Neues Design für Brennstoffzellen senkt Materialverbrauch und Kosten

Neues Design von Festoxid-Brennstoffzellen: dreifache Leistungsdichte mit flachem Röhrenverbund <br> <br>Siemens Pressebild
Brennstoffzellen gelten als eine der wichtigsten Innovationen für den Energiemarkt der Zukunft. Sie sind ideal, um Haushalte und Gewerbe dezentral mit Strom und Wärme zu versorgen. So geht der größte deutsche Energieversorger RWE davon aus, dass im Jahr 2015 rund zehn Prozent des Strombedarfs in Deutschland von Brennstoffzellen erzeugt werden. Siemens setzt dabei auf die Festoxid-Brennstoffzelle, die bei einer Temperatur von etwa 1000 Grad Celsius direkt mit dem umweltfreundlichen Brennstoff Erdgas betrieben werden kann und im Zusammenspiel mit einer Mikrogasturbine, die das heiße Abgas ausnutzt, einen elektrischen Wirkungsgrad von mehr als 55 Prozent erreicht. Wenn die Abwärme zusätzlich zum Heizen verwendet wird, könnte der Gesamtwirkungsgrad sogar auf über 80 Prozent gesteigert werden – Brennstoffzellen bieten also eine extrem gute Ausnutzung des Erdgases bei gleichzeitig sehr niedrigen Umweltbeeinträchtigungen.
Siemens baut derzeit in Pittsburgh im US-Staat Pennsylvania eine Fabrik für Brennstoffzellen-Kraftwerke. Ab 2004 sollen dort die ersten Anlagen in Serie produziert werden. Hauptproblem aller Entwicklungen in der Brennstoffzellentechnik ist der hohe Preis. Um marktfähig zu werden, müssen die Kosten pro Kilowatt auf etwa 1500 Euro sinken.
Dies wird derzeit noch nicht erreicht, aber Siemens arbeitet an etlichen Konzepten, um die Kosten drastisch zu senken. Beispielsweise gibt es derzeit im Inneren der Brennstoffzellen lange Röhren, ähnlich Besenstielen, in die Luft geblasen wird und die außen von Erdgas umströmt sind. Jede Röhre liefert bei der Reaktion von Wasserstoff und Sauerstoff eine Spannung von mehr als einem halben Volt und eine Stromstärke von 160 Ampere. Um höhere Spannungen zu erreichen, werden Röhren über leitende Streben verbunden. Der dabei auftretende elektrische Widerstand führt aber zu Verlusten. Wie das Magazin „Pictures of the Future“ berichtet, haben Siemens-Forscher jetzt den Widerstand deutlich gesenkt: Die Brennstoffzellen werden als flache Platten gebaut, in denen bis zu zehn Röhren nebeneinander liegen. Dadurch kann der Strom einen kürzeren Weg nehmen; das platzsparende Design ermöglicht die dreifache Leistungsdichte bei gleichem Verbrauch von Material, das heute der größte Kostenfaktor ist.
Media Contact
Alle Nachrichten aus der Kategorie: Energie und Elektrotechnik
Dieser Fachbereich umfasst die Erzeugung, Übertragung und Umformung von Energie, die Effizienz von Energieerzeugung, Energieumwandlung, Energietransport und letztlich die Energienutzung.
Der innovations-report bietet Ihnen hierzu interessante Berichte und Artikel, unter anderem zu den Teilbereichen: Windenergie, Brennstoffzellen, Sonnenenergie, Erdwärme, Erdöl, Gas, Atomtechnik, Alternative Energie, Energieeinsparung, Fusionstechnologie, Wasserstofftechnik und Supraleittechnik.
Neueste Beiträge
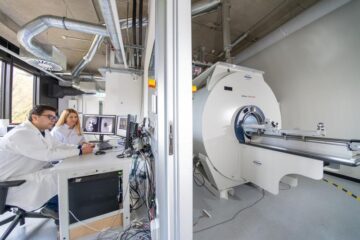
Diamantstaub leuchtet hell in Magnetresonanztomographie
Mögliche Alternative zum weit verbreiteten Kontrastmittel Gadolinium. Eine unerwartete Entdeckung machte eine Wissenschaftlerin des Max-Planck-Instituts für Intelligente Systeme in Stuttgart: Nanometerkleine Diamantpartikel, die eigentlich für einen ganz anderen Zweck bestimmt…
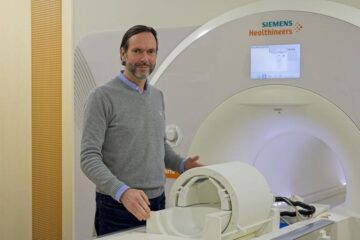
Neue Spule für 7-Tesla MRT | Kopf und Hals gleichzeitig darstellen
Die Magnetresonanztomographie (MRT) ermöglicht detaillierte Einblicke in den Körper. Vor allem die Ultrahochfeld-Bildgebung mit Magnetfeldstärken von 7 Tesla und höher macht feinste anatomische Strukturen und funktionelle Prozesse sichtbar. Doch alleine…
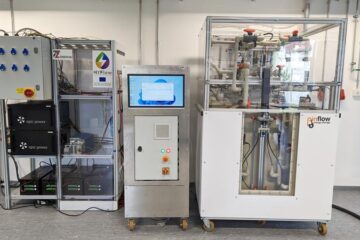
Hybrid-Energiespeichersystem für moderne Energienetze
Projekt HyFlow: Leistungsfähiges, nachhaltiges und kostengünstiges Hybrid-Energiespeichersystem für moderne Energienetze. In drei Jahren Forschungsarbeit hat das Konsortium des EU-Projekts HyFlow ein extrem leistungsfähiges, nachhaltiges und kostengünstiges Hybrid-Energiespeichersystem entwickelt, das einen…