Forscher entwickeln Leichtbau-Materialien aus Aluminium und Magnesium
Bleibt die Karosserie, die bei einem durchschnittlichen Auto immerhin 30% des Gesamtgewichts ausmacht. Rund die Hälfte davon wiederum stammt von den tragenden Teilen, die mit den Magnesium-Bauteilen deutlich leichter konstruiert werden können. Walter Reimers vom Institut für Werkstoffwissenschaften und -technologien der TU Berlin forscht dazu.
Magnesium hat für Leichtbauweisen nahezu das Idealgewicht: Wiegt ein Stahlwürfel mit jeweils zehn Zentimeter Länge, Breite und Höhe noch 8,6 kg, bringt ein Aluminium-Würfel der gleichen Dimension 2,7 kg auf die Waage, während ein genauso großer Magnesiumblock nur noch 1,8 kg wiegt. Da jedes reduzierte Kilogramm Fahrzeuggewicht Sprit spart, sollten Auto-Hersteller eigentlich möglichst viel Stahl durch Aluminium oder noch besser durch Magnesium ersetzen.
Seit 1993 gibt es Aluminium-Autos
Tatsächlich gibt es bereits seit 1993 Autos mit Aluminium-Karosserien. Von tragenden Teilen aus Magnesium im Auto ist jedoch bisher aus einem naheliegenden Grund kaum etwas bekannt: Korrosion setzt üblichen Legierungen aus 96% Magnesium, drei Prozent Aluminium und einem Prozent Zink sehr rasch zu. Obendrein gibt es für solche Legierungen keine in der Praxis erprobten Verfahren, mit denen einzelne Teile zu einer Karosserie zusammengeschweißt werden können.
Beide Probleme will Walter Reimers mit einer Art Schutzhülle für das Magnesium lösen. Um einen Block aus der Magnesium-Legierung legt er einfach eine Aluminium-Folie, die ein bis zwölf Millimeter dick ist. Dieses Material bringen die Wissenschaftler dann mit einer Strangpresse genannten Maschine in die Formen, die Automobilbauer für die tragenden Teile der Karosserie brauchen.
An einem Ende der Maschine wird der zum Beispiel zehn Zentimeter dicke Magnesium-Block mit seiner Aluminiumhülle eingeführt und bei einer Temperatur von rund 330 °C mit einigem Druck durch eine Matrize gepresst, die dem Material seine endgültige Form gibt. Am anderen Ende der Matrize kommt dann zum Beispiel ein Zentimeter oder auch nur zwei Millimeter dicker Strang im benötigten T-, runden oder eckigen Profil heraus.
Gut vor Korrosion geschützt
Das Material aber hat sich beim Pressen verändert. Zwar umhüllt immer noch eine dünne Aluminium-Schutzschicht den leichten und viel dickeren Magnesiumkern. Durch den Druck und die Temperatur aber sind die beiden Materialien an ihren Kontaktstellen zu einer sogenannten intermetallischen Phase verschmolzen, die extrem dünn ist und zum Beispiel aus einer Mischung von jeweils 17 Magnesium-Atomen mit jeweils zwölf Aluminium-Atomen besteht. Wie ein extrem haltbarer Leim verbindet diese intermetallische Phase jetzt Magnesiumkern und Aluminiumhülle so fest miteinander, dass die Konstrukteure damit arbeiten können.
Um das Verfahren weiter zu verbessern, rechnen die Forscher im Computer aus, mit welchen Temperaturen, welchem Druck und welcher Geschwindigkeit das jeweilige Profil am besten gepresst wird. In der Strangpresse optimieren sie anschließend die im Rechner erhaltenen Bedingungen weiter, bis die intermetallische Phase Aluminiumhülle und Magnesiumkern optimal verbindet und gleichzeitig das vor Korrosion schützende Aluminium überall das empfindliche Magnesium sauber vor Feuchtigkeit schützt.
Die Ingenieure haben dann einen Werkstoff vor sich, der von außen wie Aluminium aussieht und sich auch wie Aluminium bearbeiten lässt, der aber nahezu so leicht wie reines Magnesium ist. Das Magnesium im Inneren ist so perfekt vor Korrosion geschützt. Die Aluminiumhülle wiederum kann zu einer Karosserie verschweißt werden, weil es für Aluminium längst gut etablierte Schweißverfahren in der Industrie gibt.
