Die Montage von Wendelstein 7-X hat begonnen

Der erste Montage-Schritt für die Fusionsanlage Wendelstein 7-X in Greifswald: Eingehängt in ein drehbares Gestell wird die erste von 50 Stellarator-Magnetspulen auf ein Segment des Plasmagefäßes gefädelt.
Nach Jahren der Rechnung, Vorbereitung und Komponentenfertigung tritt das Projekt Wendelstein 7-X jetzt in eine neue Phase: Im Teilinstitut Greifswald des Max-Planck-Institut für Plasmaphysik (IPP) hat die Montage der Fusionsanlage begonnen. Noch während die industrielle Fertigung läuft, startete mit dem Auffädeln der ersten Magnetspule auf das Plasmagefäß der Zusammenbau des Großexperiments. Rund sechs Jahre wird der Aufbau der komplexen Anlage dauern.
Ziel der Fusionsforschung ist es, ähnlich wie die Sonne aus der Verschmelzung von Atomkernen Energie zu gewinnen. Um das Fusionsfeuer zu zünden, muss in einem späteren Kraftwerk der Brennstoff, ein Wasserstoffplasma, in Magnetfeldern eingeschlossen und auf Temperaturen über 100 Millionen Grad aufgeheizt werden. Wendelstein 7-X, die nach der Fertigstellung weltweit größte Fusionsanlage vom Typ Stellarator, hat die Aufgabe, die Kraftwerkseignung dieses Bautyps zu untersuchen. Mit bis zu 30 Minuten langen Entladungen soll sie seine wesentliche Eigenschaft vorführen, die Fähigkeit zum Dauerbetrieb.
Die Bauteile
Ein Kranz von 50 supraleitenden, etwa 3,5 Meter hohen Magnetspulen ist das Kernstück der Anlage. Mit flüssigem Helium auf Supraleitungstemperatur nahe dem absoluten Nullpunkt abgekühlt, verbrauchen sie nach dem Einschalten kaum Energie. Ihre bizarren Formen sind das Ergebnis ausgefeilter Optimierungsrechnungen: Sie sollen einen besonders stabilen und wärmeisolierenden magnetischen Käfig für das Plasma erzeugen. Um das Magnetfeld verändern zu können, wird den Stellarator-Spulen ein zweiter Satz von 20 flachen, ebenfalls supraleitenden Spulen überlagert. Eine massive ringförmige Stützstruktur hält die Spulen trotz der hohen Magnetkräfte exakt in Position.
Den gesamten Spulenkranz umschließt eine wärmeisolierende Außenhülle von 16 Metern Durchmesser, der Kryostat. Eine Kälteanlage stellt später 5000 Watt Heliumkälte bereit, um die Magnete und ihre Abstützung, d.h. insgesamt 425 Tonnen Material, auf Supraleitungstemperatur zu kühlen. Im Inneren des Spulenkranzes liegt das in 20 Teilen gefertigte Plasmagefäß, das in seiner eigenwilligen Form dem verwundenen Plasmaschlauch angepasst ist. Durch seine insgesamt 299 Löcher soll das Plasma später beobachtet und geheizt werden. Ebenso viele Stutzen, die gut wärmeisoliert zwischen den Spulen hindurchgeführt werden, verbinden diese Öffnungen mit der Außenwand des Kryostaten. Die ganze Anlage ist aus fünf nahezu baugleichen Modulen aufgebaut, die vormontiert und erst in der Experimentierhalle kreisförmig zusammengesetzt werden.
Die Montage
Anfang April hat mit dem Zusammenbau der ersten Modulhälfte die Montage begonnen: In den Vormontagestand 1b wurde dazu das erste Teil des Plasmagefäßes hinein gehoben und die erste, sechs Tonnen schwere Magnetspule mit einem drehbaren Spezialgreifer vorsichtig über die nur Millimeter breiten Zwischenräume auf das Gefäßsegment gefädelt. Erst jetzt kann man den zweiten Sektor des Plasmagefäßes anschweißen und die Wärmeisolation an der Nahtstelle vervollständigen. Diese Superisolation trennt die tiefkalten Magnetspulen von ihrer warmen Umgebung: Sie besteht aus passgenau gefertigten glasfaserverstärkten Kunststoff-Paneelen, in die zur besseren Wärmeleitung Kupfernetze einlaminiert sind. In die Paneele eingelegt sind mehrere Lagen geknitterter, mit Aluminium beschichteter Kunststoff-Folie mit Zwischenlagen aus Glasseide. Nach Fertigstellung der Isolation werden vier weitere Stellaratorspulen und zwei der Zusatzspulen von vorne und hinten auf das Gefäßstück gefädelt und auf eigenen Montage-Stützen geometrisch exakt ausgerichtet. Schließlich wird ein Segment des Tragrings gegen die Spulen geschoben und verschraubt. Nach vielen weiteren Zusatzarbeiten und zahlreichen Kontrollvermessungen ist dann das erste Halbmodul fertig.
