Eine Matrix für Gewebe
Materialwissenschaftler der Universität Würzburg haben dafür erfolgreich neue Fasern mit ganz besonderen Eigenschaften entwickelt.
Die Anforderungen an sie sind hoch: Im menschlichen Körper eingesetzt, müssen sie rückstandslos abbaubar sein – und das nicht zu schnell, aber auch nicht zu langsam. Nur ganz bestimmte Zellen sollen sich auf ihnen ansiedeln, untereinander verbinden und zu komplexen Strukturen heranwachsen. Andere Substanzen hingegen, beispielsweise Proteine und Zellen aus dem Blut, sollen ihnen fern bleiben.
Die Rede ist von extrem dünnen Polymerfäden, die zu Netzen oder dreidimensionalen Strukturen verwoben werden können. Professor Jürgen Groll erforscht solche Materialien, die in der Medizin zum Einsatz kommen sollen. Seit August dieses Jahres leitet er den Lehrstuhl für Funktionswerkstoffe in der Medizin und der Zahnheilkunde der Universität Würzburg. Jetzt hat er eine vielversprechende Neuentwicklung der Öffentlichkeit präsentiert. Die renommierte Fachzeitschrift Nature Materials berichtet darüber in ihrer aktuellen Ausgabe.
Extrem dünne Fäden wachsen im elektrischen Feld
„Es ist uns gelungen, eine Technik zu entwickeln, die solche Fasern in einem einzigen Arbeitsschritt herstellt“, sagt Groll. Ultradünne Polymerfasern zu produzieren: Das war bisher schon möglich. „Electrospinning“ heißt die dahinter steckende Technik. Das Prinzip: An eine Flüssigkeit wird ein elektrisches Feld angelegt, das dünne „Jets“ erzeugt. Die Fasern, die dabei entstehen, sind äußerst dünn – bis zu zehn Nanometern, also dem Hunderttausendstel eines Millimeters.
Groll und seine Mitarbeiter haben diese Technik jetzt einen deutlichen Schritt voran gebracht. Sie haben ein besonderes Makromolekül entwickelt. Gibt man dieses Molekül in die Flüssigkeit, aus der die Fasern hergestellt werden, verändert sich deren Oberfläche radikal. „Dieses Molekül verwandelt die an und für sich wasserabstoßenden Fasern in ‚hydophile‘, also wasseranziehende Fasern“, erklärt Groll. Damit unterdrückt es die Anlagerung unerwünschter Proteine an der Faseroberfläche.
Dass sich Proteine unkontrolliert an Polymerfäden anlagern, ist in der Medizin ein gefürchteter Effekt. Er tritt normalerweise sehr schnell auf, wenn Materialien in den Körper eingesetzt wird. „Auf den hydrophoben Oberflächen werden die Proteine schnell denaturiert“, sagt Groll. Dadurch besteht die Gefahr, dass das Immunsystem aktiviert wird und die Wundheilung gestört – alles unerwünschte Nebenwirkungen. „Deshalb ist es äußerst wichtig, die Anlagerung solcher Proteine zu verhindern“, so der Polymerchemiker.
Baugerüst für körpereigene Zellen
Andere Anheftungen sind hingegen mehr als erwünscht: Körpereigene Zellen sollen sich an den Faserstrukturen anlagern, untereinander verbinden und zu einer kompakten Struktur heranwachsen. Auf diese Weise können Mediziner beispielsweise dem Körper dabei helfen, großflächige Verletzungen schneller wieder zu schließen. Im Labor arbeiten Wissenschaftler daran, mit Hilfe dieser Fasern neue Gewebe, möglicherweise sogar neue Organe zu produzieren. Dazu „basteln“ sie mit den Polymerfäden dreidimensionale Gerüste in der benötigten Form, auf denen sich anschließend die gewünschten Zellen ansiedeln – beispielsweise Leberzellen, wenn es darum geht, eine neue Leber herzustellen, oder Knorpelzellen, die Ersatz für zerstörte Gelenkoberflächen schaffen sollen.
Der Vorteil solcher Implantate liegt auf der Hand: Weil sich das neue Organ aus Zellen des jeweiligen Patienten entwickelt hat, kommt es nach der Implantation zu keiner Abstoßungsreaktion. Auf eine medikamentöse Therapie, die heutzutage nach Fremdtransplantationen zwingend erforderlich ist, kann deshalb verzichtet werden. Und die Fasern werden nach wenigen Monaten rückstandslos abgebaut.
