3D-gedruckte Leichtbauteile für den Mittelstand
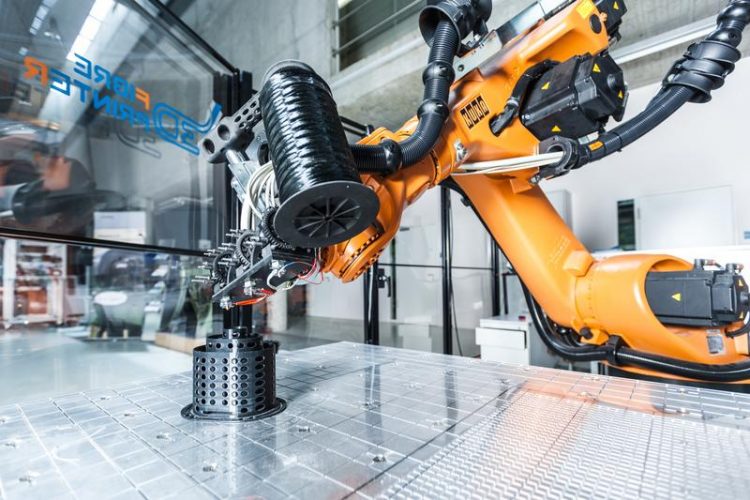
Der 3D Fibre Printer des Fraunhofer IPA ermöglicht es, Composites zu verdrucken und stabilere Bauteile herzustellen. (Quelle: Fraunhofer IPA, Foto: Rainer Bez)
Um Faserverbundwerkstoffe, sogenannte Composites, herzustellen, werden Fasern in einem formgebenden Matrixmaterial eingebettet. Bei den gängigen Verfahren gibt es allerdings noch Schwachstellen.
Einerseits können die Composites nicht mit den herkömmlichen Methoden der additiven Fertigung verarbeitet werden, andererseits ist bei der Stabilität der Bauteile noch Luft nach oben. In beiden Fällen schafft der 3D Fibre Printer des Fraunhofer IPA Abhilfe.
Mehr Stabilität durch optimale Faserauslegung
Allgemein gilt für eine möglichst hohe Stabilität im Werkstück, die Fasern bei der FVKHerstellung in Richtung der Kraftflüsse zu verlegen. Herkömmliche Verfahren wie Harzinjektion oder Laminieren stoßen hier schnell an ihre Grenzen.
»Da man meist auf die Faserausrichtung innerhalb eines textilen Halbzeugs beschränkt ist, muss man Abstriche bei der Festigkeit hinnehmen«, kritisiert Jonas Fischer, Wissenschaftler am Fraunhofer IPA. Der 3D Fibre Printer ist hingegen mit einer neuartigen Düse ausgestattet, die Endlosfasern direkt beim Drucken in den Kunststoffstrang integriert. »Da wir so erstmals Composites verdrucken können, eröffnen wir ein neues Kapitel im additiven Leichtbau «, freut sich Fischer.
Für mehr Stabilität und Flexibilität haben die Experten die Düse an einen Roboterdruckkopf montiert. Im Gegensatz zu konventionellen 3D-Fertigungsverfahren, welche über ein 3-achsiges System an den schichtweisen Aufbau einer Struktur gebunden sind, kann der 6-achsige Roboter Strukturen frei im Raum aufbauen. Dieses »Free Space Fabrication (FSF)« wird am Fraunhofer IPA in Kombination mit dem 3D Fiber Printer weiterentwickelt. Die erweiterte Produktionsfreiheit erlaubt es, die Fasern optimal entsprechend der Kraftflüsse im Werkstück zu platzieren.
Weil Endlosfasern, anstelle von Faserabschnitten im Werkstoffverbund verwendet werden, erhält das Bauteil zusätzliche Stabilität. »Mit den Faserverbundmaterialien kann gegenüber den heute in der additiven Fertigung eingesetzten Kunststoffen eine um etwa den Faktor zehn höhere Festigkeit erreicht werden«, freut sich Fischer. Weiterhin lasse sich mit der Technologie die für den 3D-Druck geeignete Werkstoffpalette entscheidend erweitern. Möglich seien, so Fischer, alle Thermoplast-Materialien, die sich mit der Düse aufschmelzen lassen, sowie die Kombination mit zahlreichen Fasern, z. B. Glas, Aramid oder Kohlenstoff. Auch die Verarbeitung biobasierter Kunststoffe und Naturfasern sei möglich.
Technologie soll Mittelstand zugänglich gemacht werden
