Laserverfahren für funktionsintegrierte Composites
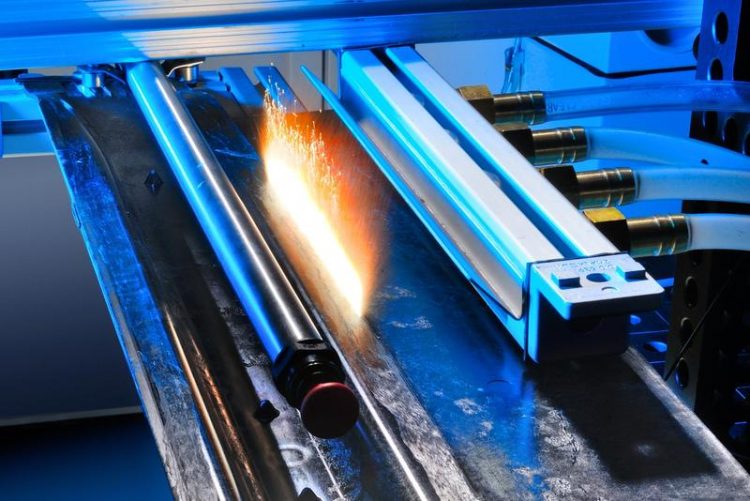
Besäumen eines PKW-Dachspriegels aus glas- und carbonfaserverstärktem Kunststoff. Fraunhofer ILT, Aachen
Experten des Fraunhofer ILT erforschen und entwickeln Laserprozesse für das wirtschaftliche Fügen, Schneiden, Abtragen oder Bohren von Verbundmaterialien – insbesondere vor dem Hintergrund der Integration in bestehende Prozessketten.
Dr. Alexander Olowinsky, Gruppenleiter Mikrofügen am Fraunhofer ILT: »Mechanische Verfahren in der Trenntechnik wie das Fräsen, Sägen oder das Wasserstrahlschneiden sowie das Kleben beim Fügen von Werkstoffen lassen sich durch Laserprozesse ersetzen, wobei diese die Effizienz und Qualität der Verfahren deutlich steigern können.«
Mikrostrukturierung von Magnesium für Ultraleichtanwendungen
Kunststoffe und Metalle bieten jeweils spezielle Eigenschaften, etwa bei Formbarkeit, Festigkeit oder Wärmeleitfähigkeit, die durch die Herstellung von Hybridbauteilen kombiniert werden können. Bei Hybridverbindungen müssen die Metalloberflächen zunächst vorbereitet werden. Dabei kommen z. B. die Mikrostrukturierung per cw-Laser oder die Mikro- beziehungsweise Nanostrukturierung mit Ultrakurzpulslaser mit unterschiedlichen Maschinenkonzepten infrage.
Magnesium ist der leichteste metallische Konstruktionswerkstoff und zeichnet sich durch eine besonders hohe Wärmeleitfähigkeit aus. Gemeinsam mit dem Institut für Kunststoffverarbeitung IKV der RWTH Aachen entwickelt das Fraunhofer ILT Laserprozesse zur Mikrostrukturierung von Magnesium, das anschließend sehr stabile und formschlüssige Verbindungen mit verschiedenen thermoplastischen Kunststoffen ermöglicht.
Ein single-mode Faserlaser (mit 1064 nm Wellenlänge) bringt mit Flächenraten von bis zu 1000 mm2 pro Sekunde präzise Hinterschnitte in die Magnesiumoberfläche ein, die sich im späteren Spritzgussverfahren mit Kunststoff ausfüllen lassen. »Mit kurzglasfaserverstärktem Kunststoff haben wir Hybridverbindungen mit hohen Zugscherfestigkeiten bis zu 22,4 MPa realisiert – die Bauteile sind extrem leicht und gleichzeitig hochbelastbar«, erklärt Dipl.-Wirt.-Ing. Christoph Engelmann, Teamleiter Kunststoffbearbeitung am Fraunhofer ILT. Da keine Klebstoffe nötig sind, finden Alterungsprozesse zudem langsamer statt als bei konventionellen geklebten Verbindungen.
Bei der Kunststoffauswahl gibt es viel Spielraum: Grundsätzlich eignen sich alle thermoplastischen Kunststoffe, die im Spritzgussverfahren einsetzbar sind. Sie eröffnen vielfältige Möglichkeiten zur Bauteilanbindung und zur Integration von Funktionalitäten, welche die hergestellten Hybridbauteile später bieten und welche in reiner Metallbauweise nicht erzeugt werden können.
Materialschonende Trennverfahren für Composites
Beim Laserstrahlschneiden von Faserverbundmaterialien, insbesondere carbonfaserverstärkten Kunststoffen, zielt die Prozessauslegung auf eine möglichst kleine Wärmeeinflusszone. Gleichzeitig soll eine produktivitätsorientierte, kurze Bearbeitungszeit eingehalten werden. Durch wiederholtes, schnelles Scannen des Laserstrahls entlang der Schneidbahn entsteht ein sukzessiver, schonender Abtrag.
»Durch ein kontinuierliches Nachführen des Scanfeldes ist dieses Verfahren auch für große Bauteile anwendbar«, erläutert Dr. Frank Schneider, Projektleiter Makrofügen und Schneiden am Fraunhofer ILT.
Laserleistung, Scangeschwindigkeit und die Abkühlzeit zwischen den Scans beeinflussen dabei die Wärmeeinflusszone und die Bearbeitungszeit. Die Wissenschaftler optimieren diese Parameter und ermitteln so die materialabhängig besten Einstellungen, die bei hybriden, aus einem Materialmix bestehenden Teilen auch innerhalb eines Bauteils adaptiert werden können.
Selbst wenn so unterschiedliche Werkstoffe wie glasfaser- und kohlefaserverstärkte Kunststoffe getrennt werden sollen, die in übereinanderliegenden Schichten angeordnet sind, lässt sich ein Schnitt in nur einem Bearbeitungsschritt ausführen – präzise, ohne Verschleiß an Werkzeugen und dank der Verfügbarkeit von cw-Hochleistungslasern mit hoher Strahlqualität auch effizient.