Magnesiumlegierung durch Flachmatrizen zu dünnen Blech pressen
Inzwischen haben die Wissenschaftler um Walter Reimers bereits ein Patent, mit dem man den Werkstoff weiter verbessern kann: Von der Matrize wird der entstehende Strang gleich in ein mit Flüssigkeit gefülltes Rohr gepresst. Dort baut sich dann ein Druck auf, der Magnesium rund 50% fester zusammenpresst und so die Eigenschaften des Materials weiter verbessert.
Walter Reimers und seine Mitarbeiter arbeiten mittlerweile auch an Verfahren, die Magnesiumlegierung durch Flachmatrizen zu etwa 1,5 mm dicken Blechen zu pressen, die anschließend zu handelsüblichen 0,7 mm dicken Blechen ausgewalzt werden. Die können dann mit altbekannten Verfahren wie dem Galvanisieren mit einer Aluminiumhülle vor Korrosion geschützt und für nicht tragende Teile der Autokarosserie verwendet werden.
Der Leichtbau-Magnesium-Karosserie scheint die Zukunft zu gehören. Und da die anfänglich relativ hohen Magnesiumpreise in den nächsten Jahrzehnten erheblich sinken dürften, sobald die ersten Fahrzeuge mit solch einer Karosserie verschrottet und das Magnesium recycelt wird, sollte das Spritsparen und Klimaschützen auf diesem Weg in weiterer Zukunft langfristig auch nicht allzu teuer werden.
Media Contact
Weitere Informationen:
http://www.maschinenmarkt.vogel.de/themenkanaele/konstruktion/werkstoffe/articles/145955/Alle Nachrichten aus der Kategorie: Maschinenbau
Der Maschinenbau ist einer der führenden Industriezweige Deutschlands. Im Maschinenbau haben sich inzwischen eigenständige Studiengänge wie Produktion und Logistik, Verfahrenstechnik, Fahrzeugtechnik, Fertigungstechnik, Luft- und Raumfahrttechnik und andere etabliert.
Der innovations-report bietet Ihnen interessante Berichte und Artikel, unter anderem zu den Teilbereichen: Automatisierungstechnik, Bewegungstechnik, Antriebstechnik, Energietechnik, Fördertechnik, Kunststofftechnik, Leichtbau, Lagertechnik, Messtechnik, Werkzeugmaschinen, Regelungs- und Steuertechnik.
Neueste Beiträge
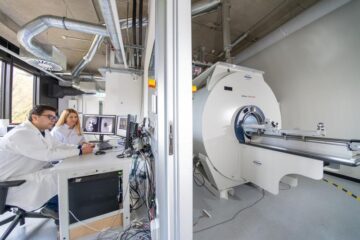
Diamantstaub leuchtet hell in Magnetresonanztomographie
Mögliche Alternative zum weit verbreiteten Kontrastmittel Gadolinium. Eine unerwartete Entdeckung machte eine Wissenschaftlerin des Max-Planck-Instituts für Intelligente Systeme in Stuttgart: Nanometerkleine Diamantpartikel, die eigentlich für einen ganz anderen Zweck bestimmt…
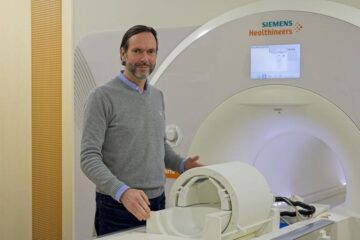
Neue Spule für 7-Tesla MRT | Kopf und Hals gleichzeitig darstellen
Die Magnetresonanztomographie (MRT) ermöglicht detaillierte Einblicke in den Körper. Vor allem die Ultrahochfeld-Bildgebung mit Magnetfeldstärken von 7 Tesla und höher macht feinste anatomische Strukturen und funktionelle Prozesse sichtbar. Doch alleine…
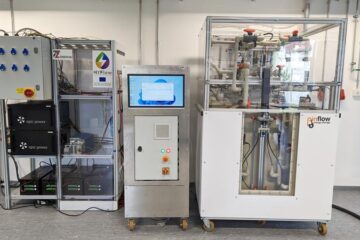
Hybrid-Energiespeichersystem für moderne Energienetze
Projekt HyFlow: Leistungsfähiges, nachhaltiges und kostengünstiges Hybrid-Energiespeichersystem für moderne Energienetze. In drei Jahren Forschungsarbeit hat das Konsortium des EU-Projekts HyFlow ein extrem leistungsfähiges, nachhaltiges und kostengünstiges Hybrid-Energiespeichersystem entwickelt, das einen…