Heißisostatisches Pressen bei konstruktiver Bauteilanpassung vorteilhaft
Das heißisostatische Pressen (HIP) gehört zu den gängigen Verfahren zur Herstellung von pulvermetallurgischem Stahl. Hierbei wird ein Blechbehälter mit gasverdüstem Stahlpulver gefüllt, evakuiert und gasdicht abgedichtet. Diese Kapsel setzt man dann bei Temperaturen bis 1100 °C einem hohen Gasdruck (bis 1400 bar) aus, wodurch das Pulver im Inneren gesintert wird und einen Stahlkörper mit homogener Struktur bildet.
Pulver lässt sich auf Stahl gut heißisostatisch pressen
Das heißisostatische Pressen ermöglicht auch, feste Pulverschichten auf herkömmliche Stahlkörper aufzubringen, welche die Oberfläche ganz oder teilweise bedecken. Außerdem lassen sich damit Formteile aus Werkstoffkombinationen herstellen, die durch Schweißen nicht erzielt werden können.
Das gab den Ausschlag für die Prämierung eines Zylinders mit kegelförmiger Innenbeschichtung auf der HIP 2008. Dort erhielt dieses Bauteil einem Preis für das Beste seiner Klasse. Der Zylinder wurde in enger Zusammenarbeit mit dem Kunden und unter Ausnutzung wesentlicher Vorteile des heißisostatischen Pressens verwirklicht.
Werkstoffverbund ermöglicht stabilen Verschleißschutz
Ziel des Werkstoffverbunds ist es, dieses Hohlteil im Innern mit einer stabilen Verschleißschutzschicht zu versehen. In diesem Einschneckenzylinder wird Roh-Methylzellulose unter hohen Temperaturen und Drücken „geschoren“. Dabei ist die Innenfläche des Zylinders einem erheblichen Abriebverschleiß ausgesetzt.
Methylzellulose wird im Wesentlichen in der Bauindustrie als Zusatz zu Zement oder Gips verwendet, um die Abbindezeit zu verzögern. Methylzellulose ist auch Hauptbestandteil in Tapetenkleistern. Außerdem ist es in vielen Nahrungsmittel- und Körperpflegeprodukten enthalten.
Zum Schutz des Zylinders gegen extremen Verschleiß wird üblicherweise eine Legierung auf Kobaltbasis als Innenbeschichtung aufgebracht. Bei diesem Projekt führte die Zusammenarbeit mit dem Kunden zu einer verbesserten Kapselkonstruktion und zu innovativen Bearbeitungstechniken für das heißisostatische Pressen.
Heißisostatisches Pressen ermöglicht besseres Bauteil
Die Entwicklung ging schrittweise voran, in vier einzelnen Phasen. Das Endergebnis war ein komplexes Bauteil – eines, das für die spezielle Anwendung besser geeignet ist.
Üblicherweise wird der Grundkörper aus dem Werkstoff 304L in eine zylindrische Form gebracht. Danach setzt man einen kegelförmigen Kern, der das Innenprofil des Einschneckenzylinders bildet, in die Innenbohrung ein. Beides wird mit Hilfe standardmäßiger Kapselungsverfahren abgedichtet. Schließlich kommt das Beschichtungspulver dazu. Die Baugruppe wird heißisostatisch gepresst.
Hartstoffschicht muss nach dem heißisostatischen Pressen bearbeitet werden
Fertigt man das Teil auf diese Weise, so muss die aufgebrachte Hartstoffschicht im Anschluss an das heißisostatische Pressen aufwändig bearbeitet werden, weil das fertige Bauteil einen doppelten Gewindegang auf der Innenfläche hat. Dieses Innenprofil wird benötigt, um zusammen mit der Schnecke die hohen Scherkräfte zu erzeugen, die für die Methylzellulose-Produktion nötig sind.
Weil sich der Hartstoff nicht spanend bearbeitet lässt, wird das Gewinde durch einen äußerst kostenintensiven Schleifprozess hergestellt. Zusätzlich zu den hohen Bearbeitungskosten geht dadurch auch viel vom sehr teuren Pulver verloren.
