Schneller Materialfluss beim Beschichten und Trocknen schwerer Bauteile
Es ist beeindruckend: Wie schwerelos schwebt ein Bagger-Unterwagen durch eine Halle im schwäbischen Kirchdorf, begleitet von einem blinkenden Warnlicht und regelmäßigen Gongschlägen zum Schutz der Mitarbeiter. Gleich dahinter folgen einige Ausleger und Drehbühnen zu mehreren an einem Gehänge. Der Unterwagen wiegt rund 11 t – die anderen Teile bringen zusammen sogar über 15 t auf die Waage. Liebherr war auf der Suche nach einer Lösung, die einen schnelleren Materialfluss und eine höhere Wirtschaftlichkeit bei der Beschichtung und Trocknung der Werkstücke ermöglicht.
Liebherrs bisherige Hänge-Beschichtungsanlage war lediglich auf Lasten bis 4 t ausgelegt, schwerere Teile wurden manuell transportiert. Für sie stand nur Bodenfördertechnik zur Verfügung, was die Lackierung jedoch erschwert. Eine deckengeführte Anlage bis 20 t schien für Liebherr zunächst nicht realisierbar – es gab bisher niemanden, der so eine Anlage gebaut hat.
Bereits seit 1949 fertigt, montiert und beschichtet Liebherr an seinem baden-württembergischen Stammsitz Hydraulikbagger. Das Einsatzgebiet der typischen gelben Riesen umfasst den Tief- und Tunnelbau, industrielle Umschlagtechnik, Abbruch- und Recyclingunternehmen sowie die Wasserwirtschaft.
Die Produktpalette beinhaltet Maschinen mit Einsatzgewichten zwischen 10 und 672 t. Im Werk Kirchdorf werden derzeit Bagger bis 77 t gefertigt – Tendenz steigend. Im Zuge einer Umstrukturierung der Produktion sollten deshalb der Beschichtungsprozess auch für schwere Teile automatisiert und die Lackierung auf umweltfreundliche, wasserlösliche 2-K-Hydrolacke umgestellt werden.
Neue Hängebahn für den Transport schwerer Teile
Eine Maschinenhalle, die bisher zum Schweißen von Teilen genutzt wurde, stand bereits zur Verfügung. Auf einer Gesamtfläche von 3500 m2 konnte also eine komplett neue Anlage erstellt werden.
Die Lösung lieferte Vollert Anlagenbau aus Weinsberg. Der Spezialist für schwere Lasten entwickelt neben Intralogistiksystemen für die Metall- und Automotive-Branche auch Förderanlagen
für die Baustoffindustrie, unter anderem für BetonfertigteilWerke.
Aus diesem Bereich stammt das Prinzip der neuen durchgehenden Ein-Träger-Hängelaufbahn für Teile bis zu 20 t Gewicht. Für die neue Anlage konnte Vollert auf seine Erfahrung aus der Baustoffindustrie zurückgreifen. Hier wurden bereits ähnliche Anlagen konzipiert.
Die hohe Traglast ist bei einer deckengeführten Anlage bisher allerdings einzigartig. Die Herausforderung bestand zudem darin, eine Anlage zu entwickeln, die aus Gründen des Explosionsschutzes in den Lackierstationen ohne elektrischen Einzelantrieb der Transporteinheiten auskommen sollte – das ist gelungen.
Perfekter Ex-Schutz: kein Motor, keine Stromversorgung
Die Lösung ist so einfach wie genial: Die von Vollert speziell entwickelten Transporteinheiten bestehen aus einem Gehänge, an dem die Werkstücke je nach Größe und Gewicht einzeln oder zu mehreren eingehängt werden. Die Höhe kann dabei um 2 m variiert werden. Die Gehänge fahren auf einer deckengeführten Laufschiene durch die gesamte Anlage, an der in regelmäßigen Abständen stationäre Reibradantriebe installiert sind, die für den nötigen Vorschub sorgen.
Drei Verteilmanipulatoren an zentralen Punkten, jeder mit einer Spannweite von 15,5 m und einem Gewicht von 14 t, übernehmen die Transporteinheiten und fahren sie zu den vorgesehenen Grundier-, Lackier-, Abdunst- und Trockenkabinen. Dabei zeigt sich dann der eigentliche Vorteil des Antriebsystems: Das Abschieben und Einholen der Gehänge in die Kabinen erfolgt mithilfe der Reibradtechnik und eines Zahnstangenantriebs, die auf dem Verteilmanipulator angebracht sind.
