Neue Werkstoffe für Luftfahrt und Automobilbau – leichter, schneller, sicherer und kostengünstiger
Das neue Verbundfasertechnikum der Uni Stuttgart zählt zu den weltweit modernsten Anlagen
Faserverbundwerkstoffe sind bis zu 25 Prozent leichter als Aluminium und 60 Prozent leichter als vergleichbare Stahlstrukturen: sie machen Großflugzeuge wie den neuen Airbus A 380 leichter, schneller, sicherer, ökologisch verträglicher und kostengünstiger – und werden zunehmend auch für die Automobilindustrie interessant. Der Trick bei diesen modernen Verbundwerkstoffen aus hochfesten Kohlefasern ist, alte Textiltechniken wie Nähen, Flechten oder Stricken mit neuen Entwicklungen wie Harzinjek-tionstechniken oder Mikrowellenhärtung zu kombinieren. Auf diese Weise kommen die beiden Disziplinen Flugzeugbau und Textiltechnik zusammen, die auf den ersten Blick nur wenig Berührungspunkte haben. Nun gilt es, die neuen Techniken für die Serienfertigung zu optimieren. Neben der Weiterentwicklung der Forschung ist dies eine der Aufgaben des neuen Faserverbundtechnikums, das in Zusammenarbeit des Instituts für Flugzeugbau der Universität Stuttgart mit mittelständischen Firmen entstanden ist. „Das Technikum zählt zu den weltweit modernsten Anlagen dieser Art“, betonte Prof. Klaus Drechsler, Direktor des Instituts für Flugzeugbau, am 7. Oktober bei der Vorstellung der neuen Einrichtung im Verfügungsgebäude auf dem Uni-Campus in Vaihingen. „Das mit einer NC-Nähanlage, einer neuartigen Flechtmaschine, einem Nähroboter und einer Mikrowelleninjektions- und -härtungsanlage ausgestattete Technikum bietet eine exzellente Grundlage für die Lehre, die Forschung und für die Einwerbung von Drittmittelprojekten“, hob Prof. Drechsler hervor. Bereits vor dem offiziellen Start sind von der Europäischen Union und dem Bundesforschungsministerium finanzierte Projekte angelaufen. Neben der Weiterentwicklung der Technologien in enger Zusammenarbeit mit Textilmaschinen- und Textilwarenherstellern, Endanwendern und Forschungsinstituten legt Prof. Drechsler großen Wert darauf, die Grundlagen dem Ingenieurnachwuchs in der Lehre zu vermitteln.
Vom Segler „Phönix“ bis zum Airbus
Faserverstärkte Kunststoffe haben in den letzten 40 Jahren immer mehr Anwendungsfelder im Flugzeugbau gefunden. Schon 1958 bauten Ingenieure der damaligen Technischen Hochschule Stuttgart mit dem „Phönix“ das erste Segelflugzeug aus glasfaserverstärktem Kunststoff und gehörten damit zu den Pionieren auf diesem Gebiet. Heute bestehen fast alle Hochleistungssegelflugzeuge aus faserverstärkten Kunststoffen und Deutschland hat sich zur führenden Nation im Segelflugzeugbau entwickelt.
Im Verkehrsflugzeugbau haben Airbus und Eurocopter eine Vorreiterrolle der neuen Technologie übernommen: 1980 flog mit der A 300 das erste Großraumflugzeug mit einem kohlefaserverstärkten Leitwerk und 2005 soll der A 380 abheben. Das hintere Ende der Kabine dieses „Riesen der Lüfte“ mit 73 Metern Länge und 80 Metern Spannweite, die Druckkalotte mit über sechs Metern Durchmesser, auf der beim Flug der gesamte Innendruck lastet, besteht aus einem mit modernen Nähverfahren hergestellten Faserverbundwerkstoff. Eingesetzt werden diese modernen Werkstoffe nicht nur im Flugzeugbau, sondern auch für zahlreiche Sportartikel sowie zunehmend auch im Automobilbau.
Von parallelen Fasern bis zu mehrdimensionalen Geweben
Basis der modernen Hochleistungswerkstoffe ist die so genannte Prepreg-Technologie, bei der Verstärkungsfasern parallel angeordnet und bis zur gewünschten Stärke aufeinander geschichtet wurden. Die Integration in die entsprechenden Bauteile und die weitere Verarbeitung waren aufwändig, teuer und zu großen Teilen Handarbeit. Bei der am Institut für Flugzeugbau mit entwickelten Technik werden nun mit Hilfe von Textiltechniken wie Nähen, Weben, Flechten und Sticken automatisiert mehrdimensional belastbare Gewebe hergestellt, die im Bauteil zu einer höheren Strukturintegrität, besserer Schadenstoleranz und höherem Energieaufnahmevermögen im Crashfall führen. Die trockenen Faserstrukturen werden anschließend mit verschiedenen Injektionsverfahren, beispielsweise mit Expoxidharz, imprägniert. Sehr gute Erfahrungen haben die Stuttgarter Wissenschaftler mit einem Verfahren gemacht, bei dem der textile „Vorformling“ auf eine Werkzeugschale aufgelegt und mit einer Vakuumfolie das Harz verteilt und ausgehärtet wird. Eine halb durchlässige Membran sorgt dafür, dass die Luft großflächig entweichen und die Harzmenge genau kontrolliert werden kann. Und bereits bei der Fertigung können Sensoren integriert werden, die den Werkstoff beim Einsatz auf Schäden oder Ermüdung kontrollieren.
