Wenn der Stahl mit der Keramik: RUB-Ingenieur entwickelt neues Verfahren für extrem robuste Beschichtungen
Nur die besten Eigenschaften von Stahl und Keramik kombiniert der Bochumer Maschinenbauer Dr.-Ing. Sebastian Weber in einem neuen Verfahren, um extrem robuste Schichten für Bauteile herzustellen.
„Zäh wie Stahl und hart wie Keramik“ sind die hoch verschleißbeständigen Beschichtungen, hergestellt aus Pulvern im so genannten Sintercladding. Das Ergebnis birgt ein enormes Sparpotenzial, fallen doch in Deutschland jedes Jahr Bauteile im Wert von 60 Milliarden Euro dem Verschleiß zum Opfer. Für seine Entwicklung erhielt Dr. Weber den mit 2.500 Euro dotierten Werkstoff-Innovationspreis 2009 von ThyssenKrupp.
Das Problem: dem Verschleiß standhalten
Ob Walzen, Pressen oder Prägewerkzeuge: Für zahlreiche Anwendungen im Maschinenbau werden Bauteile benötigt, die einer dauerhaften Belastung und dem Verschleiß so lange wie möglich standhalten müssen. Im Idealfall bzw. Modell bearbeitet ein hartes Werkzeug ein weicheres Werkstück oder Mahlgut – zum Beispiel Walzen, die mineralische Güter zerkleinern, oder Prägestempel zur Herstellung von Münzen. In der Praxis ist das bearbeitete Gut häufig nicht so weich – dann prägt die Münze den Stempel und das Mineral schmirgelt die Walze nach und nach dünner.
Vermählt: Stahl und Keramik
Selbst der härteste Stahl hat unter groben Verschleißbedingungen keine lange Lebensdauer. Wesentlich härter sind dagegen Keramiken. Die Lebensdauer einer Keramikwalze könnte weitaus höher liegen – leider „zerplatzt“ dieser Lösungsansatz schon am ersten größeren Gesteinsbrocken. „Denn so hart die Keramik sein mag, sie ist auch außerordentlich spröde“, sagt Sebastian Weber. Zum Einsatz etwa bei der Mineralzerkleinerung kommen daher schon länger Komposite aus Stahl und Keramik in einem aufwändigen und teuren Herstellungsprozess.
Etabliert, aber teuer: HIP
Beim heiß-isostatischen Pressen – HIP oder HIP-Verfahren genannt – vermischen sich ein beliebiges Stahl- und ein genauso beliebig wählbares Keramikpulver. Diese Pulvermischung wird anschließend in eine Kapsel gefüllt, die evakuiert und anschließend zugeschweißt wird. Bei einem Druck von etwa 1000 bar und einer Temperatur von 1150°C entsteht aus den beiden Pulvern ein zu 100 Prozent dichter Werkstoff, ohne dass dabei eine Komponente flüssig ist. Im Gegensatz zum HIP ist das klassische Schmelzen und Gießen von Stahl wesentlich kostengünstiger. Allerdings sind die Kombinationsmöglichkeiten von Keramik und Stahl beim Schmelzen stark eingeschränkt. „Und wie es der Zufall will, lassen sich die besonders verschleißbeständigen Kombinationen nicht durch Schmelzen herstellen“, so Weber.
Die Lösung: Sintern mit Flüssigphase
Am Lehrstuhl für Werkstofftechnik (Inhaber: Prof. Dr.-Ing. Werner Theisen) hat Sebastian Weber nichts dem Zufall überlassen. Die einfache Idee: Auch beim HIP-Verfahren kommt es auf die richtige Mischung an – mit dem Ziel, vom Preis her näher am Schmelzen und von den erzeugten Kompositen her näher an den HIP-Werkstoffen zu liegen. Beim Sintercladding entfällt das isostatische Pressen bei hohem Druck. Da der Druck aber für die Verdichtung des Pulvers sorgt, braucht man einen Ersatz – eine flüssige Phase, indem man die Temperatur von vorher 1150°C auf etwa 1250°C erhöht. Dabei schmilzt ein Teil des Stahlpulvers auf, die Keramik jedoch nicht. Durch die engen Pulverzwischenräume entstehen große Kapillarkräfte, die die flüssige Phase gleichmäßig im Bauteil verteilen. Da die flüssige Phase das Pulvergemisch auch beweglicher macht, reichen die Kapillarkräfte aus, um das Bauteil vollständig zu verdichten. Erwärmt man die Pulvermischung nun gemeinsam mit einem massiven Grundkörper (Substrat), so lassen sich auf einfache Art und Weise dicke, verschleißbeständige Schichten herstellen.
