Modulares Fertigungssystem für Kettenräder

Vom Schüttgut in Form von Sägeabschnitten zum fertigen Kettenrad in weniger als 40 Sekunden, so sieht das neue Fertigungssystem von EMAG aus.
Komplettlösungen sind heute mehr gefragt denn je. Wurden vor einigen Jahren noch Fertigungsschritte in Teilprozesse zerlegt und Fertigungslinien mit verschiedenen Werkzeugmaschinenherstellern realisiert, werden heute praktisch nur noch Komplettlösungen verlangt.
Hier kann sich glücklich schätzen, wer über eine breite technologische Basis verfügt, um die geforderten Fertigungslösungen aus eigenen Kräften stemmen zu können. Einer dieser Hersteller, der sich auf die Abbildung der kompletten Prozesskette spezialisiert hat, ist das Unternehmen EMAG.
Niemand beherrscht das Zerlegen von komplexen Fertigungsprozessen in einfach zu handhabende Teilprozesse so gut, wie das Unternehmen aus Salach. Ein Grund hierfür sind die modularen Maschinen von EMAG, die den Aufbau von Fertigungslinien quasi nach dem Baukastensystem ermöglichen, wie die neue Fertigungslinie für Kettenräder eindrucksvoll beweist.
Kettenräder sind Teil eines jeden modernen Motors und müssen in millionenfacher Ausfertigung bei gleichzeitig höchster Qualität gefertigt werden. Diese Präzision ist notwendig, um den Verschleiß der Teile so minimal wie möglich zu halten, schließlich hängen essentielle Bauteile, wie z.B. Nockenwellen, von deren Funktion ab. Das eine hohe Produktivität eine hohe Qualität nicht ausschließt, zeit EMAG mit dem Fertigungssystem für Kettenräder, das komplett mit modularen Maschinen realisiert wurde.
Modulare Maschinen optimal verkettet
„Wir haben den Bearbeitungsprozess für Kettenräder in vier einfach zu handhabende Teilprozesse zerlegt“, erklärt Björn Svatek, Sales & Marketing Director Modular Solutions bei EMAG. „In OP 10 und OP 20, bearbeiten wir mit der doppelspindligen Vertikaldrehmaschine VL 3 DUO die beiden Seiten des Kettenradrohlings, in OP 30 fräsen wir die Verzahnung auf unserer Wälzfräsmaschine VL 4 H, und schließlich entgraten wir das fertige Kettenrad in OP 40 auf unserer Anfas- und Entgratmaschine VL 2 RC.
Dass wir dabei für den kompletten Arbeitsprozess auf unsere modularen Maschinen aus dem Baukasten der Modular Solutions zurückgreifen können, unterstreicht die hohe Flexibilität und Leistungsfähigkeit dieser Baureihe– und das Ganze noch zu einem überaus fairen Preis“, ergänzt Björn Svatek.
EMAG nutzt neben den modularen Maschinen auch das für diesen Maschinentyp eigens entworfene Automationssystem TrackMotion. „Mit unserem eigenen Automationssystem dem sog. TrackMotion können wir unsere modularen Maschinen sehr einfach und effizient verketten. Über den TransLift, ein Werkstückgreifer, der direkt hinter dem Arbeitsraum auf einem Schienensystem quasi direkt durch die Maschinen fährt, erfolgt der effiziente und direkte Teiletransport zwischen den Maschinen.
Dabei sorgt er sowohl für das Wenden der Teile zwischen den Operationen als auch für die letztendliche Ablage auf sogenannten Stackern – Paletten, auf denen die fertigen Teile aufgestapelt werden. So können wir auf engstem Raum extrem viele Fertigteile unterbringen“, führt Svatek weiter aus. „Kompaktheit und Einfachheit bei gleichzeitig maximaler Produktivität waren unsere Ziele beim Entwurf dieser Fertigungslinie, und die große Zufriedenheit unserer Kunden zeigt uns, dass wir unsere hochgesteckten Ziele erreicht haben.“
Das Fertigungssystem im Detail
Bei der Entwicklung wurde auf eine einfache Handhabung geachtet. Dies beginnt bereits bei der Beladung des Fertigungssystems. Hier kommt ein Vereinzeler zum Einsatz, in den die Rohteile in Form von Sägeabschnitten einfach hineingeschüttet werden. Von hier gelangen die Teile dann auf den integrierten Teilespeicher der doppelspindligen Vertikaldrehmaschine VL 3 DUO. Diese integrierten Teilespeicher sind Teil des Pick-up-Automationssystems, mit dem jede modulare Maschine von EMAG ausgestattet ist. Die modularen Maschinen sind in sich vollständig automatisiert.