Das 50 Tonnen schwere Bauteil wird nun in einem speziellen Lastgeschirr in den zweiten Montagestand gehoben. Das zweite – spiegelsymmetrisch aufgebaute – Halbmodul, das in der Zwischenzeit im Montagestand 1a zusammengebaut wurde, wird gegenüber platziert und beide werden hydraulisch zusammengefahren. Die beiden Segmente des Tragrings beiden werden zueinander ausgerichtet und verschraubt, die Plasmagefäß-Teile verschweißt. Zugleich wird die thermische Isolation an der Nahtstelle geschlossen: Mit einer Masse von 100 Tonnen ist das erste von fünf Modulen im Rohbau fertig.
Nun werden die Leiter für die elektrische Verschaltung der Spulen angebaut – ein recht schwieriger Arbeitsgang. Die steifen, bis zu 14 Meter langen Supraleiter, die vom Forschungszentrum Jülich hergestellt werden, sind bereits in die richtige Form gebogen. 24 Stück der unhandlichen, aber empfindlichen Leiter werden pro Modul gebraucht. Nach dem elektrischen Verbinden und Verschweißen der Supraleiter werden die Verbindungsstellen hochspannungsfest isoliert und ihre Heliumdichtigkeit kontrolliert. Es folgt die Verrohrung für die Helium-Kühlung der Spulen. Alles ist auf Leckdichtigkeit hin zu prüfen. Sind nun noch Sensoren und Messkabel verlegt, dann kann – gemäß Planung nach insgesamt 28 Wochen Bauzeit – das erste Modul den Montagestand verlassen.
In der Experimenthalle
Mit einem speziellen Fahrgestell in die Experimentierhalle transportiert, wird das Modul auf dem dortigen Montagestand in die Unterschale des Außengefäßes hinein gehoben; Verbindungen und Stützen werden angebracht. Das 120 Tonnen-Bauteil wird nun auf das eigentliche Maschinenfundament gehoben und zusätzlich auf Hilfsstützen abgestellt. Die Oberschale des Außengefäßes wird aufgesetzt und verschweißt. 60 Stutzen, die Plasma- und Außengefäß durch den kalten Spulenbereich hindurch verbinden, sind nun samt ihrer Thermoisolation einzubauen.
Es folgen die Inneneinbauten im Plasmagefäß, insbesondere die zahlreichen Teile des Divertors. Mit seinen wassergekühlten Prallplatten werden später die Verunreinigungen und ein Teil der Wärmeenergie aus dem Plasma abgeführt. Den Rest der Energie fängt der Wandschutz ab, Stahlpaneele bzw. ein mit Graphit-Ziegeln armiertes Hitzeschild. Die fünffache Symmetrie der Anlage wiederholt sich im Divertor: Die zwei mal fünf Divertoren bestehen aus Prall- und Führungsplatten, Regelspule und Kryopumpe sowie den zugehörigen Rohrleitungen. Ein Großteil der Komponenten – darunter Pumpen, Hitzeschild und Divertormodule – entsteht zur Zeit in den Zentralen Technischen Einrichtungen des IPP in Garching; die Prallplatten, Regelspulen und Stahlpaneele werden von Industriebetrieben hergestellt. Auch die Abnahmeprüfungen laufen in Garching: Geprüft wird die Leck- und Ausgasrate der Komponenten bzw. die Belastbarkeit der Divertorteile bei hohen Wärmeflüssen.
Bis alle fünf Module in der Experimentierhalle stehen, sind die bisherigen Arbeitsschritte fünfmal zu durchlaufen. Schließlich müssen die fünf Großkomponenten verbunden werden: Die Nahtstellen von Plasma- und Außengefäß sind zu schließen, die Magnete an Strom- und Heliumversorgung anzuschließen. Es folgen die Hauptstromverbindungen, Kühlverrohrungen und immer wieder Kontrollvermessungen und Dichtigkeitsprüfungen: Die Basismaschine ist nun fertig.