Laserbohren für produktive CFK-Bauteilfertigung
Im Leichtbaubereich wird die Integration von Funktionselementen in CFK-Strukturbauteilen häufig über eingesetzte Gewindehülsen (Inserts) durchgeführt, z. B. in Preforms für Bauteile in der Automobil- und Flugzeugindustrie. Die Inserts werden dazu formschlüssig in typischerweise mechanisch gebohrte Bauteile eingesetzt und anschließen geklebt. Die Qualität und Festigkeit der Fügestelle hängen dabei maßgeblich von der Fehlerfreiheit des gebohrten Laminates und der Klebung ab.
Besonders haltbare und hochqualitative Verbindungen entstehen, wenn das noch ungetränkte Carbonfasertextil mittels ultrakurz gepulster (UKP) Laserstrahlung gebohrt wird, in das anschließend Funktionselemente formschlüssig eingesetzt werden.
Laserscanner ermöglichen auch anspruchsvolle Bohrkonturen wie sternförmige Formbohrungen und damit die Integration von belastungsangepassten Einlegeteilen. Im späteren Infusionsprozess dient die Matrix als Klebstoff zwischen den Carbonfasern und dem Insert, wodurch kein weiterer Klebstoff erforderlich ist.
Durch UKP-Laserstrahlbearbeitung können sowohl Preforms als auch konsolidierte CFK-Bauteile hochqualitativ gebohrt werden. »Durch die primäre Verdampfung des Werkstoffs können thermische oder materialographische Schädigungen im Laminat oder an den Fasern vermieden werden«, erläutert Dr. Stefan Janssen, Teamleiter Laserstrahlbohren und Präzisionstrennen am Fraunhofer ILT. Die Prozesszeiten von typischerweise wenigen Sekunden bis zu einer Minute und die hohe Automatisierbarkeit unterstützen zudem einen produktiven Einsatz in der CFK-Bauteilfertigung.
Das Fraunhofer ILT auf der JEC World 2019
Mehr zur Laserbearbeitung von Composites erfahren Besucher auf der JEC World vom 12. bis zum 14. März 2019 in Paris. Experten des Fraunhofer ILT präsentieren Details und neue Entwicklungen auf dem AZL-Gemeinschaftsstand, Halle 5A/D17.
Dipl.-Wirt.-Ing. Christoph Engelmann
Gruppe Mikrofügen
Telefon +49 241 8906-217
christoph.engelmann@ilt.fraunhofer.de
Dr.-Ing. Frank Schneider
Gruppe Makrofügen und Schneiden
Telefon +49 241 8906-426
frank.schneider@ilt.fraunhofer.de
Dr.-Ing. Stefan Janssen
Gruppe Mikro- und Nanostrukturierung
Telefon +49 241 8906-8076
stefan.janssen@ilt.fraunhofer.de
http://www.ilt.fraunhofer.de
http://www.ilt.fraunhofer.de/de/messen-und-veranstaltungen/messen/jec-world-comp…
Media Contact
Alle Nachrichten aus der Kategorie: Verfahrenstechnologie
Dieses Fachgebiet umfasst wissenschaftliche Verfahren zur Änderung von Stoffeigenschaften (Zerkleinern, Kühlen, etc.), Stoffzusammensetzungen (Filtration, Destillation, etc.) und Stoffarten (Oxidation, Hydrierung, etc.).
Unter anderem finden Sie Wissenswertes aus den Teilbereichen: Trenntechnologie, Lasertechnologie, Messtechnik, Robotertechnik, Prüftechnik, Beschichtungsverfahren und Analyseverfahren.
Neueste Beiträge

Aufbruchstimmung in der Alzheimer-Forschung
Bei der Alzheimer Erkrankung lagern sich Eiweiße im Gehirn ab und schädigen es. Prof. Dr. Susanne Aileen Funke von der Hochschule Coburg hat eine Methode gefunden, die solche gefährlichen Eiweißverbindungen…

Chronische Entzündungen durch Ansätze aus der Natur behandeln
Die interdisziplinäre Forschungsgruppe „nature4HEALTH“ hat jüngst ihre Arbeit aufgenommen. Das Team der Friedrich-Schiller-Universität Jena und des Universitätsklinikums Jena entwickelt ganzheitliche naturstoffbasierte Therapieansätze für die Behandlung chronisch-entzündlicher Erkrankungen. Chronische Entzündungen sind…

Antivirale Beschichtungen und Zellkultur-Oberflächen maßgeschneidert herstellen
Verfahren der Kieler Materialwissenschaft ermöglicht erstmals umfassenden Vergleich von Beschichtungen für biomedizinische Anwendungen. Der Halteknopf im Bus, die Tasten im Fahrstuhl oder die Schutzscheibe am Anmeldetresen in der Arztpraxis: Täglich…