durch den Einbau der Zwischenablage sowie der rationellen Übergabe der Platinen an die Tiefziehwerkzeuge der ersten Umformstufe mit baugleichen Saugerbalken sind für das Werkstückhandling durch den gesamten Stanz- und Umformprozess insgesamt sechs Saugerbalken im Einsatz. Dass diese Saugerbalken baugleich sind und von baugleichen Transfer-Geräten der Firma Güdel bewegt werden, ist bereits ein erstes Indiz für die rationelle Gestaltung der technischen Prozesse.
Karbon-Fiber-Saugerbalken mit Bilsing-Werkzeugen ausgestattet
Die Karbon-Fiber-Saugerbalken aus dem Hause Bilsing Automation sind integraler Bestandteil der Werkzeugwechselwagen. Jeder Saugerbalken trägt vier Saugertoolings aus dem Bilsing-Greiferbaukasten. Dieser Baukasten umfasst alle Teile und Baugruppen, die zu einem fertigen Greifer gehören. Zur Verbindung mit dem Saugerbalken ist das Trägerrohr mit einem einfach aufgebauten und daher sicher funktionierenden Kupplungssystem ausgestattet.
Der Geschäftsführende Gesellschafter des Attendorner Unternehmens Bilsing Automation, Alfred Bilsing, beschreibt die Funktion: „Unser Kupplungssystem basiert auf einem Hakenmechanismus, der den Bajonettverschluss festklemmt und ihn beim Lösen aus den Führungen herausdrückt.
Die neuen Toolings sind nicht nur einfacher aufgebaut, sie sind auch leichter geworden. Deshalb kann man ein solches Greiferwerkzeug mit einer Hand längs zum Saugerbalken heben und es in die Aufnahmevorrichtung einführen. Mit der zweiten Hand bewegt man den Hebel, der über einen Hakenmechanismus das Tooling mit dem Saugerbalken verbindet. Dabei wird es zunächst angedrückt, dann angezogen und am Ende der Bewegung prozesssicher gespannt.“
Greifer können auch steuerungstechnische Aufgaben übernehmen
An das Trägerrohr sind Schwenkarme installiert, die die Vakuumsauger tragen, wie Bilsing weiter erläutert. Die Zahl der Sauger richte sich nach der Teilegröße. Der Greiferbaukasten könne durch Module ergänzt werden, die zusätzlich zur Handhabungsfunktion steuerungstechnische Aufgaben übernehmen.
„Bei Kia Motors Slovakia sind die Toolings mit Sensoren ausgestattet, die von einer gelben Hülle umgeben sind. Es handelt es sich dabei um mechanisch wirkende Sensoren, die detektieren, ob ein Greifer ein Werkstück aufgenommen hat oder nicht“, wie Bilsing berichtet. Auf diese Weise gehöretn die taktilen Sensoren zu einem Sicherheitssystem, das einem reibungslosen Umformprozess dient.
Zur Realisierung einer sicher ablaufenden Pressenautomatisierung gehört zunächst, dass das zum Werkzeug passende Tooling an die richtige Stelle des Saugerbalkens montiert wird. Dazu sind die beiden Saugerbalken beidseitig farblich gekennzeichnet. Die rechte Seite mit roter Farbe die linke mit grüner.
Passend dazu sind auch die Toolingwerkzeuge farblich markiert. Darüber hinaus wird jedes Tooling über den sechspoligen roten Stecker identifiziert. „Bevor die Presse gestartet wird, überprüft die Steuerung, ob an jeder Stelle das richtige Tooling installiert wurde“, so Bilsing.
Sauger müssen sehr präzise aufsetzen
Diese Saugertoolings müssen mit höchster Präzision auf das zu handhabende Teil in der Presse eingestellt sein. Solche Einstellprozesse lassen sich direkt auf der Produktionspresse, aber auch auf entsprechenden Simulatoren oder Tryout-Pressen durchführen, wo auch die entsprechenden Werkzeuge eingestellt werden.