Die Arbeitsspindel belädt sich vom integrierten Teilespeicher, verfährt in den Arbeitsraum für die Bearbeitung und legt anschließend das fertig bearbeitete Werkstück wieder auf dem Teilespeicher ab, wo bereits das nächste Teil auf die Bearbeitung wartet. Von hier nimmt das oben erwähnte TrackMotion Automationssystem das Teil auf und legt es auf dem integrierten Teilespeicher der nächsten Maschine ab. Auf diese Weise gibt es fast keine Stillstandzeiten, da der Transport der Teile zwischen den Maschinen parallel zur Bearbeitung abläuft und daher völlig taktzeitneutral ist. Und die Zeit, die die Arbeitsspindel für die Be- und Entladung benötigt, beträgt nur wenige Sekunden.
Hocheffiziente Bearbeitungstechnologien
EMAG hat aber nicht nur bei der Automationstechnologie auf maximale Performance geachtet, auch die eingesetzte Bearbeitungstechnologie trägt zur hohen Produktivität der Fertigungslinie bei.
So kommen in den VL 3 DUO Maschinen leistungsstarke Arbeitsspindeln mit 18 kW und einen Drehmoment von 77 Nm zum Einsatz. In Kombination mit den 12-Fach-Werkzeugrevolvern (wahlweise mit VDI- oder BMT-Schnittstelle), die optional mit angetriebenen Werkzeugen und Y-Achse ausgestattet werden können, ergeben sich ebenso schnelle wie präzise Zerspanungsprozesse – dank Direktantrieb (Torquemotor).
In der vertikalen Wälzfräsmaschine und in der vertikalen Anfas- und Entgratmaschine findet sich bewährte Technik von EMAG KOEPFER, dem Zahnradspezialisten der EMAG Gruppe. Die leistungsstarke Fräseinheit der VL 4 H sorgt für schnelle Vorschübe und steht ihren modularen Geschwistern der Modellfamilie in punkto Produktivität in nichts nach. Für das Einbringen der Fase und das Entgraten des Kettenrads stehen wahlweise das Drückentgraten oder das CHAMFER-CUT-Verfahren zur Verfügung. Welches davon zum Einsatz kommt, hängt von der Werkstückgeometrie und natürlich auch vom Wunsch des Kunden ab.
„Mit diesem Fertigungssystem für Kettenräder zeigen wir als EMAG wieder einmal, wie flexibel und leistungsfähig unsere modulare Produktpalette ist. Mit diesem System produzieren wir Kettenräder in weniger als 40 Sekunden und das unter Einsatz unserer modularen Maschinen. Für Kunden bedeutet dies, dass das Fertigungssystem nicht nur sehr schnell verfügbar, sondern auch im Preis äußerst attraktiv ist“, erklärt Björn Svatek.
„Nie zuvor war es so einfach Fertigungslinien aufzubauen, wie mit unseren Modular Solutions in Kombination mit unserem TrackMotion Automationssystem. Ich bin sicher, wer einmal eine solche Maschine oder eine Linie aus diesen Maschinen im Einsatz gesehen hat, wird begeistert sein. Hier stimmt eben alles, Qualität, Produktivität und Preis.
Kasten: Induktionshärten
Beim Induktionshärten von Kettenrädern auf einer EMAG eldec MIND 750 Härtemaschine liegt der Fokus auf höchster Ausbringung bei konstanter Bauteilqualität. Die Taktzeiten liegen je nach Werkstücktyp zwischen 4 und 8 Sekunden. Das vollautomatisierte System ist dazu mit einem mittaktenden Brausesystem ausgerüstet. Energiequelle ist entweder ein SDF®- oder Hochfrequenz-Generator. Durch die hochgenaue Einbringung der Energie beim Induktionshärten und dem nachfolgenden Anlassen wie auch durch den Abkühlungsprozess erreichen die gesinterten Kettenräder die gewünschte Festigkeit.
