Züge im Leichtbauformat

Diese Dieselmotoreinhausung für Züge ist aus einem leichten Polyurethan-basierenden Material gefertigt und dennoch extrem belastbar. © Fraunhofer ICT<br>
Ein neues Material hält nun auch extremen Belastungen stand. Es eignet sich etwa für die Dieselmotoreinhausungen von Zügen – dieses Bauteil wird dadurch 30 Prozent günstiger und über 35 Prozent leichter als das Gegenstück aus Stahl und Aluminium.
Autos und Züge sollen energiesparender werden – die Hersteller versuchen daher, die gängigen Materialien durch leichtere zu ersetzen. Eine Hürde dabei: Die leichten Materialien sind nicht genauso belastbar wie Stahl und Aluminium, die Werkstoffe können nicht eins zu eins ersetzt werden. Vielmehr müssen die Hersteller abwägen, welche Bauteile abspecken dürfen und wie sich diese in das Gesamtsystem integrieren lassen.
Forscher des Fraunhofer-Instituts für Chemische Technologie ICT in Pfinztal haben nun ein Polyurethan-basierendes Sandwichmaterial entwickelt, das extrem belastbar ist – gemeinsam mit Bombardier GmbH, Krauss-Maffei Kunststofftechnik GmbH, Bayer MaterialScience AG, der DECS GmbH, dem DLR-Institut für Fahrzeugkonzepte, der Universität Stuttgart und dem Karlsruher Institut für Technologie. »Als Demonstrator haben wir daraus zunächst ein Bauteil hergestellt, das stark beansprucht wird und viele Anforderungen erfüllen muss: die Dieselmotoreinhausung von Zügen«, sagt Jan Kuppinger, Wissenschaftler am ICT. Diese Einhausung befindet sich unter der Fahrgastzelle, also zwischen Abteil und Schienen. Hier schützt sie den Motor vor Steinschlägen und die Umgebung vor eventuell ausgelaufenem Öl. Im Brandfall verhindert sie, dass sich die Flammen ausbreiten und erfüllt somit die geforderten Flamm- und Brandschutznormen für Schienenfahrzeuge. »Mit dem neuen Material können wir das Gewicht der Bauteile um mehr als 35 Prozent reduzieren, und die Kosten um 30 Prozent«, sagt Kuppinger.
Die Stabilität des Bauteils erreichen die Forscher durch einen Sandwich-Aufbau: Außen befindet sich jeweils eine glasfaserverstärkte Polyurethanschicht, innen ein Kern aus Pappwaben. Polyurethan ist ein Massenkunststoff aus zwei Komponenten, den man an verschiedene Anforderungen anpassen kann, er wird daher auch als »Werkstoff nach Maß« bezeichnet. Aufgeschäumt ist er weich und dient beispielsweise als Material für Matratzen, in seiner kompakten Form dagegen ist er fest und hart. Die Forscher haben das Polyurethan durch verschiedene Zusätze zunächst so verändert, dass es die Brandschutznormen erfüllt. In einem zweiten Schritt haben die Partner das hierfür gängige Fertigungsverfahren, das Fasersprühen, optimiert: Sie haben einen Mischkopf entwickelt, mit dem sie auch komplexe Strukturen in der benötigten Größe herstellen können. Die hergestellte Dieselmotoreinhausung ist etwa 4,5 Meter lang und über zwei Meter breit. »Erstmals ist es gelungen, über dieses Verfahren ein so großes und komplexes Bauteil herzustellen, das den strukturellen Anforderungen genügt«, erläutert Kuppinger. Ein Problem beim Fasersprühen lag bisher darin, dass die Dicke der entstandenen Polyurethan-Sandwichdeckschichten nicht genau bestimmt werden konnte. Dies ist den Forschern nun gelungen: Sie haben die hergestellten Schichten mit einem Computer-Tomographen untersucht und über eine angepasste Auswerteroutine die genaue Schichtdicke ermittelt. Diese Informationen helfen dabei, die Festigkeit des Bauteils zu simulieren – und somit zu wissen, welche Belastung es aushält.