Bei Kia Motors Slovakia müssen die Sauger in hoher Präzision im rechten Winkel auf das Blech aufsetzen. Das erfordert der Umformprozess, der in Teplicka ölfrei gefahren wird. Dieses ölfreie Umformen bietet eine Reihe von Vorzügen, erläutert Bilsing: „Man braucht zum Beispiel keine Ölwaschanlagen. Die Werkzeuge bleiben sauber. Die Handhabung von ölfreien Blechen ermöglicht es, teilweise kleinere beziehungsweise weniger Sauger einzusetzen.“
Zu den Vorzügen des Bilsing-Greifersystems gehört das bequeme Feineinstellen der Sauger auf das Umformteil: Mit einem Achter-Inbusschlüssel lassen sich Tragarme, Saugerklemmblöcke und alle anderen zum Greifer gehörenden Baugruppen festziehen und lösen, so dass sich mit geringem Aufwand Anpassungen an veränderte Oberflächengeometrien eines Blechteils ausführen lassen.
Diese Konstruktion ermöglicht es auch dem Betreiber nach entsprechender Unterweisung, aus dem Bilsing-Greiferbaukasten neue Greifer zu montieren. Die bei einem Produktwechsel auszutauschenden Greifersätze befinden sich ganz in der Nähe der Werkzeugwechselwagen auf speziellen Ablagewagen.
Saugerbalken werden automatisch ausgetauscht
Welche Kräfte die Sauger erzeugen müssen, wird deutlich, wenn man auf die Geschwindigkeit schaut, mit der die Saugerbalken in der Presse bewegt werden. Zeitgleich mit dem automatischen Wechseln der Presswerkzeuge werden auch die Saugerbalken, die sich auf den Werkzeugwechselwagen befinden und zuvor manuell mit den Toolings komplettiert wurden, automatisch ausgetauscht.
Im Arbeitsraum der Presse übernehmen die Saugerbalken-Transfergeräte der Firma Güdel die Saugerbalken. Die Steuerung dieser Geräte gehört mit zu den Grundlagen der hohen Produktivität des gesamten Umformprozesses: Die Längsbewegung der Blechwerkstücke übernehmen separat angesteuerte Lineareinheiten, die drehbar gelagert sind.
Diese Gestaltung ermöglicht die Realisierung einer wellenförmigen Bewegung der Umformteile. Auf diese Weise wird in der vorhandenen Zeit der Stößelbewegungen vom und zum Unterwerkzeug ein Werkstück entnommen und in paralleler Bewegung das nächste eingelegt.
Dabei entfalten die von Servomotoren angetriebenen Zahnriemen, die die Saugerbalken bewegen, eine Geschwindigkeit von bis zu 8 m/s und eine Beschleunigung von bis zu 3 g. Für dieses System garantiert Güdel eine Verfügbarkeit von 99%.
Baugleiche Güdel-Saugerbalken-Transfergeräte entsorgen auch das letzte Umformwerkzeug, in der drei- bis vierstufig gefahrenen Saugerpresse. Sie legen die entnommenen Fertigteile jeweils auf ein Transportband, das die Teile zur automatisierten Palettierstation fördert.
Robotergreifer ebenfalls mit taktilen Sensoren ausgestattet
Durch die hohe Produktivität der Saugerpresse mit 30 Umformteilen pro Minute braucht man zum automatisierten Palettieren der Fertigteile vier, auf Säulen montierte Kuka-Roboter. Die sind ebenfalls mit Bilsing-Toolings ausgerüstet. Damit auch in der letzten Station alle Belange einer sicheren Fahrweise umgesetzt werden, sind auch die Robotergreifer mit taktilen Sensoren und einer von der Steuerung überwachten Codierung ausgestattet.
„Auf dem Weg zur Palettierstation richtet eine Zentrierstation die Fertigteile so aus, dass sie die folgenden, geteilten Förderstrecken präzise erreichen. Dabei leiten die Förderstrecken die jeweils ersten Doppelteile bis unter die beiden hinteren Roboter. Wenn unter jedem der vier Roboter ein Fertigteil liegt, drücken zwei Hebebalken, einer unter den vorderen und einer unter den hinteren Robotern, die werkstückspezifischen Heber, nach oben“, erläutert Bilsing.
Dabei würden die jeweils nebeneinander liegenden Fertigteile ein letztes Mal exakt positioniert. Jetzt greifen laut Bilsing die Roboterhände zu, heben die Fertigteile an, schwenken sie um 90 zur Seite und legen sie präzise in die Spezialpaletten ein. In dieser Zeit seien bereits die nächsten Fertigteile auf dem Weg zu den Hebestationen. Die gefüllten Spezialpaletten werden automatisch nach vorne gefördert und von Staplern übernommen.