Mit ihrem 3D Fibre Printer haben die IPA-Experten schon Materialprüfkörper für interne Tests gedruckt. Um ihn der Industrie zugänglich zu machen, muss er aber noch weiterentwickelt werden. Dies soll nun in gemeinsamen Projekten mit dem Netzwerk 3D-CP erfolgen. »Uns geht es vor allem darum, dem Mittelstand die Technologie zugänglich zu machen«, informiert Netzwerkmanager Markus Kafara von der Fraunhofer-Projektgruppe Regenerative Produktion in Bayreuth. Das nächste Treffen findet am 27. Juli Netzwerkpartner Picco’s 3D World in Deggendorf statt. Interessierte Unternehmen aus den Bereichen Digitalisierung, additive Fertigung oder FVK können noch beitreten und am Treffen teilnehmen.
Über das Netzwerk 3D Composite Print (3D-CP)
Das Netzwerk »3D Composite Print« (3D-CP) wurde im November 2015 von der Fraunhofer- Projektgruppe Regenerative Produktion und dem Lehrstuhl für Umweltgerechte Produktionstechnik der Universität Bayreuth gegründet. Ziel des Verbunds ist, neue Lösungen für die Herstellung von Leichtbauteilen mit 3D-Druck herzustellen. Im Fokus steht der Mittelstand. Bis heute sind acht Firmen aus Süddeutschland beigetreten. Dazu gehören Grundig Business Systems, ZCK, acad Prototyping, Carl Zeiss Optotechnik, Picco’s 3D World, isepos sowie die beiden jungen Unternehmen Maisenbachers und das Ingenieurbüro Dübon. Das Netzwerk ist offen für Forschungseinrichtungen, Firmen und Hochschulen.
Fachliche Ansprechpartner
Jonas Fischer | Telefon +49 711 970-1119 | jonas.fischer@ipa.fraunhofer.de | Fraunhofer-Institut für Produktionstechnik und Automatisierung IPA |
Markus Kafara | Telefon +49 921 78516-410 | markus.kafara@ipa.fraunhofer.de | Fraunhofer-Projektgruppe Regenerative Produktion |
Pressekommunikation
Ramona Hönl | Telefon +49 711 970-1638 | ramona.hoenl@ipa.fraunhofer.de |
http://www.ipa.fraunhofer.de/3d_fibre_printer.html
http://www.regenerative-produktion.fraunhofer.de
http://www.ipa.fraunhofer.de/
Media Contact
Alle Nachrichten aus der Kategorie: Maschinenbau
Der Maschinenbau ist einer der führenden Industriezweige Deutschlands. Im Maschinenbau haben sich inzwischen eigenständige Studiengänge wie Produktion und Logistik, Verfahrenstechnik, Fahrzeugtechnik, Fertigungstechnik, Luft- und Raumfahrttechnik und andere etabliert.
Der innovations-report bietet Ihnen interessante Berichte und Artikel, unter anderem zu den Teilbereichen: Automatisierungstechnik, Bewegungstechnik, Antriebstechnik, Energietechnik, Fördertechnik, Kunststofftechnik, Leichtbau, Lagertechnik, Messtechnik, Werkzeugmaschinen, Regelungs- und Steuertechnik.
Neueste Beiträge

Ein Herz so groß wie ein Stecknadelkopf
Uni Osnabrück untersucht Herzklappen von Fruchtfliegen… Gerade einmal zweieinhalb Millimeter messen die Fruchtfliegen (Drosophila melanogaster), an denen die Arbeitsgruppe der Zoologie und Entwicklungsbiologie der Uni Osnabrück forscht. Für die Untersuchung…

Waldinventur per Drohne und KI
Im Kampf gegen den Klimawandel sind Mangroven wichtige Verbündete; sie speichern bis zu fünfmal mehr Treibhausgase als andere Bäume. Dank einer von Forschenden aus Mitgliedseinrichtungen der U Bremen Research Alliance…

Beschichtungsverfahren der Zukunft
LZH und Cutting Edge Coatings auf der Optatec… Auf der Optatec 2024 zeigen das Laser Zentrum Hannover e.V. (LZH) und die Cutting Edge Coatings GmbH (CEC) neue Möglichkeiten der Beschichtungsverfahren…