Einen Demonstrator der Dieselmotoreinhausung haben die Wissenschaftler in dem vom Bundesministerium für Bildung und Forschung BMBF geförderten Projekt PURtrain bereits hergestellt. Er hat den ersten Festigkeitstest mit Bravour bestanden: Dabei haben die Wissenschaftler in einem Versuchsstand Kräfte auf verschiedene Stellen des Demonstrators ausgeübt und gemessen, wie stark er sich verformt. In einem weiteren Schritt wollen die Forscher das Bauteil in einem realen Feldversuch testen. Verläuft er erfolgreich, dann können aus dem Material auch Dachsegmente, Seitenklappen und Windabweiser für die Automobil- und Nutzfahrzeugindustrie gefertigt und der Herstellungsprozess auf mittlere Stückzahlen zwischen 250 und 30 000 übertragen werden.
Media Contact
Alle Nachrichten aus der Kategorie: Maschinenbau
Der Maschinenbau ist einer der führenden Industriezweige Deutschlands. Im Maschinenbau haben sich inzwischen eigenständige Studiengänge wie Produktion und Logistik, Verfahrenstechnik, Fahrzeugtechnik, Fertigungstechnik, Luft- und Raumfahrttechnik und andere etabliert.
Der innovations-report bietet Ihnen interessante Berichte und Artikel, unter anderem zu den Teilbereichen: Automatisierungstechnik, Bewegungstechnik, Antriebstechnik, Energietechnik, Fördertechnik, Kunststofftechnik, Leichtbau, Lagertechnik, Messtechnik, Werkzeugmaschinen, Regelungs- und Steuertechnik.
Neueste Beiträge
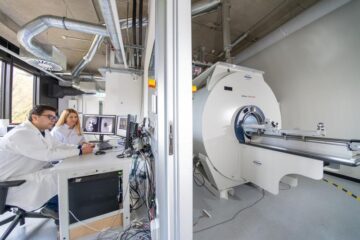
Diamantstaub leuchtet hell in Magnetresonanztomographie
Mögliche Alternative zum weit verbreiteten Kontrastmittel Gadolinium. Eine unerwartete Entdeckung machte eine Wissenschaftlerin des Max-Planck-Instituts für Intelligente Systeme in Stuttgart: Nanometerkleine Diamantpartikel, die eigentlich für einen ganz anderen Zweck bestimmt…
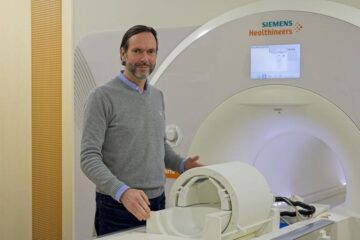
Neue Spule für 7-Tesla MRT | Kopf und Hals gleichzeitig darstellen
Die Magnetresonanztomographie (MRT) ermöglicht detaillierte Einblicke in den Körper. Vor allem die Ultrahochfeld-Bildgebung mit Magnetfeldstärken von 7 Tesla und höher macht feinste anatomische Strukturen und funktionelle Prozesse sichtbar. Doch alleine…
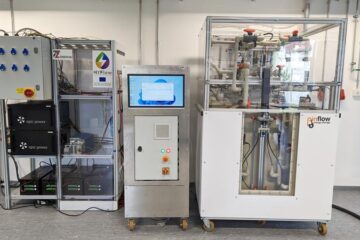
Hybrid-Energiespeichersystem für moderne Energienetze
Projekt HyFlow: Leistungsfähiges, nachhaltiges und kostengünstiges Hybrid-Energiespeichersystem für moderne Energienetze. In drei Jahren Forschungsarbeit hat das Konsortium des EU-Projekts HyFlow ein extrem leistungsfähiges, nachhaltiges und kostengünstiges Hybrid-Energiespeichersystem entwickelt, das einen…