Neue Organe wachsen im Labor
„Je nachdem, welche Zellen sich an den Fasern anlagern sollen, geben wir ihnen die entsprechenden bioaktive Peptide auf der Oberfläche mit“, sagt Groll. Diese sorgen dafür, dass genau die Zellen angelockt werden, die im jeweiligen Fall benötigt werden.
Mit der von Groll und seinen Mitarbeitern entwickelten Technik lassen sich jetzt deutlich schneller als bisher Fasern und Faserstrukturen herstellen und mit den unterschiedlichsten Eigenschaften versehen. Groll ist überzeugt davon, dass es diese Technik schon in naher Zukunft möglich macht, im Labor Strukturen zu konstruieren, auf denen komplexe Gewebe wachsen können.
“Degradable polyester scaffolds with controlled surface chemistry combining minimal protein adsorption with specific bioactivation”, Dirk Grafahrend, Karl-Heinz Heffels, Meike V. Beer, Peter Gasteier, Martin Möller, Gabriele Boehm, Paul D. Dalton and Jürgen Groll. Nature Materials, DOI: 10.1038/NMAT2904
Kontakt
Professor Jürgen Groll,
T: (0931) 201 73610,
E-Mail: juergen.groll@fmz.uni-wuerzburg.de
Media Contact
Weitere Informationen:
http://www.uni-wuerzburg.deAlle Nachrichten aus der Kategorie: Materialwissenschaften
Die Materialwissenschaft bezeichnet eine Wissenschaft, die sich mit der Erforschung – d. h. der Entwicklung, der Herstellung und Verarbeitung – von Materialien und Werkstoffen beschäftigt. Biologische oder medizinische Facetten gewinnen in der modernen Ausrichtung zunehmend an Gewicht.
Der innovations report bietet Ihnen hierzu interessante Artikel über die Materialentwicklung und deren Anwendungen, sowie über die Struktur und Eigenschaften neuer Werkstoffe.
Neueste Beiträge
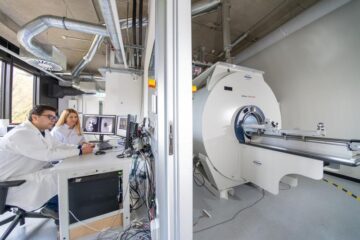
Diamantstaub leuchtet hell in Magnetresonanztomographie
Mögliche Alternative zum weit verbreiteten Kontrastmittel Gadolinium. Eine unerwartete Entdeckung machte eine Wissenschaftlerin des Max-Planck-Instituts für Intelligente Systeme in Stuttgart: Nanometerkleine Diamantpartikel, die eigentlich für einen ganz anderen Zweck bestimmt…
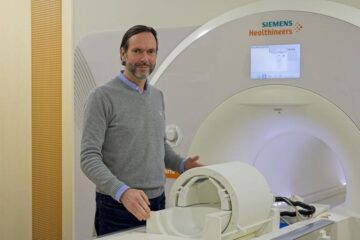
Neue Spule für 7-Tesla MRT | Kopf und Hals gleichzeitig darstellen
Die Magnetresonanztomographie (MRT) ermöglicht detaillierte Einblicke in den Körper. Vor allem die Ultrahochfeld-Bildgebung mit Magnetfeldstärken von 7 Tesla und höher macht feinste anatomische Strukturen und funktionelle Prozesse sichtbar. Doch alleine…
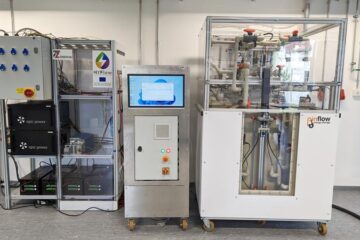
Hybrid-Energiespeichersystem für moderne Energienetze
Projekt HyFlow: Leistungsfähiges, nachhaltiges und kostengünstiges Hybrid-Energiespeichersystem für moderne Energienetze. In drei Jahren Forschungsarbeit hat das Konsortium des EU-Projekts HyFlow ein extrem leistungsfähiges, nachhaltiges und kostengünstiges Hybrid-Energiespeichersystem entwickelt, das einen…