Keine stromführenden Anlagenteile in der Kabine ersparen Ex-Schutz-gesicherten Antrieb
Innerhalb der Kabinen sind deshalb keinerlei Motoren oder stromführende Anlagenteile notwendig – ein entscheidender Punkt für den Explosionsschutz. Zwar sind Ex-Schutz-gesicherte Antriebe möglich, diese sind jedoch wesentlich teurer. Außerdem ist die Technik dann der Verschmutzung beispielsweise durch Lacknebel ausgesetzt, was eine ständige Wartung erfordert.
Mit dem Reibradantrieb haben die Vollert-Ingenieure dagegen eine kostengünstige, dauerhafte und nahezu wartungsfreie Lösung mit einer hohen Verfügbarkeit gefunden: Die neue Anlage ist 24 h am Tag in Betrieb.
Als Generalunternehmer übernahm Vollert nicht nur die Planung, die Fördertechnik und den Stahlbau, sondern auch die Koordination für die weiteren Teile der Anlagentechnik. Insgesamt umfasst das vollständige System 17 Bearbeitungsplätze, darunter fünf Trocken- und Abdunst- sowie jeweils eine Reinigungs-, Grundier-, Lackier- und Kühlkabine.
Am Ende der Anlage befindet sich außerdem ein Rücklaufpuffer mit vier Plätzen. Dieser dient einerseits als freie Kühlstrecke nach dem Decklacktrocknen, andererseits zum Ausgleich von Produktionsschwankungen.
Manipulator mit 16 m Spannweite zum Be- und Entladen
Das Be- und Entladen übernimmt ein vierter Manipulator mit einer Spannweite von 16 m und einer Höhe von 10,5 m. Dieser ist als selbstfahrende Halbportallösung konzipiert, so dass keine störende aufgeständerte Laufbahn den Aktionsradius bei der Anlieferung der bis zu 12,5 m langen, 4,5 m hohen und 2,8 m breiten Teile einschränkt. Nach der Anlieferung werden die Teile in die Transporteinheit eingehängt, die sich im Belademanipulator befindet, und zur Reinigungskabine gefahren.
Am Ende der Durchfahrt übernimmt der erste von drei Verteilmanipulatoren die Trägereinheit mit dem Werkstück und bringt sie zum Abtropf- und danach zu einem freien Vorbereitungsplatz. Hier werden unter anderem nicht zu lackierende Flächen wie der Drehkranz der Bagger abgeklebt und Bohrungen vor dem Grundieren abgedichtet.
Außerdem wird der Transporteinheit ein entsprechender Datensatz zugeordnet, der Auskunft über die Art der Lackierung, RAL-Farbe, Temperatur und Trockendauer gibt. Die RAL-Nummer kann an der Grundier- und Lackierstation auf Displays abgerufen werden. Die Trocknersteuerung greift ebenfalls auf diesen Datensatz zu. Nach dem Quittieren durch den Werker erfolgen Anfahrt, Entnahme und der Weitertransport automatisch.
Insgesamt 19 Gehänge mit jeweils bis zu 20 t Gewicht sind ständig im Umlauf. Dank der parallelen Anordnung der Vorbereitungsplätze und Lackierkabinen ist außerdem jederzeit ein Queren und Kreuzen der Werkstücke und damit ein Überholen, Vorziehen, Ausschleusen oder ein Rücklauf möglich. Ein Durchfahrtspuffer führt parallel an den Arbeitsplätzen vorbei zu den Lackierkabinen.
Damit bietet die Ein-Träger-Hängelaufbahn von Vollert eine wesentlich höhere Flexibilität als andere. Bereits im Vorfeld der Planungen wurden die Prozessabläufe virtuell simuliert und die optimale Anzahl der Transporteinheiten für einen reibungslosen Ablauf ermittelt. Die gefundene Lösung garantiert damit schnellste Taktzeiten.
Umweltfreundliche Lackiertechnik
Auf die Ausstattung der Lackier- und Trockenkabinen spezialisiert ist Heimer Lackieranlagen und Industrie-lufttechnik aus Bielefeld. Zwei Kabinen dienen zum Grundieren und Decklackieren der Baggerteile. Vollautomatische Rolltore verhindern ein Austreten von Lacknebel und eine Verschmutzung der Oberflächen. Moderne Filteranlagen sorgen für das Absaugen und die Reinigung der Luft, wobei durch die Verwendung der wasserlöslichen 2-K-Hydrolacke ohnehin kaum noch Lösungsmittel im Lack enthalten sind.