Der Werkstoff-Innovationspreis
ThyssenKrupp ist ein langjähriger Kooperationspartner der Bochumer Fakultät für Maschinenbau. Das Unternehmen gehört zudem federführend dem Industriekonsortium an, das zusammen mit dem Land NRW das Materialforschungszentrum ICAMS der RUB finanziell unterstützt. Seit 2002 verleiht ThyssenKrupp den Werkstoff-Innovationspreis an Forscher der Ruhr-Universität, die in der Erforschung, Entwicklung und Anwendung von Werkstoffen Herausragendes leisten. Der diesjährige Preisträger Dr. Sebastian Weber ist derzeit Mitarbeiter einer gemeinsamen Forschergruppe der RUB und des Helmholtz-Zentrums Berlin. Den Preis erhielt er für seine Dissertation „Gezielte Ausnutzung des Stofftransports zur Herstellung neuartiger PM-Hartverbundwerkstoffe auf Eisenbasis“.
Weitere Informationen
Dr.-Ing. Sebastian Weber, Tel. 0234/32-28229, E-Mail: weber@wtech.rub.de
Redaktion: Jens Wylkop
Media Contact
Weitere Informationen:
http://www.ruhr-uni-bochum.de/Alle Nachrichten aus der Kategorie: Verfahrenstechnologie
Dieses Fachgebiet umfasst wissenschaftliche Verfahren zur Änderung von Stoffeigenschaften (Zerkleinern, Kühlen, etc.), Stoffzusammensetzungen (Filtration, Destillation, etc.) und Stoffarten (Oxidation, Hydrierung, etc.).
Unter anderem finden Sie Wissenswertes aus den Teilbereichen: Trenntechnologie, Lasertechnologie, Messtechnik, Robotertechnik, Prüftechnik, Beschichtungsverfahren und Analyseverfahren.
Neueste Beiträge
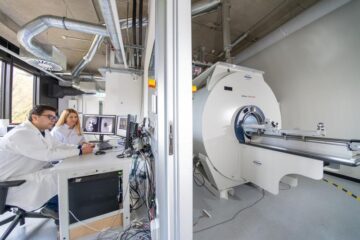
Diamantstaub leuchtet hell in Magnetresonanztomographie
Mögliche Alternative zum weit verbreiteten Kontrastmittel Gadolinium. Eine unerwartete Entdeckung machte eine Wissenschaftlerin des Max-Planck-Instituts für Intelligente Systeme in Stuttgart: Nanometerkleine Diamantpartikel, die eigentlich für einen ganz anderen Zweck bestimmt…
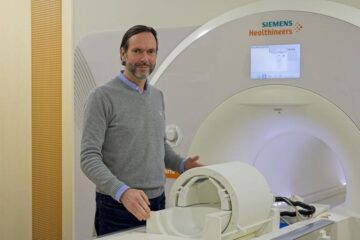
Neue Spule für 7-Tesla MRT | Kopf und Hals gleichzeitig darstellen
Die Magnetresonanztomographie (MRT) ermöglicht detaillierte Einblicke in den Körper. Vor allem die Ultrahochfeld-Bildgebung mit Magnetfeldstärken von 7 Tesla und höher macht feinste anatomische Strukturen und funktionelle Prozesse sichtbar. Doch alleine…
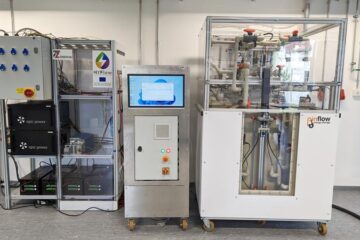
Hybrid-Energiespeichersystem für moderne Energienetze
Projekt HyFlow: Leistungsfähiges, nachhaltiges und kostengünstiges Hybrid-Energiespeichersystem für moderne Energienetze. In drei Jahren Forschungsarbeit hat das Konsortium des EU-Projekts HyFlow ein extrem leistungsfähiges, nachhaltiges und kostengünstiges Hybrid-Energiespeichersystem entwickelt, das einen…