Vorprofilierter Stahlkern zum Abbilden der Geometrie
Jedoch kann zur Herstellung der Innengeometrie auch ein massiver, negativ vorprofilierter Kern verwendet werden. Dieser Kern wird in der zweiten Phase der Produktentwicklung hergestellt, um die Bearbeitungskosten zu minimieren und Werkstoff einzusparen.
Auf diese Weise ermöglicht das heißisostatische Pressen, die Gewindeform in der Verschleißschutzschicht abzubilden. Der Kern besteht aus kostengünstigem, einfachem Kohlenstoffstahl, der weich bleibt und deshalb nach der HIP-Behandlung leicht zu bearbeiten ist.
Um eine Diffusion zwischen dem Kern und dem Kobaltbasis-Pulver zu verhindern, wird der Kern im Plasmasprühverfahren mit einem keramischen Werkstoff beschichtet. Nach dem heißisostatischen Pressen lässt sich der Kern durch Zerspanen entfernen. Die Nuten der Gewindeform sind fertig. Die einzige noch verbleibende Arbeit ist ein leichtes Schleifen der Gewindestege auf den fertigen Innendurchmesser.
In diesem Zylinderstadium werden an beiden Seiten des Bauteils Flansche angebracht, die zum Einbau des Zylinders in den Extruder erforderlich sind. Bisher hat man diese Flansche nach dem Beschichten an das Rohteil geschweißt. Zuvor musste ein aus Blech gefertigtes Kühlsystem am Zylindermantel angebracht werden.
Verzicht auf Schweißprozesse erhöht Fertigungssicherheit
Bei der ursprünglichen Fertigungsmethode erzeugte das Anschweißen des Kühlsystems und der Flansche an den Zylinder Wärmespannungen, die zur Bildung von Rissen in der Hartschicht führen konnten. Solche Risse machen den Zylinder unbrauchbar. Um das zu vermeiden, erfolgt das Schweißen üblicherweise bei kontinuierlicher Erwärmung des Rohlings in kleinen Schritten – ein langwieriger und kritischer Fertigungsschritt, der es notwenig machte einen alternativen Fertigungsweg zu suchen.
Die Lösung fand man in der Kühlung des Systems. Heute müssen die Flansche nicht mehr angeschweißt werden. Sie werden pulvermetallurgisch durch heißisostatisches Pressen hergesellt.
Zylinderfertigung in zwei Schritten
Bei der heutigen Zylinderfertigung sind zwei Verfahrensschritte zu einem zusammengefasst. So werden der Edelstahl-Grundkörper und die kobaltbasierte Innenbeschichtung aus Pulver gefertigt. Zusammen mit der Kapselkonstruktion werden auch die Flansche gebildet. Ein Zwischenblech gewährleistet die Trennung beider pulverförmiger Werkstoffe, dem Edelstahl 304L und der kobaltbasierten Hartbeschichtung.
Weil bei der neuen Konstruktion die Grundform aus Pulver gefertigt wird, ist es möglich, eine spiralförmige Röhre in das Pulver einzulegen. Die Röhre wird am Ende der Grundform auf dem Blech-Zwischenstück befestigt und mit dem Edelstahlpulver umgeben.
Röhre wird beim heißisostatischen Pressen nicht zusammengedrückt
Um zu verhindern, dass die Röhre während des heißisostatischen Pressens zusammengedrückt wird, muss sie zur Umgebung der Kapsel offen und gegenüber dem Innenraum der Kapsel gasdicht ausgelegt sein. Zu diesem Zweck wird die spiralförmige Röhre auf einer Seite verschlossen und so gebogen, dass dieses Ende im großen Flansch liegt. Das andere Ende wird aus der Kapsel herausgeführt und so verschweißt, dass der Außendurchmesser der Röhre mit der Kapsel gegenüber der Umgebung gasdicht ist.