Fragen zum Recycling und Reparaturkonzept im Automobilbau
Vor dem Einsatz dieser neuen Werkstoffsysteme und Fertigungsverfahren im Flugzeugbau müssen aufwändige und langwierige Prozesse durchlaufen werden von Prüfprogrammen zur Qualifizierung, Abläufen zur Zulassung oder Berechnungen zur Bauteilauslegung. Insofern erstaunt es nicht, dass bis zur Serienfertigung textilverstärkter Verbundwerkstoffe rund 20 Jahre vergingen. Beim Hubschrauberbau werden solche Werkstoffe erstmals für den Rumpfspant des Transporthubschraubers NH 90 eingesetzt. Das Automatisierungspotential und die hohe Strukturintegrität dieser Verbundwerkstoffe sind auch die Schlüssel für die Nutzung im Automobilbau. Vor der Großserienfertigung müssen jedoch noch Fragen zum Recycling und zum Reparaturkonzept geklärt werden. In jedem Fall können Fertigungszeiten deutlich verkürzt und Kosten reduziert werden. Mercedes hat das Potential der Textiltechnik vom Automatisierungsgrad bis zur Energieabsorption bereits mit den Crashelementen des Supersportwagens SLR aufgezeigt.
Fachkolloquium
Bei einem Fachkolloquium aus Anlass der Einweihung am Freitag, den 8. Oktober, geben Fachleute aus Industrie und Wissenschaft Einblick in aktuelle Arbeiten. Unter anderem wird Dr. Jürgen Brandt von der EADS Forschung in Ottobrunn über „Zwanzig Jahre Textiltechnik für Faserverbundwerkstoffe“ berichten, Dr. Christian Weimer von Eurocopter „Textile Faserverbundwerkstoffe im Hubschrauberbau“ und Dr. Thomas Bischoff von der Saertex Stade GmbH „Die genähte Druckkalotte des Airbus A 380“ vorstellen. Anschließend informieren Mitarbeiter der Volkswagen AG über „Leichtbaupotentiale mit Faser-Kunststoff-Verbunden im Automobilbau“. Weitere Themen betreffen Technologien für den Airbus der Zukunft oder Informationen zur Entwicklung textiler Verbundwerkstoffe in den USA. Angemeldet haben sich rund 150 Teilnehmer aus Deutschland, Österreich, der Schweiz, Belgien und den Niederlanden. Vertreten sind, neben der Luft- und Raumfahrtindustrie, fast alle deutschen Automobilfirmen, mittelständische Unternehmen aus dem Textilmaschinen- und Zuliefererbereich sowie Forschungsinstitute und -ministerien. Das Kolloquium findet von 9.30 Uhr bis ca. 15.00 Uhr im Hörsaal 57.02 (Vaihingen, Pfaffenwaldring 57) statt. Ab 15.15 Uhr können die Gäste das neue Technikum und die Anlagen in Augenschein nehmen.
Weitere Informationen am Institut für Flugzeugbau, Tel. 0711/685-2402, Fax 0711/685-2429, e-mail: drechsler@ifb.uni-stuttgart.de sowie unter www.ifb.uni-stuttgart.de.
Media Contact
Weitere Informationen:
http://www.ifb.uni-stuttgart.deAlle Nachrichten aus der Kategorie: Automotive
Die wissenschaftliche Automobilforschung untersucht Bereiche des Automobilbaues inklusive Kfz-Teile und -Zubehör als auch die Umweltrelevanz und Sicherheit der Produkte und Produktionsanlagen sowie Produktionsprozesse.
Der innovations-report bietet Ihnen hierzu interessante Berichte und Artikel, unter anderem zu den Teilbereichen: Automobil-Brennstoffzellen, Hybridtechnik, energiesparende Automobile, Russpartikelfilter, Motortechnik, Bremstechnik, Fahrsicherheit und Assistenzsysteme.
Neueste Beiträge
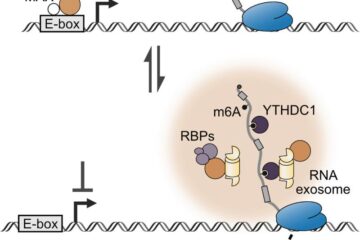
Forschende enthüllen neue Funktion von Onkoproteinen
Forschende der Uni Würzburg haben herausgefunden: Das Onkoprotein MYCN lässt Krebszellen nicht nur stärker wachsen, sondern macht sie auch resistenter gegen Medikamente. Für die Entwicklung neuer Therapien ist das ein…

Mit Kleinsatelliten den Asteroiden Apophis erforschen
In fünf Jahren fliegt ein größerer Asteroid sehr nah an der Erde vorbei – eine einmalige Chance, ihn zu erforschen. An der Uni Würzburg werden Konzepte für eine nationale Kleinsatellitenmission…
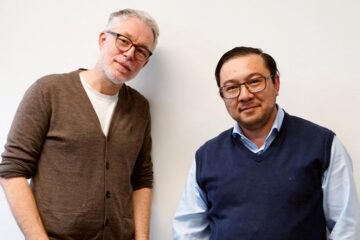
Zellskelett-Gene regulieren Vernetzung im Säugerhirn
Marburger Forschungsteam beleuchtet, wie Nervenzellen Netzwerke bilden. Ein Molekülpaar zu trennen, hat Auswirkungen auf das Networking im Hirn: So lässt sich zusammenfassen, was eine Marburger Forschungsgruppe jetzt über die Vernetzung…