Auch bei den anschließenden Kühl-, Abdunst- und Trockenkabinen setzt Liebherr auf eine umweltfreundliche Lösung: Die Trockner arbeiten mit 90% Umluft und lediglich 10% Frischluft. Durch einen Wärmetauscher in der Abdunstanlage wird die frische Luft außerdem vorgewärmt und wertvolle Energie zurückgeführt.
Hängebahn erreicht bis zu 0,5m/s
Fertig getrocknet fahren die Gehänge auf die Rücklaufstraße, an deren Ende die Werkstücke abgenommen und in die Endmontage überführt werden. Während aus Arbeitsschutzgründen in den Bereichen mit Werksverkehr Transportgeschwindigkeiten von 0,2 m/s gefahren werden, erreicht die Anlage im geschlossenen Lackierbereich und auf der Rücklaufstraße Geschwindigkeiten bis 0,5 m/s.
Obwohl dies die erste Anlage ihrer Art ist, ist man bei Liebherr von der Lösung absolut überzeugt. Im Vergleich zu vorher erreicht man jetzt kürzere Taktzeiten bei wesentlich höheren Lasten und ist gleichzeitig viel flexibler im Durchlauf.
Damit verfügt man über eine moderne, umweltfreundliche und wirtschaftlichere Anlage. Und auch die Projektzeit kann sich sehen lassen: Lediglich 15 Monate benötigten die Ingenieure von Vollert von der Planung bis zur endgültigen Abnahme.
Gerhard Geist ist Geschäftsführer der Vollert Anlagenbau GmbH + Co. KG in 74189 Weinsberg, Tel. (0 71 34) 52-2 43, gerhard.geist@vollert.de
Media Contact
Alle Nachrichten aus der Kategorie: Maschinenbau
Der Maschinenbau ist einer der führenden Industriezweige Deutschlands. Im Maschinenbau haben sich inzwischen eigenständige Studiengänge wie Produktion und Logistik, Verfahrenstechnik, Fahrzeugtechnik, Fertigungstechnik, Luft- und Raumfahrttechnik und andere etabliert.
Der innovations-report bietet Ihnen interessante Berichte und Artikel, unter anderem zu den Teilbereichen: Automatisierungstechnik, Bewegungstechnik, Antriebstechnik, Energietechnik, Fördertechnik, Kunststofftechnik, Leichtbau, Lagertechnik, Messtechnik, Werkzeugmaschinen, Regelungs- und Steuertechnik.
Neueste Beiträge
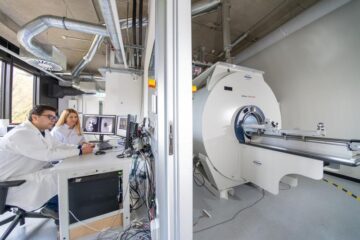
Diamantstaub leuchtet hell in Magnetresonanztomographie
Mögliche Alternative zum weit verbreiteten Kontrastmittel Gadolinium. Eine unerwartete Entdeckung machte eine Wissenschaftlerin des Max-Planck-Instituts für Intelligente Systeme in Stuttgart: Nanometerkleine Diamantpartikel, die eigentlich für einen ganz anderen Zweck bestimmt…
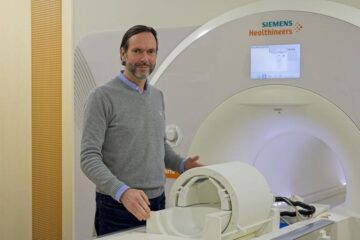
Neue Spule für 7-Tesla MRT | Kopf und Hals gleichzeitig darstellen
Die Magnetresonanztomographie (MRT) ermöglicht detaillierte Einblicke in den Körper. Vor allem die Ultrahochfeld-Bildgebung mit Magnetfeldstärken von 7 Tesla und höher macht feinste anatomische Strukturen und funktionelle Prozesse sichtbar. Doch alleine…
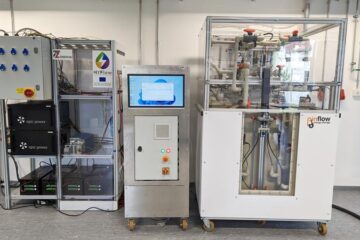
Hybrid-Energiespeichersystem für moderne Energienetze
Projekt HyFlow: Leistungsfähiges, nachhaltiges und kostengünstiges Hybrid-Energiespeichersystem für moderne Energienetze. In drei Jahren Forschungsarbeit hat das Konsortium des EU-Projekts HyFlow ein extrem leistungsfähiges, nachhaltiges und kostengünstiges Hybrid-Energiespeichersystem entwickelt, das einen…