Nachdem die Kapsel fertiggestellt ist, wird die Lage des verschlossenen Endes der spiralförmigen Röhre im Inneren des Flansches durch Ultraschallmessung ermittelt, so dass sich nach der Endbearbeitung der zweite Anschluss des Kühlsystems von außerhalb an der richtigen Stelle anbringen lässt.
Heißisostatisches Pressen spart Rohstoffe und Kosten
Die Fertigungsanpassung bei einem komplexen Bauteil, wie dem Einschneckenzylinder, an die HIP-Technik hat eine Einsparung teuerer Rohstoffe bei gleichzeitiger Minimierung der Fertigungskosten bewirkt. Aufgrund dieser Methode ist es nicht mehr notwendig, einen Rohling im Voraus vorzubereiten. Außerdem ist die Gefahr, dass während der Bearbeitung Ausschuss entsteht, ausgeschlossen.
Das heißisostatische Pressen ermöglicht, die Kühlspirale direkt hinter der Hartbeschichtung zu platzieren – an einer optimalen Stelle in unmittelbarer Nähe der Wärmequelle. Die verbesserte Kühlung führte zu minimalem Zylinderverschleiß und zu einem Produkt von gleichbleibend hoher Qualität. Die Zylinderstandzeit wurde durch das integrierte Kühlsystem praktisch verdoppelt.
Viele herkömmliche Fertigungsschritte wurden durch Anwendung des heißisostatischen Pressens vereinfacht oder entfielen sogar ganz. Vorraussetzung ist eine enge Zusammenarbeit mit dem Kunden. Nur so lassen sich vorteilhafte Lösungen für beide Seiten erarbeiten. Bei einer gewissen Risikobereitschaft sind die Anwendungsmöglichkeiten für HIP-Produkte praktisch unbegrenzt.
Lothar Bruder ist Market Product Manager bei der Kennametal HTM AG in CH-2503 Biel.
Media Contact
Alle Nachrichten aus der Kategorie: Maschinenbau
Der Maschinenbau ist einer der führenden Industriezweige Deutschlands. Im Maschinenbau haben sich inzwischen eigenständige Studiengänge wie Produktion und Logistik, Verfahrenstechnik, Fahrzeugtechnik, Fertigungstechnik, Luft- und Raumfahrttechnik und andere etabliert.
Der innovations-report bietet Ihnen interessante Berichte und Artikel, unter anderem zu den Teilbereichen: Automatisierungstechnik, Bewegungstechnik, Antriebstechnik, Energietechnik, Fördertechnik, Kunststofftechnik, Leichtbau, Lagertechnik, Messtechnik, Werkzeugmaschinen, Regelungs- und Steuertechnik.
Neueste Beiträge
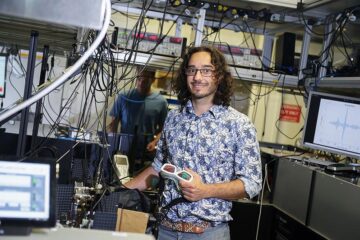
Neue universelle lichtbasierte Technik zur Kontrolle der Talpolarisation
Ein internationales Forscherteam berichtet in Nature über eine neue Methode, mit der zum ersten Mal die Talpolarisation in zentrosymmetrischen Bulk-Materialien auf eine nicht materialspezifische Weise erreicht wird. Diese „universelle Technik“…

Tumorzellen hebeln das Immunsystem früh aus
Neu entdeckter Mechanismus könnte Krebs-Immuntherapien deutlich verbessern. Tumore verhindern aktiv, dass sich Immunantworten durch sogenannte zytotoxische T-Zellen bilden, die den Krebs bekämpfen könnten. Wie das genau geschieht, beschreiben jetzt erstmals…

Immunzellen in den Startlöchern: „Allzeit bereit“ ist harte Arbeit
Wenn Krankheitserreger in den Körper eindringen, muss das Immunsystem sofort reagieren und eine Infektion verhindern oder eindämmen. Doch wie halten sich unsere Abwehrzellen bereit, wenn kein Angreifer in Sicht ist?…