Die Vorbereitung
Diesen Ablauf minuziös vorzubereiten, war die Mammutaufgabe der Abteilungen „Montagetechnologie“ und „Montagesteuerung“: Zunächst mussten die Verfahren gefunden werden, mit denen die schweren, bizarr geformten Bauteile über enge Zwischenräume hinweg präzise zusammenzufügen sind – einschließlich der aufwändigen Entwicklung zahlreicher Spezialwerkzeuge wie der steuerbare Spulengreifer oder die Montagestände. Die gesamte Arbeitsfolge der komplexen Montage musste sodann in Einzelschritte zerlegt werden. Insgesamt 450 einzelne Arbeitspakete von der Komponentenvorbereitung bis zur fertigen Maschine wurden festgelegt, detailliert in Arbeitsvorschriften zerlegt, dokumentiert und wo nötig durch Tests untermauert. Die mit der Qualitätssicherung betrauten Ingenieure haben anschließend jeden Schritt geprüft. Dr. Lutz Wegener, der Leiter der Montage: „Die Herausforderung dabei ist, jede Teilaufgabe einfach nachvollziehbar darzulegen. Auch externe Mechaniker müssen nämlich die Arbeitsschritte leicht verstehen, damit wir die Arbeitskapazität dem Bedarf entsprechend schnell variieren können.“ Um möglichst wirtschaftlich arbeiten zu können, müssen nämlich für den Aufbau viele Zeitkräfte eingesetzt werden: bis zu 60 Externe werden das 15-köpfige Montageteam des IPP unterstützen.
Parallel zur Errichtung der Basismaschine wird das Mikrowellen-System zum Aufheizen des Plasmas aufgebaut, die Versorgungseinrichtungen für elektrische Energie und Kühlung, die Maschinensteuerung und schließlich die Messgeräte, die das Verhalten des Plasmas diagnostizieren sollen. Dr. Wegener: „Wenn die Zulieferung durch die Industrie termingerecht läuft und unsere Montageplanung richtig war, dann sollte Wendelstein 7-X in rund sechs Jahren in Betrieb gehen können“.
Media Contact
Weitere Informationen:
http://www.ipp.mpg.deAlle Nachrichten aus der Kategorie: Energie und Elektrotechnik
Dieser Fachbereich umfasst die Erzeugung, Übertragung und Umformung von Energie, die Effizienz von Energieerzeugung, Energieumwandlung, Energietransport und letztlich die Energienutzung.
Der innovations-report bietet Ihnen hierzu interessante Berichte und Artikel, unter anderem zu den Teilbereichen: Windenergie, Brennstoffzellen, Sonnenenergie, Erdwärme, Erdöl, Gas, Atomtechnik, Alternative Energie, Energieeinsparung, Fusionstechnologie, Wasserstofftechnik und Supraleittechnik.
Neueste Beiträge
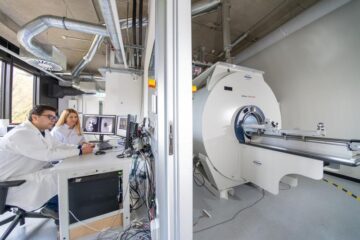
Diamantstaub leuchtet hell in Magnetresonanztomographie
Mögliche Alternative zum weit verbreiteten Kontrastmittel Gadolinium. Eine unerwartete Entdeckung machte eine Wissenschaftlerin des Max-Planck-Instituts für Intelligente Systeme in Stuttgart: Nanometerkleine Diamantpartikel, die eigentlich für einen ganz anderen Zweck bestimmt…
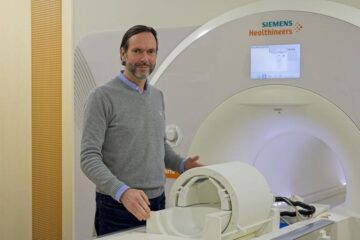
Neue Spule für 7-Tesla MRT | Kopf und Hals gleichzeitig darstellen
Die Magnetresonanztomographie (MRT) ermöglicht detaillierte Einblicke in den Körper. Vor allem die Ultrahochfeld-Bildgebung mit Magnetfeldstärken von 7 Tesla und höher macht feinste anatomische Strukturen und funktionelle Prozesse sichtbar. Doch alleine…
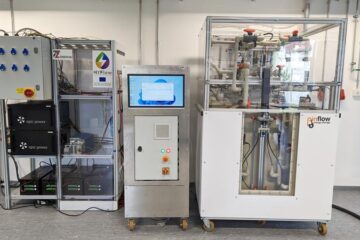
Hybrid-Energiespeichersystem für moderne Energienetze
Projekt HyFlow: Leistungsfähiges, nachhaltiges und kostengünstiges Hybrid-Energiespeichersystem für moderne Energienetze. In drei Jahren Forschungsarbeit hat das Konsortium des EU-Projekts HyFlow ein extrem leistungsfähiges, nachhaltiges und kostengünstiges Hybrid-Energiespeichersystem entwickelt, das einen…