Wechsel der Roboterhände ebenfalls automatisiert
Nach dem Prinzip des manuellen Bestückens der Saugerbalken mit den jeweils richtigen Greiferwerkzeugen und dem automatisierten Wechsel der Saugerbalken parallel zum Wechsel der Pressenwerkzeuge, erfolgt auch der Wechsel der Roboterhände, der ebenfalls parallel zum Wechsel der Pressenwerkzeuge erfolgt. Nur ist es an der Palettierstation ein wenig komplizierter: Bei einem Produktwechsel benötigen andere Fertigteile auch andere, passende Heber. Dazu setzen die Roboter die bis dahin genutzten Greifer in ihre zugeordnete Haltevorrichtung.
Neben jeder Haltevorrichtung befindet sich ein Klammergreifer, mit passender Automatikkupplung, so dass jeder Roboter schnell seinen Klammergreifer ankuppeln kann. Mit diesem Klammergreifer tauscht der Roboter die Heber aus. Er legt danach den Klammergreifer wieder ab und nimmt den neuen Greifer aus einer weiteren Haltevorrichtung auf.
Dieser Wechsel dauert nur wenige Minuten und fügt sich gut in den automatischen Wechsel der Pressenwerkzeuge ein. Selbst ein Produktwechsel mehrmals am Tage ist unter diesen Aspekten vollkommen unproblematisch.
Media Contact
Weitere Informationen:
http://www.maschinenmarkt.vogel.de/themenkanaele/produktion/umformtechnik/articles/124436/Alle Nachrichten aus der Kategorie: Maschinenbau
Der Maschinenbau ist einer der führenden Industriezweige Deutschlands. Im Maschinenbau haben sich inzwischen eigenständige Studiengänge wie Produktion und Logistik, Verfahrenstechnik, Fahrzeugtechnik, Fertigungstechnik, Luft- und Raumfahrttechnik und andere etabliert.
Der innovations-report bietet Ihnen interessante Berichte und Artikel, unter anderem zu den Teilbereichen: Automatisierungstechnik, Bewegungstechnik, Antriebstechnik, Energietechnik, Fördertechnik, Kunststofftechnik, Leichtbau, Lagertechnik, Messtechnik, Werkzeugmaschinen, Regelungs- und Steuertechnik.
Neueste Beiträge
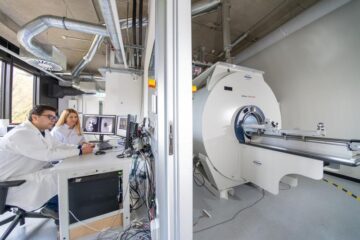
Diamantstaub leuchtet hell in Magnetresonanztomographie
Mögliche Alternative zum weit verbreiteten Kontrastmittel Gadolinium. Eine unerwartete Entdeckung machte eine Wissenschaftlerin des Max-Planck-Instituts für Intelligente Systeme in Stuttgart: Nanometerkleine Diamantpartikel, die eigentlich für einen ganz anderen Zweck bestimmt…
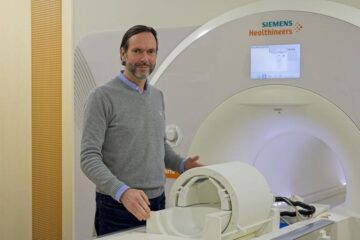
Neue Spule für 7-Tesla MRT | Kopf und Hals gleichzeitig darstellen
Die Magnetresonanztomographie (MRT) ermöglicht detaillierte Einblicke in den Körper. Vor allem die Ultrahochfeld-Bildgebung mit Magnetfeldstärken von 7 Tesla und höher macht feinste anatomische Strukturen und funktionelle Prozesse sichtbar. Doch alleine…
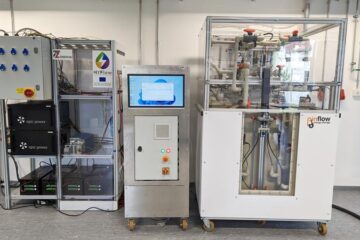
Hybrid-Energiespeichersystem für moderne Energienetze
Projekt HyFlow: Leistungsfähiges, nachhaltiges und kostengünstiges Hybrid-Energiespeichersystem für moderne Energienetze. In drei Jahren Forschungsarbeit hat das Konsortium des EU-Projekts HyFlow ein extrem leistungsfähiges, nachhaltiges und kostengünstiges Hybrid-Energiespeichersystem entwickelt, das einen…