Kasten: Hartdrehen & Schleifen von Kettenrädern
Die Qualität der VLC 100 GT wird vor allem an einem konkreten Beispiel deutlich. Betrachtet man die Bearbeitung von Kettenrädern, werden die Vorteile der Kombinationsbearbeitung schnell klar. Nach der automatischen Beladung der Maschine per Pick-up-Spindel erfolgt die erste Bearbeitung mit der integrierten Innenschleifspindel. Die Bohrung des Kettenrads hat wenig Aufmaß und wird mit CBN fertiggeschliffen. Mit den beiden ebenfalls im Arbeitsraum angeordneten Blockstahlhaltern erfolgt die Bearbeitung der Planflächen des Kettenrads. Die Bearbeitung per Hartdrehtechnologie ermöglicht dabei nicht nur sehr kurze Bearbeitungszeiten, sondern erfordert zudem keinerlei Nachbearbeitung. Per Messtaster, der zwischen Arbeitsraum und Beladestation angeordnet ist, wird anschließend die Bearbeitungsqualität des Kettenrads geprüft.
Ansprechpartner Presse und Veröffentlichung
Markus Isgro EMAG GmbH & Co.KG Austraße 24 D-73084 Salach Fon: +49(0)7162/17-4658 Fax: +49(0)7162/17-199 e-mail: misgro@emag.comMedia Contact
Alle Nachrichten aus der Kategorie: Maschinenbau
Der Maschinenbau ist einer der führenden Industriezweige Deutschlands. Im Maschinenbau haben sich inzwischen eigenständige Studiengänge wie Produktion und Logistik, Verfahrenstechnik, Fahrzeugtechnik, Fertigungstechnik, Luft- und Raumfahrttechnik und andere etabliert.
Der innovations-report bietet Ihnen interessante Berichte und Artikel, unter anderem zu den Teilbereichen: Automatisierungstechnik, Bewegungstechnik, Antriebstechnik, Energietechnik, Fördertechnik, Kunststofftechnik, Leichtbau, Lagertechnik, Messtechnik, Werkzeugmaschinen, Regelungs- und Steuertechnik.
Neueste Beiträge
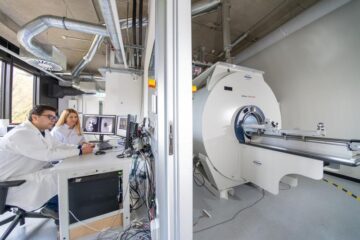
Diamantstaub leuchtet hell in Magnetresonanztomographie
Mögliche Alternative zum weit verbreiteten Kontrastmittel Gadolinium. Eine unerwartete Entdeckung machte eine Wissenschaftlerin des Max-Planck-Instituts für Intelligente Systeme in Stuttgart: Nanometerkleine Diamantpartikel, die eigentlich für einen ganz anderen Zweck bestimmt…
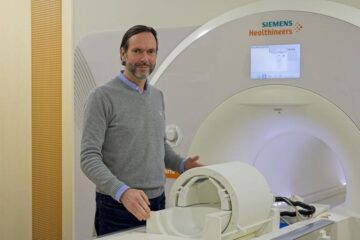
Neue Spule für 7-Tesla MRT | Kopf und Hals gleichzeitig darstellen
Die Magnetresonanztomographie (MRT) ermöglicht detaillierte Einblicke in den Körper. Vor allem die Ultrahochfeld-Bildgebung mit Magnetfeldstärken von 7 Tesla und höher macht feinste anatomische Strukturen und funktionelle Prozesse sichtbar. Doch alleine…
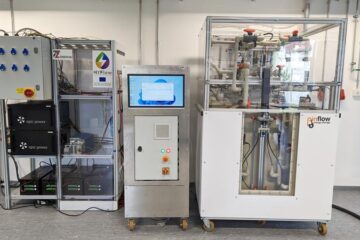
Hybrid-Energiespeichersystem für moderne Energienetze
Projekt HyFlow: Leistungsfähiges, nachhaltiges und kostengünstiges Hybrid-Energiespeichersystem für moderne Energienetze. In drei Jahren Forschungsarbeit hat das Konsortium des EU-Projekts HyFlow ein extrem leistungsfähiges, nachhaltiges und kostengünstiges Hybrid-Energiespeichersystem entwickelt, das einen…